TONGLI roller press grinding system is a new type of energy-saving cement grinding equipment. It adopts material layer grinding technology. It is composed of roller press, breaking, grading, drying and powder selection. It can be combined with ball mill to form various process flows.
Tongli roller press grinding system is widely used in material grinding in cement, mining and other industries. Its main components include roller press, classifier and high-efficiency powder separator. The roller press consists of two extrusion rollers that rotate synchronously in opposite directions, one is a fixed roller and the other is a movable roller. The hydraulic system applies high pressure to the material through the movable roller, and the force can reach 500-1500 tons. The material is gradually squeezed and crushed by the high pressure. It can be combined with the ball mill to form pre-grinding, mixed grinding, semi-final grinding and final grinding systems. Due to the change of grinding principle, the roller press and its grinding system technology reduce power consumption by 50-100% and increase output by 100-300%; it is suitable for the transformation of grinding systems in new or old plants. After extrusion, the fine materials of 0.08mm account for 20-35% of the material cake, and those less than 20mm account for 65-85%. The internal structure of small particles is full of many tiny cracks due to extrusion, and the grindability is greatly improved.
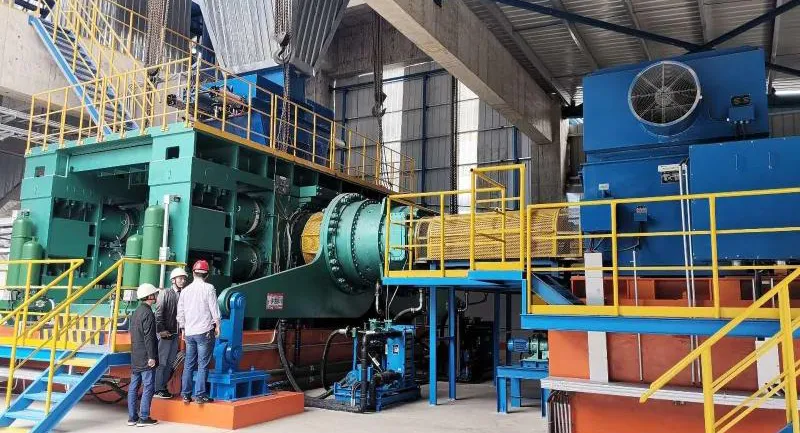
Roller Press Station EQUIPMENT LIST
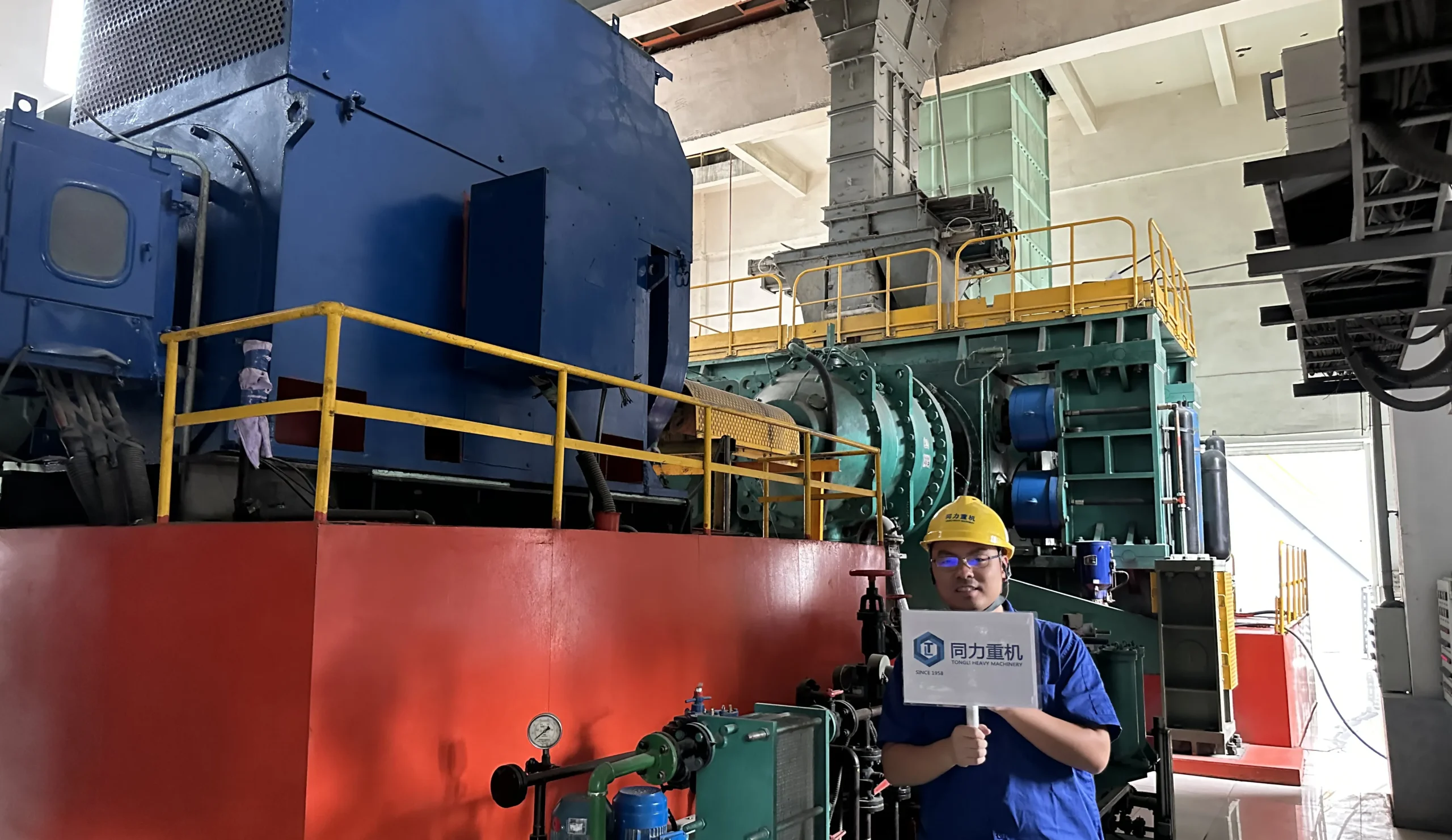
Cement raw material roller press is a kind of equipment used for raw material grinding in cement production process, mainly used to replace traditional ball mill. Through high pressure roller pressing technology, raw material roller press can compress raw materials (such as limestone, clay, iron ore, etc.) into fine powder, usually reaching 200~300 mesh.
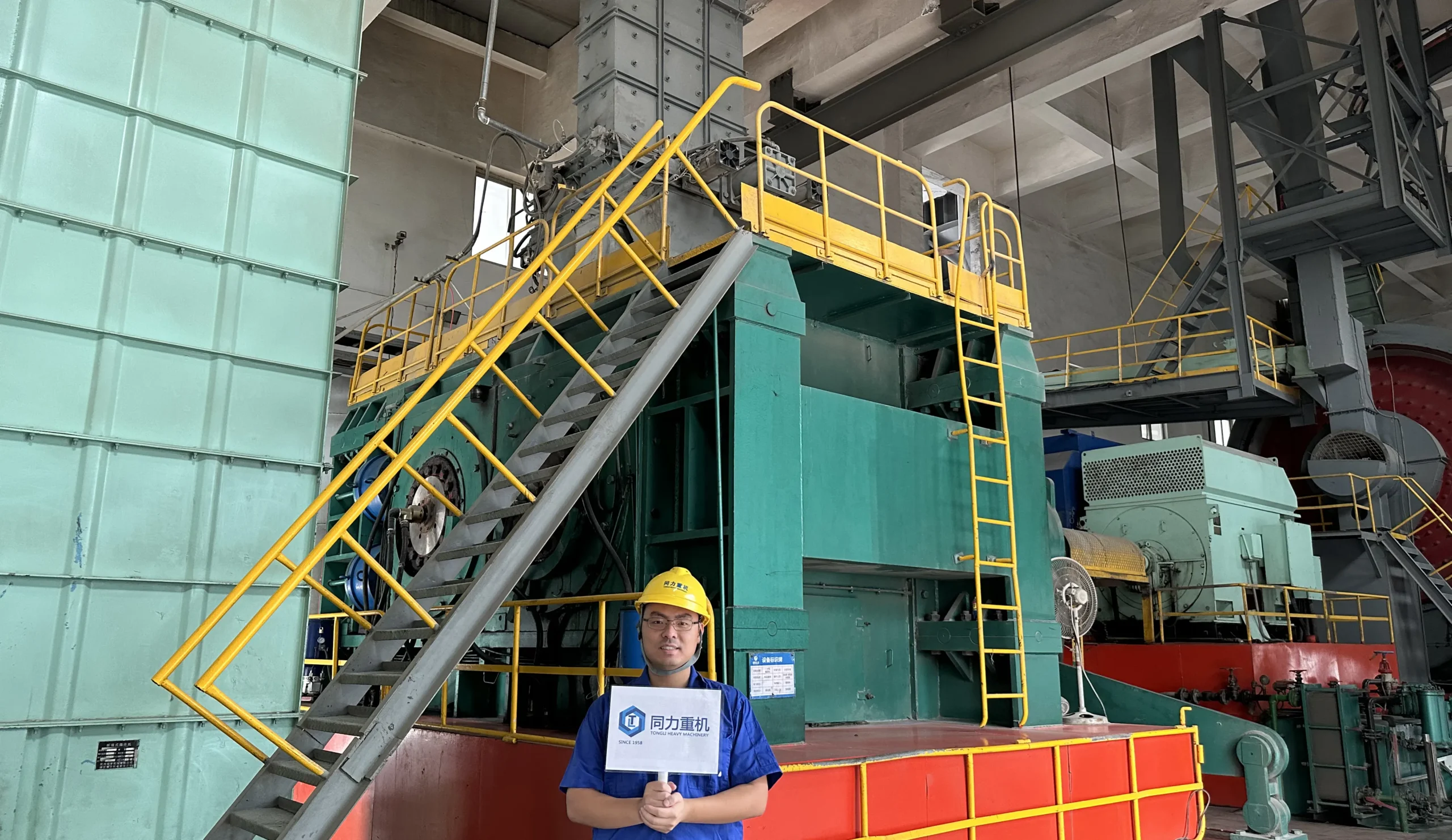
Compared with cement raw meal roller press, clinker roller press has stronger adaptability, can handle harder and stronger materials, and has excellent grinding effect on fine grinding materials with higher particle size requirements.
High Pressure Grinding Roller ADVANTAGES
Roller surface technology (welding materials, equipment and welding process) The roller surface adopts hot surfacing, and the wear-resistant layer is more convenient to repair.
The main drive motor load control of the roller press; the left and right gap deviation control and automatic deviation correction of the two rollers; fault self-diagnosis technology.
The main drive motor load control of the roller press; the left and right gap deviation control and automatic deviation correction of the two rollers; fault self-diagnosis technology.
After extrusion, about 65-85% of the material is smaller than 2mm, and the particles are full of tiny cracks, which greatly improves the grindability.
Reduce the generation and spread of microcracks in the welding process, the hardened layer has high hardness (>HRC58) and high toughness, and the service life of the roller surface is more than 8000h.
The roller press can significantly increase system output, reduce energy consumption and steel consumption, and reduce working noise.
The matching powder selector integrates aggregate cake scattering, grading, and drying, with low operating costs and high operating rates.
The roller press hydraulic system cooperates with a complete automatic control system.
ROLLER PRESS GRINDING PROCESS
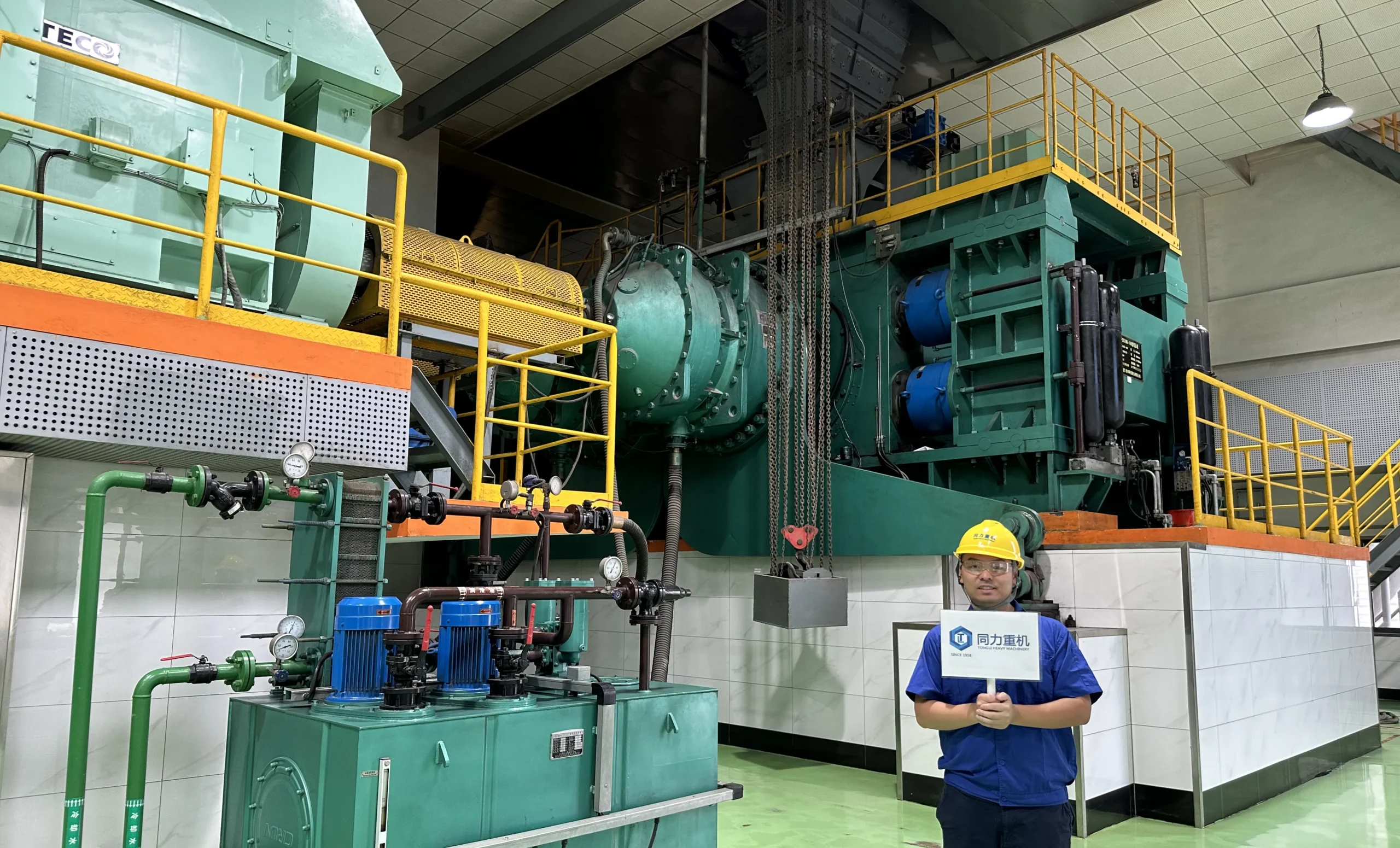
Material Pre-treatment
The material first enters the roller press for extrusion pretreatment. The roller press is designed according to the principle of material bed grinding. It consists of two extrusion rollers that rotate synchronously in opposite directions, one is a fixed roller and the other is a movable roller. The material is fed from the top of the two rollers and is continuously brought into the roller space by the extrusion rollers. After being subjected to the high pressure of 100-150MPa, it is deformed into a dense cake and discharged from the bottom of the machine.
Cake Formation And Separation
After extrusion, the material forms a dense cake with low mechanical strength and high grindability. About 60-70% of the material particles in the cake are smaller than 2 mm, and there are many microcracks, which helps the subsequent grinding process.
Grinding And Separation
The cake can be processed by a disintegrator to separate the finished product from the cake, and then sent to the powder selector for sorting. This step can further refine the material and separate and screen it as needed.
Finished Product Collection
After being sorted by the powder selector, qualified fine powder is selected, and unqualified coarse powder is returned to the roller press for reprocessing until the required fineness and quality requirements are reached. Finally, qualified fine powder is collected as the product.
System Optimization
The efficiency and output of the entire grinding system can be improved by adjusting the particle size of the roller press feed and improving the grindability of the hard-to-grind materials in the coarse powder by re-squeezing them. In addition, the operation of the entire system can be optimized by controlling the mill load to adjust the amount of fresh feed to the roller press and by using the coarse powder from the classifier to meet the stable material requirements of the roller press.
VIDEO
WHY CHOOSE US
The cement production line is efficient, reliable, and provides consistent quality. Customer service and support are excellent. We're highly satisfied and would recommend it.
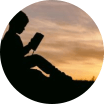
CFO
The cement production line is efficient, reliable, and provides consistent quality. Customer service and support are excellent. We're highly satisfied and would recommend it.

CEO
The cement production line is efficient, reliable, and provides consistent quality. Customer service and support are excellent. We're highly satisfied and would recommend it.

CEO
The cement production line is efficient, reliable, and provides consistent quality. Customer service and support are excellent. We're highly satisfied and would recommend it.

CEO
FAQ
The roller press grinding system uses two relatively rotating rollers to squeeze the material under high pressure, so that the material will have internal cracks between the rollers, thereby achieving the purpose of crushing.
The material enters the roller press through the feeding device and is subjected to strong pressure between the two rollers. The surface of the roller is provided with a wear-resistant layer, which can withstand high-intensity wear.
During the extrusion process of the material, the stress between the particles is concentrated, causing cracks inside the material and eventually breaking.
Compared with the traditional ball mill, the roller press grinding system has higher crushing efficiency and lower energy consumption. The operating parameters of the system, such as the pressure between the rollers, the material particle size, the feeding amount, etc., can be adjusted according to specific needs to achieve the best grinding effect. This efficient and energy-saving grinding method has been widely used in industries such as cement, mining and coal.
1) Compared with traditional ball mill system, roller press grinding system has significant energy consumption and efficiency advantages. First of all, roller press crushes materials by high pressure extrusion, which has higher energy utilization rate than ball mill's impact and grinding method.
2) Roller press has fewer wear parts and lower maintenance cost during operation. Roller press system can more accurately control the particle size distribution of materials and produce products with more uniform particle size. In addition, due to the high grinding efficiency and short grinding time of roller press system, it can greatly improve production efficiency and reduce production cycle.
These advantages make roller press grinding system have higher economic and social benefits in various industrial applications, especially in cement and mining industries, roller press has become a major grinding technology.
The roller press grinding system is suitable for a variety of materials, including but not limited to cement clinker, raw material, slag, coal, ore, etc. In the cement industry, roller presses can be used for pre-grinding and final grinding of cement clinker, significantly improving grinding efficiency and reducing energy consumption.
In the mining industry, roller presses are widely used for crushing metal ores and non-metallic ores, and high-pressure extrusion is used to make the ore reach the required fineness.
In the coal industry, roller presses can be used for the preparation of coal powder to improve the combustion efficiency of coal. In order to meet the grinding needs of different materials, the roller press can adapt to different material characteristics by adjusting operating parameters such as roller pressure, feed amount, roller speed, etc. This multifunctional feature makes the roller press grinding system have a wide range of application prospects in various industries.
1) The roller press grinding system is mainly composed of the roller press body, hydraulic system, feeding device, transmission system and control system. The roller press body is the core part of the system, including two rollers, between which the material is squeezed and crushed.
2) The hydraulic system is used to adjust the pressure between the rollers to ensure stable operation of the system and achieve efficient grinding. The feeding device is responsible for evenly feeding the material into the roller press to prevent overload or underload.
3) The transmission system drives the rollers to rotate through the motor and gear mechanism to achieve continuous crushing of the material.
4) The control system is used to monitor and adjust various operating parameters in real time, such as roller pressure, roller speed, feeding amount, etc., to ensure that the system operates in the best condition.
The coordinated work of various components makes the roller press grinding system have significant advantages in improving grinding efficiency, reducing energy consumption and maintenance costs.
1) There are many ways to improve the efficiency of roller press grinding system. First, optimize the pressure between rollers to ensure that the material is fully squeezed. Too high pressure will lead to increased equipment wear, and too low pressure will result in poor grinding effect.
2) Reasonably adjust the feeding amount and uniformity of the material to prevent overload or underload. Maintaining uniform wear of the roller surface and regularly replacing the severely worn roller surface can ensure the continuous and efficient operation of the system.
3) Optimizing the particle size distribution of the material and reducing the content of large particle materials will help improve the grinding efficiency.
4) Using advanced control systems to monitor and adjust operating parameters such as roller pressure, roller speed, feeding amount, etc. in real time can further improve the grinding efficiency of the system. Through scientific and reasonable operation and maintenance, the roller press grinding system can achieve efficient and stable operation.
In cement production, roller press grinding system is mainly used for pre-grinding and final grinding of cement clinker. In the pre-grinding stage, the roller press crushes large clinker into smaller particles through high-pressure extrusion, significantly improving the grinding efficiency of the subsequent ball mill and reducing the energy consumption of the ball mill.
In the final grinding stage, the roller press can directly grind the clinker into finished cement, improve the grinding efficiency and reduce the grinding time.
Roller press can also be used for grinding cement raw materials, slag, gypsum and other materials to improve production efficiency and product quality. In specific applications, by adjusting the operating parameters of the roller press, such as roller pressure, feed amount, roller speed, etc., the best grinding effect of different materials can be achieved.
The application of roller press grinding system in cement production not only improves grinding efficiency and reduces energy consumption, but also improves product quality, with significant economic and social benefits.
HPGR GRINDING STATION TECHNICAL PARAMETERS
Equipment Model | Roller Diameter (mm) | Roller Width (mm) | Roller Surface Speed (m/s) | Normal Working Roller Gap (mm) | Max Feeding Size (mm) | Max Feeding Temp (°C) | Pre-Crushing Capacity (Clinker, t/h) | Pre-Crushing Capacity (Raw Material, t/h) | Main Motor Model | Power (kW) | Speed (r/min) | Voltage (V) | Main Reducer Model | Total Weight (t) |
TL200-180 | Φ2000 | 1800 | 1.83 | 25-50 | 65 | ≤130 | 1000-1250 | 1050-1280 | YRKK7104-4 | 2000×2 | 1000 | ~10000 | GYM23PZN | 290 |
TL180-160 | Φ1800 | 1600 | 1.74 | 25-45 | 65 | ≤130 | 920-1120 | 920-1150 | YR6302-4 | 1600×2 | 1490 | ~10000 | GYM2292N | 250 |
TL180-120 | Φ1800 | 1200 | 1.75 | 24-45 | 65 | ≤130 | 650-750 | 700-820 | YR560-4 | 1250×2 | 1480 | ~10000 | GYM18PZN | 250 |
TL170-100 | Φ1700 | 1000 | 1.47 | 25-45 | 60 | ≤130 | 480-620 | 500-650 | YR5004-4 | 900×2 | 1485 | ~10000 | RPG29 | 208 |
TL160-140 | Φ1600 | 1400 | 1.47 | 25-45 | 60 | ≤130 | 600-720 | 650-760 | YRKK630-6 | 1120×2 | 993 | ~10000 | GYM18P2N | 212 |
TL150-100 | Φ1500 | 1000 | 1.50 | 22-40 | 60 | ≤130 | 460-500 | 480-520 | YR5002-4 | 710×2 | 1485 | ~10000 | RPG26 | 178 |
TL140-120 | Φ1400 | 1200 | 1.52 | 18-35 | 60 | ≤130 | 460-530 | 485-550 | YR500-4 | 800×2 | 1485 | ~10000 | RPG28 | 176 |
TL140-80 | Φ1400 | 850 | 1.46 | 18-35 | 60 | ≤130 | 300-350 | 320-390 | YR560-6 | 560×2 | 1485 | ~10000 | PRG23 | 125 |
TL140-70 | Φ1400 | 700 | 1.48 | 18-35 | 60 | ≤130 | 240-334 | 280-360 | YR5001-8 | 500×2 | 740 | ~600 | XGL48 | 120 |
TL140-65 | Φ1400 | 650 | 1.48 | 18-35 | 60 | ≤130 | 240-300 | 260-320 | YR5001-8 | 500×2 | 740 | ~600 | XGL48 | 115 |
TL120-60 | Φ1200 | 600 | 1.47 | 16-30 | 55 | ≤130 | 110-165 | 175-220 | Y355L-6 | 280×2 | 960 | ~380 | XGM38 | 68 |
TL120-50 | Φ1200 | 500 | 1.47 | 16-30 | 55 | ≤130 | 115-170 | 130-195 | Y315L-6 | 250×2 | 960 | ~380 | XGL38 | 64 |