TONGLI provides an annual production line of 50,000-350,000 tons of extruded fertilizer, using Siemens PLC control, with strong flexibility
TONGLI's roller-pressed round pellet extrusion NPK fertilizer production line has fully automated management of the entire production process from raw material feeding to finished pellet packaging. The raw materials enter the mixer through a precisely controlled automatic feeding system to ensure that the ingredients are evenly mixed. The mixed material then enters the pressing area of the high-strength alloy steel roller, where it is extruded into round pellets with a diameter of 2-5 mm through roller pressing technology, and can process up to 6 tons of material per hour. The extruded pellets enter a rapid cooling system to ensure their stable shape and texture, and then are graded through an efficient screening system to ensure that each pellet meets quality standards. The equipment consumes only 70-90 kWh of electricity for every ton of pellets produced, which is about 15-20% more energy-efficient than traditional equipment.

PRODUCTION LINE EQUIPMENT LIST

The compound fertilizer extrusion granulator extrude the mixed powdered raw materials into shape through high pressure, and is suitable for producing high-density and high-strength compound fertilizer granules. The equipment adopts double-roller extrusion technology, which can complete granulation at a lower temperature to ensure the uniformity and stability of the granules.

The compound fertilizer extrusion granulation dryer mainly uses hot air to contact the particles to quickly remove moisture from the particles after extrusion. The equipment precisely controls the temperature, humidity and wind speed to make the particles dry evenly without overheating, thereby increasing the strength of the particles to 20 Newton.

The compound fertilizer extrusion granulation cooler is used to quickly cool the hot granules to room temperature to prevent the granules from deforming or softening due to high temperature. The cooler uses strong ventilation and contact between cold air and granules.

The compound fertilizer extrusion granulation coating machine improves the anti-caking and anti-wetting properties of the granules by evenly coating the protective film. This process can improve the fluidity of the granules and prevent the granules from sticking to each other or deteriorating.
Roller Compaction Fertilizer Produciton Line ADVANTAGES
The roller is made of high-strength wear-resistant material, which extends the life by 50% and reduces the downtime of frequent replacement
Adjustable extrusion speed, flexible adjustment of extrusion speed to meet the needs of different material characteristics
The efficient screening system classifies the particles by size to ensure that each particle meets the quality standards
Using unique extrusion technology, the particle shape is uniform and the strength is increased by 20%
The batching system has an accuracy of ±0.5%, ensuring the accurate and consistent composition of each batch of products
Precise automatic feeding system to ensure accurate proportion of raw materials in each batch
Independent drying and cooling sections, drying efficiency increased by 25%
Equipped with PLC control system and touch screen human-machine interface (HMI) to achieve full process automation control and real-time monitoring
Roller Extrusion Granulation PROCESS

Raw Material Crushing
The starting point of extrusion granulation is raw material preparation. Common raw materials include potassium sulfate, monoammonium phosphate (MAP), diammonium phosphate (DAP) and urea. Powdered raw materials go directly to the subsequent steps, while blocky raw materials need to be processed by bulk crushers or double cage crushers. After reaching the required particle size, they are weighed using a belt scale. This step ensures that the raw materials meet the granulation requirements and improves product quality and consistency. The goal of the twin-roll granulation extrusion line is to optimize the physical properties of the raw materials through crushing to make them suitable for twin-roll extrusion. After crushing, the raw material particles are smaller and more uniform, which is easier to flow and improves production efficiency. This process has a significant impact on the quality, output and production efficiency of the final product, ensuring the stability and efficiency of the production line.
Raw Material Mixing
In the second process, the production line is equipped with seven high-precision belt weighing scales. The raw materials crushed to the appropriate size are sent to the chain crusher through the conveyor belt and elevator for further crushing and mixing. Then, the crushed raw materials are transported to the drum coarse screen for pre-screening by the scraper conveyor and bucket elevator. The screened raw materials enter the comprehensive weighing scale and are transported to the double-shaft mixer or vertical mixer by the elevator for final mixing to complete the raw material preparation.
Granulation
After the raw materials are prepared, they enter the granulation stage. Taking the conventional 150,000 tons output as an example, each production line is equipped with 16 extrusion granulators with an output of 0.8 tons per hour. The crushed and mixed raw materials are sent to 16 extrusion granulators through a scraper conveyor. In the machine, the raw materials are squeezed into small particles by stainless steel rollers. The particles are transported to the drum screening machine for screening through the discharge belt and the screening bucket elevator. Unqualified particles are returned to the crushing section through the return system for recycling.
Pre-Screening
The materials coming out of the granulator are of different sizes. To ensure that they are qualified, we set up a screening process. The particles enter the drum screener or vibrating screener to remove particles that do not meet the standards. Fine powder returns to the granulator through the return system, and oversized particles enter the crusher for reprocessing. Screening can improve the uniformity and quality of particles. This cycle increases production and reduces losses. 2 tons of raw materials can be recycled from 100 tons of products, increasing efficiency by 2%.
Drying
The drying system uses low-temperature, high-volume co-current drying. After the semi-finished product comes out of the extruder, it enters the drum dryer through the conveyor belt, and exchanges heat with the hot flue gas generated by the hot air furnace to remove moisture. After drying, the product temperature is 50~70 degrees and needs to be cooled by a cooler. Due to the low moisture content, the extrusion granulation dryer has a lower requirement for the temperature of the hot air furnace, usually 150~200 degrees Celsius, while the traditional process requires 250~300 degrees Celsius, showing its energy saving and flexibility.
Cooling
The cooling process is similar to the drying system. After the material comes out of the extruder, it enters the drum dryer through the conveyor belt to complete the heat exchange. After drying, the material needs to be cooled, and the temperature is usually 50-70 degrees. The low moisture content of extrusion granulation makes the hot air furnace temperature lower and the selection smaller, usually 150~200 degrees Celsius, which is more energy-saving than the traditional process.
Fine Screening
After the material is cooled, it is sent to the fine rotary screen for secondary screening through a fine screen bucket elevator. Unqualified particles are returned for granulation, and qualified finished products are weighed on a metering belt scale. The production line is set up with two screenings. The first is pre-screening to prevent unqualified particles from affecting subsequent processes. The second is fine screening to ensure the specifications of the finished product. This design ensures product quality and consistency.
Coating
The weighed finished product is processed by a coating machine to form a thin film to prevent caking. The system is equipped with an anti-caking agent conveyor, an oil injection metering pump and a metering scale. It uses DCS Siemens control to automatically adjust the amount of oil injection and powder sprinkling. After coating, the particles are sent to the automatic packaging machine through an elevator.
Packaging And Palletizing
We provide semi-automatic and fully automatic packaging solutions. The servo motor packaging scale has a speed of 800 to 1000 bags/hour, and the main components are made of high-quality materials. After packaging, the product enters the palletizing system, including automatic rewinding, with a speed of 1000 to 1200 bags/hour. An optional fully automatic pallet system can be equipped to achieve high automation.
Dust Removal System
The production line adopts two-stage dust removal, bag dust collector removes dust, and washing circulation pump sprays spray water to wash the exhaust gas. Each dust removal point is connected to the bag dust collector and FRP pipe to ensure efficient dust removal.
VIDEO
WHY CHOOSE US
The cement production line is efficient, reliable, and provides consistent quality. Customer service and support are excellent. We're highly satisfied and would recommend it.
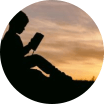
CFO
The cement production line is efficient, reliable, and provides consistent quality. Customer service and support are excellent. We're highly satisfied and would recommend it.

CEO
The cement production line is efficient, reliable, and provides consistent quality. Customer service and support are excellent. We're highly satisfied and would recommend it.

CEO
The cement production line is efficient, reliable, and provides consistent quality. Customer service and support are excellent. We're highly satisfied and would recommend it.

CEO
FAQ
The roller-pressed round pellet extrusion line is an equipment system for processing powdered raw materials into round pellets, which is widely used in fertilizer production. Its core principle is to press the raw materials into shape through the high pressure of the roller extruder.
This production line includes multiple links: raw material pretreatment, extrusion molding, particle screening, cooling and drying, and final packaging. Its equipment design is designed to improve production efficiency and product quality to meet the needs of fertilizer pellets in different markets.
Its advantages are simple operation, low energy consumption, strong adaptability, and can handle a variety of fertilizer raw materials, such as nitrogen fertilizer, phosphate fertilizer, potassium fertilizer, etc.
By adjusting equipment parameters such as roller spacing, pressure and temperature, the production line can produce pellets of different specifications to meet the fertilization needs of different crops. This production line not only plays an important role in the fertilizer industry, but can also be used in chemical industry, mineral processing and other fields, reflecting its versatility and wide application prospects.
The core equipment of the roller-pressed round pellet extrusion line is the double-roll extruder, whose working principle relies on two rollers rotating relative to each other. The raw materials are evenly fed between the rollers and pressed into dense round pellets under high pressure.
First, the raw materials are conveyed to the feed port of the double-roll extruder through a feeder. Then, under the strong extrusion of the rollers, the powdered raw materials are compressed and formed into regular pellets. These pellets are then passed through a screening device, and the pellets that do not meet the standards are separated and returned for further processing. Qualified pellets are conveyed to the next step of cooling and drying.
The whole process ensures high yield and pellet uniformity. By adjusting parameters such as roller gap, speed and pressure, the production line can flexibly produce pellets of different specifications to meet market demand. This efficient production method not only improves production efficiency, but also reduces production costs.
1) The requirements for raw materials of the roller-pressed round pellet extrusion production line are mainly concentrated on particle size and moisture content. In order to ensure the molding quality of the pellets, the raw material particles need to be uniform and fine, generally required to be less than 0.3 mm.
2) The moisture content of the raw materials is also a key factor, which should not exceed 5%. Excessive moisture may cause the pellets to stick together, affecting the molding effect and equipment operation efficiency. The raw material ingredients must have a certain plasticity and adhesion to form dense and stable pellets during the extrusion process.
3) When mixing different raw materials, pay attention to their chemical properties to avoid reactions or instability. Through scientific raw material ratios and strict quality control, it can be ensured that the produced granular fertilizers meet market standards and customer needs. Therefore, choosing the right raw materials and their processing process is the key to ensuring efficient operation of the production line and product quality.
The production capacity of roller-pressed round granule extrusion production lines is an important indicator of its efficiency, which is usually related to equipment specifications, raw material characteristics and operating conditions. In general, the production capacity of small and medium-sized production lines can reach 0.5 tons to 5 tons per hour, and large production lines can even have higher production capacity under optimized configuration.
The specific production capacity is also affected by factors such as raw material fluidity, particle size and equipment configuration. By adjusting parameters such as roller gap and speed, the production line can adapt to different production capacity requirements. In addition, by increasing the number of equipment or optimizing the process flow, the overall production capacity of the production line can also be significantly improved.
Modern production lines also use automated control systems to achieve real-time monitoring and adjustment of the production process, thereby improving production efficiency and product consistency. Stable and efficient production capacity output enables the production line to meet the market demand for fertilizers of various specifications and ingredients, while reducing operating costs and improving economic benefits.
ROLLER PRESS NPK FERTILIZER PLANT TECHNICAL PARAMETERS
Equipment Name | Capacity | Range | Quantity | Power (kW) |
Electronic Belt Scale | 1~10 tons/hour | B650, Length = 2200 mm | 8 | 1.5 + 1.5 |
Finished Product Scale | 2.5~25 tons/hour | B800, Length = 3000 mm | 1 | 2.2 + 2.2 |
Chain Mill | 25~30 tons/hour | FS800 | 1 | 7.5 kW + 7.5 kW |
Bulk Crusher | 5~12 tons/hour | PD800 | 1 | 7.5 kW |
Pre-Screener | 1.8 x 4 m | TL1840 | 1 | 10 kW |
Double Shaft Mixer | 25~40 tons/hour | TL500 | 1 | 5.5 kW |
Double Roller Extrusion Granulator | 0.6~1.2 tons/hour | ZJ800 | 16 | 3 kW |
Primary Screener | 20~25 tons/hour | 800020001500 mm | 1 | 15 kW |
Fine Screening Machine | 20~22 tons/hour | 800018001500 mm | 1 | 10 kW |
Rotary Drum Dryer | 20~30 tons/hour | 1.8 x 18 m | 1 | 85 kW |
Rotary Drum Cooler | 20~30 tons/hour | 1.6 x 16 m | 1 | 55 kW |
Rotary Drum Coating Machine | 20~30 tons/hour | 1.6*(6+1) m | 1 | 35 kW |
Automatic Packaging System | 75 tons/hour | LCS-50 | 1 | 7.5 kW |
Bagging Machine | 75 tons/hour | TL-500 | 1 | 10 kW |
Palletizing Robot | 75 tons/hour | ZJ-75 | 1 | 11 kW |