
First of all let us jump to the conclusion: Although both cement and concrete are building materials, there are super obvious differences between them. Cement is used as a cementitious material, concrete is a composite material composed of multiple materials; cement has relatively low hardness and wear resistance but concrete has high strength and durability; In summary concrete is a composite made of several materials, one of them is cement. In this article we are going to introduce about what are the difference between cement and concrete in various aspects, now let's begin!
So, What is cement? the official wikipedia definition 2025

Cement is a powdery hydraulic inorganic cementitious material. It is made by mixing limestone, clay, iron ore and coal in a certain proportion, and then calcining at high temperature, grinding and other processes. After adding water and stirring, it will produce hydration (that is, the cement compound reacts chemically with water to form submicroscopic crystals or gel-like substances with high surface area) and solidify into a hard block, achieving solidification and hardening, and can adhere to other materials to bond them together. With this hydration property, construction cement that can solidify and harden even underwater is usually called hydraulic cement, of which the most important is Portland cement. Cement is widely used in construction projects such as buildings, roads, and bridges, but cement is rarely used alone. When mixed with fine aggregate, it can be made into masonry mortar, and when mixed with sand and gravel (aggregate), it can be made into concrete. Concrete is the most widely used material in existence, and it is also the largest consumption resource on the earth after water. It is an indispensable and important material for modern civil engineering.
And, What is concrete? Definition From Britannica

Concrete is an artificial stone material made of cementitious materials, aggregates (chemically inert granular materials usually sand and gravel), water and other admixtures in a certain proportion. When the aggregates are mixed with dry Portland cement and water, the mixture forms a fluid slurry, which allows concrete to be cast into various shapes and processed with various tools. The concrete slurry then solidifies into a solid over time, forming a composite material with high strength, good durability and impermeability. It can be made into components or structures of various shapes and properties by adjusting the mix ratio according to different engineering requirements. Concrete is widely used in many fields such as construction, water conservancy, and transportation. It is the second most used substance in the world (after water) and the most manufactured material. Most structural concrete is embedded with reinforcing steel bars when it is poured to provide tensile strength, thus forming reinforced concrete. Since the hydration process is exothermic, the ambient temperature plays an important role in the setting time of concrete. Typically, engineering teams add additives such as volcanic ash or high-efficiency water reducers to concrete to improve the physical properties of the wet mix and delay or accelerate the curing time, so that the concrete has enough time to be transported by pump trucks to skyscrapers hundreds of meters high.
Production process difference between concrete and cement:
Cement manufacturing process in steps:
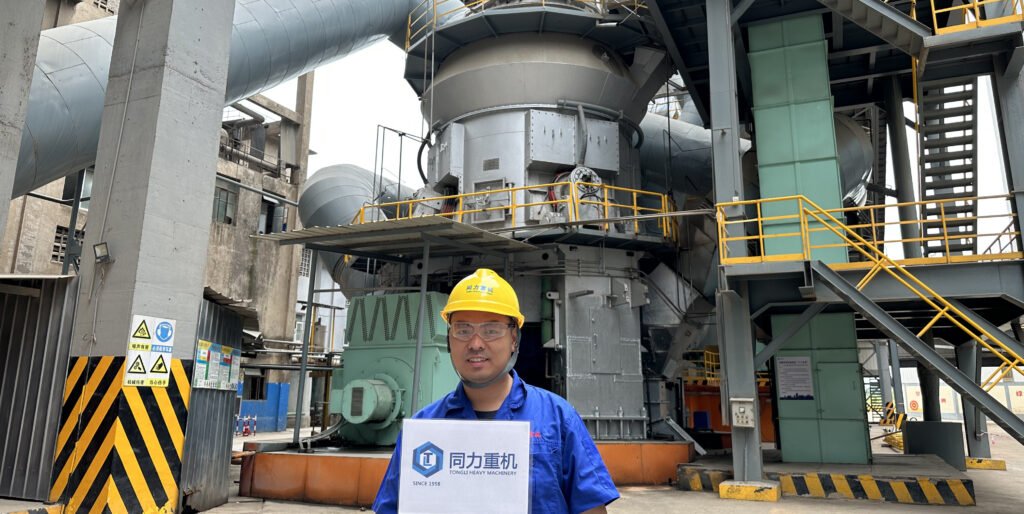
The production process of cement mainly includes the mining of raw limestone sedimentary rocks, crushing and pre-homogenization, raw material preparation, raw material homogenization, preheating and decomposition, clinker calcination, cement grinding and packaging. First, the mined limestone is mixed with clay, slag, fly ash and other raw materials, crushed and pre-homogenized to ensure uniform composition; then the raw materials are ground into raw materials by ball mill or vertical roller mill, and then homogenized to improve stability; then the raw materials enter the preheater for preheating and decomposition, and then sent to the rotary kiln for high-temperature calcination at about 1450℃ to form cement clinker; finally, the clinker is mixed with an appropriate amount of gypsum, etc., ground to a suitable fineness by ball mill or vertical mill, and packaged for shipment to make cement products.
Concrete manufacturing process in steps:

The first step in concrete production is to convey sand and gravel aggregates to the screening workshop for particle size classification via a belt conveyor, and then send powdered materials such as cement and fly ash to the metering bin via a screw conveyor and a pneumatic conveying system; then, use a DEL schenck technology high-precision electronic scale to accurately measure each material according to the mix ratio (such as C30 concrete, which contains about 350kg of cement, 650kg of sand, and 1150kg of crushed stone per cubic meter), and the PLC control system monitors in real time; then the materials enter the twin-shaft forced mixer and are mixed evenly after 60-120 seconds; the finished concrete is transported to the site by a mixer truck, pumped to the pouring site by a concrete pump truck, and after vibrating and compacting, it is cured for 7 days in an environment with suitable temperature and humidity to ensure that the strength meets the standards.
Different Uses in construction:

Compared with cement, concrete has a wider range of applications and more comprehensive performance. It not only relies on the bonding effect of cement, but also combines the characteristics of other materials such as aggregates. It is the main material that directly constitutes the building entity in construction projects, while cement focuses more on providing a bonding basis for concrete. Their differences are as follows:
- In construction, cement mainly acts as a cementitious material. It relies on the bonding force generated by its own hydration reaction to firmly bond aggregates such as sand and stone together. It is a key component of concrete. At the same time, the selection of its variety and strength grade can adjust the performance of concrete and affect the progress and quality of engineering construction. For example, fast-hardening cement can speed up the construction period, and low-heat cement can reduce the hydration heat of large-volume concrete.
- Concrete is a composite material made by mixing cement, water, sand, gravel and admixtures in a certain proportion. In the field of construction, concrete, as the main structural load-bearing body, uses high compressive strength to bear the dead weight of the building and various loads. It is the core material of foundations, beams and columns. Its durability is reflected in its ability to resist environmental erosion for a long time, and its plasticity allows it to be cast into complex shapes according to architectural design requirements. In addition, concrete can also adapt to different engineering needs by adjusting the mix ratio, such as impermeable concrete for hydraulic structures and high-strength concrete for super high-rise buildings.
Difference in curing process:
From the perspective of maintenance purpose, the maintenance of cement is mainly to ensure that its hydration reaction is fully carried out, to prevent the surface water from evaporating too quickly and affecting the strength development, and to avoid shrinkage cracks caused by drying; while concrete maintenance, in addition to ensuring that the cement is fully hydrated, also needs to ensure good bonding between the aggregate and the cement paste to prevent volume deformation and cracks caused by temperature and humidity changes. Other difference are as follows:
Curing time:
In terms of curing time, cement paste hardens relatively quickly, with an initial setting time of generally 1-3 hours and a final setting time of about 3-6 hours. Early strength develops rapidly, and curing is usually required within 1-2 days after pouring. The curing cycle is relatively short, and generally 3-7 days can basically meet the strength development requirements. Concrete has a larger volume, a large amount of cement, and contains aggregates, and the hydration reaction process is more complicated. The initial setting time is generally 4-8 hours, and the final setting time is 8-12 hours. The curing time requirement is longer. The curing time of ordinary concrete is not less than 7 days. For concrete with anti-seepage requirements or large volumes, the curing time is usually extended to 14 days or even longer.
Curing method:
cement is often used for small-area construction such as repairing and grouting. During maintenance, it is often covered with wet cloth, plastic film, etc. to keep the surface moist. For some special cement products, steam maintenance can also be used to accelerate cement hydration by increasing temperature and humidity, shortening the maintenance cycle. Concrete has a wider range of maintenance methods due to its large construction area and diverse structural forms. After the surface is pressed, watering can be used for maintenance, and the concrete surface can be kept moist by regular watering. For large-area concrete structures, such as roads and floors, curing agents can be sprayed to form a protective film on the concrete surface to reduce water evaporation. During winter construction, concrete also needs to take thermal insulation maintenance measures, such as covering with quilts, heating with electric blankets, or adding antifreeze to prevent concrete from being damaged by freezing. Although cement also needs to be protected from freezing during winter construction, its dosage and volume are relatively small, so antifreeze measures are relatively simple.
Curing monitoring:
In terms of maintenance monitoring, during cement maintenance, the main things to observe are the surface humidity and hardening state to determine whether cracking occurs; concrete maintenance requires monitoring of multiple indicators such as temperature, humidity, shrinkage and deformation. For large volumes of concrete, temperature measuring instruments are also required to monitor internal temperature changes to prevent cracks caused by large temperature differences between the inside and outside.
What are the adventages of concrete compared to portland cement?

Higher strength and durability
- High compressive strength: Concrete can withstand greater pressure. Depending on the mix ratio and production process, its compressive strength can be in the range of C10-C80 or even higher grades. It is widely used in various load-bearing structures, such as beams, columns, foundations, etc. of buildings. Although pure cement has a certain strength after hardening, it is far inferior to concrete.
- Good durability: Concrete structures have good durability and can resist natural factors such as weathering, chemical erosion, wear and tear, and various destructive effects during use, and have a long service life. In contrast, when cement is used alone, its ability to resist external damage is weak.
Better plasticity and adaptability
- Strong moldability: Concrete has good plasticity before hardening, and can be cast into components of various shapes and sizes according to engineering needs to meet the requirements of different architectural designs, such as complex curved surfaces, special-shaped structures, etc. Although cement paste also has a certain plasticity, in actual applications, it usually needs to be mixed with other materials to form a structure with a certain shape and size.
- Wide adaptability: Concrete can adapt to the requirements of different environments and engineering conditions by adjusting the mix ratio. For example, frost-resistant concrete can be used in cold regions, and corrosion-resistant concrete can be used in environments with chemical erosion. However, the performance of cement is relatively simple and it is difficult to directly meet these special requirements.
High cost performance
- High cost-effectiveness: The raw materials of concrete are widely available and the price is relatively low. Although cement is an important component of concrete, a large amount of aggregates such as sand and stone are also added to concrete, and the overall cost is relatively low. In contrast, it would be very expensive to use cement alone to build large structures.
- Low maintenance cost: Because concrete has good durability and stability, under normal use conditions, the maintenance cost is low. If cement products are exposed to harsh environments for a long time, more frequent maintenance and replacement may be required.
What are the benefits of using cement?
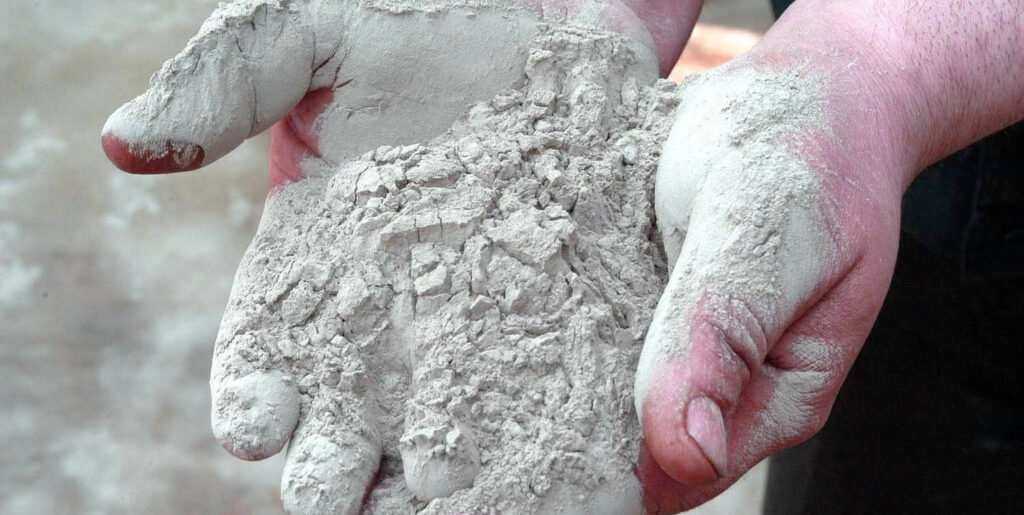
- High strength and fast hardening Ordinary Portland cement and high-grade cement have excellent early and late strength, and are suitable for cast-in-place concrete structures, prestressed projects and high-strength concrete projects. The fast setting and hardening speed is particularly suitable for scenes that require early strength or winter construction, such as rapid construction in low-temperature environments.
- Excellent durability Frost resistance: Ordinary Portland cement has a dense structure and can withstand repeated freeze-thaw cycles in cold areas. It is suitable for projects such as dam overflow surfaces and concrete pavements. Wear resistance: It shrinks when it dries, is not easy to powder on the surface, and has good wear resistance. It is often used in road projects and ground paving. Carbonation resistance: Calcium hydroxide in cement stone can effectively resist the erosion of carbon dioxide in the air, and is suitable for high CO₂ environments such as foundries.
- Construction adaptability Good plasticity: It can be cast into complex shapes before solidification to meet diverse construction needs. Strong bonding with steel bars: It is suitable for making reinforced concrete structures to improve overall stability. Thin layer construction capability (such as self-leveling cement): The thickness is only 2-8mm, which can directly cover the old ground, with high construction efficiency and no shrinkage.
- Environmental protection and economy: Bulk cement saves resources, reduces dust pollution, and has stable long-term storage strength (the grade does not decrease within 13 months), which is better than bagged cement. Raw materials are easy to obtain (such as sand and gravel), the configuration is flexible, the cost is moderate, and it is suitable for large-scale projects.
- Special functional advantages: Fireproof performance: Self-leveling cement is suitable for places with high fire protection requirements such as oil depots and power stations. Chemical corrosion resistance (specific types): For example, slag cement is resistant to sulfate erosion and is suitable for underground or seawater projects. Limitation tips: Ordinary cement has high hydration heat (not suitable for large-volume concrete) and poor corrosion resistance. The type needs to be selected according to project requirements (such as slag cement for heat-resistant projects).
What are the types of concrete?
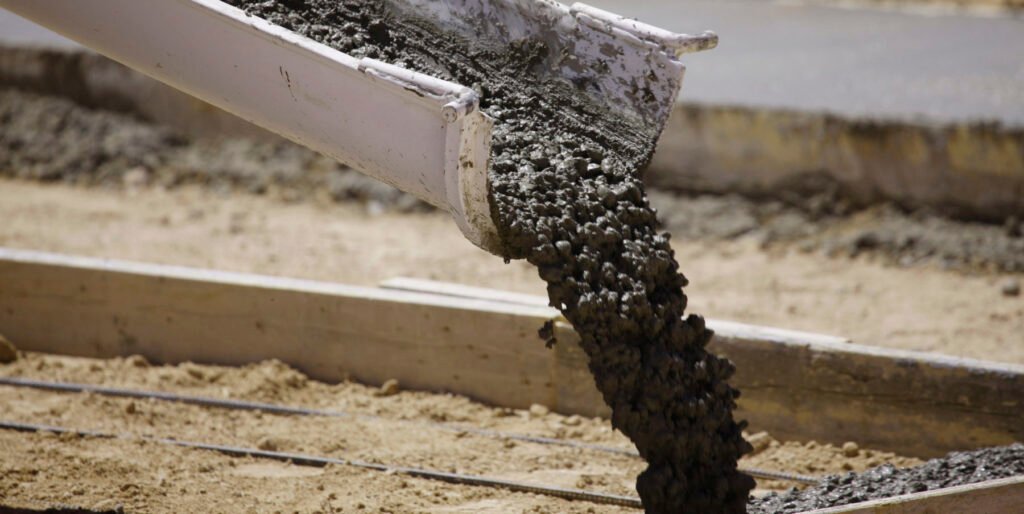
Classification by concrete grade
- C10 - C15: It is a low-strength grade concrete. C10 is generally used for some non-load-bearing foundations, foundations of secondary structures and some temporary projects. It does not require high concrete strength, but requires a certain compressive strength to bear its own weight and a small amount of additional load. C15 is often used in some structural parts with less stress, such as the foundation of small buildings, ground cushions, etc. C15 concrete is also used in some temporary buildings or simple buildings with low durability requirements.
- C20 - C35: It is a more commonly used concrete strength grade. C20 concrete is suitable for beams, slabs, columns and other components in general building structures, such as the main structures of some multi-story residential buildings, office buildings and other buildings.
- C25 and C30 concrete are more widely used. In high-rise buildings, large industrial plants, bridges and other structures, many ordinary beams, slabs, columns and foundations and other structural components will use these two strength grades of concrete.
- C35 concrete is usually used in some structural parts with higher strength requirements, such as the transfer layer of high-rise buildings, some key parts of large-span bridges, etc.
- C40 - C60: High-strength concrete grade. C40 concrete is often used in the core tube of high-rise buildings, key load-bearing components of large-span structures, and some structural parts with high durability requirements.
- C50 and C60 concrete are generally used in the main beams of large bridges, key parts of tall structures (such as TV towers, etc.), core load-bearing components of super-high-rise buildings, etc. These structures have very high requirements for the strength and durability of concrete.
- C60 and above: Ultra-high-strength concrete grade. C80 and above concrete is mainly used in some special engineering structures, such as the bottom reinforcement parts of super-high-rise buildings, large-span roof structures of large stadiums, and some special projects with strict control of the self-weight of the structure. The use of high-strength concrete can reduce the cross-sectional size of the components, reduce the self-weight of the structure, and improve the performance of the structure while meeting the structural strength requirements.
Classification by concrete density
- Heavy concrete: The apparent density is greater than 2600kg/m³, and it is made of heavy aggregates (such as barite, iron ore, etc.), cement and water. It has high density and strength, and is mainly used in radiation protection projects, such as nuclear power plants, hospital radiotherapy rooms, etc.
- Ordinary concrete: The apparent density is between 2000-2600kg/m³, and it is made of natural sand and stone as aggregates, cement, water and admixtures in a certain proportion. It is the most widely used type of concrete in construction projects, used in various load-bearing structures, non-load-bearing structures and hydraulic structures.
- Light concrete: The apparent density is less than 2000kg/m³, and it can be divided into light aggregate concrete, porous concrete and macroporous concrete. Light aggregate concrete uses light aggregate (such as expanded clay, pumice, expanded perlite, etc.) instead of ordinary sand and gravel aggregate; porous concrete contains a large number of evenly distributed tiny pores, such as aerated concrete; macroporous concrete is made of coarse aggregate, cement and water, has a larger porosity, and is often used in road bases, wall materials, etc.
Classification by construction process
- Premixed concrete: The various components of concrete are mixed in advance according to the designed mix ratio at the mixing station, and then transported to the construction site by a concrete mixer truck for pouring. It has the advantages of stable quality, high construction efficiency, and low environmental pollution, and is widely used in urban construction projects.
- Pumped concrete: Concrete that is transported to the pouring site through a pipeline using a concrete pump. Concrete is required to have good fluidity and pumpability, and usually an appropriate amount of admixtures need to be added to meet the pumping requirements. It is suitable for high-rise buildings, large-volume concrete and other projects.
- Sprayed concrete: A construction process that uses a sprayer to spray concrete mixture onto the sprayed surface at high speed to form a concrete layer. It is commonly used in tunnel lining, slope support, underground projects, etc., with the advantages of fast construction speed and timely closure of surrounding rocks.
- Roller compacted concrete: A dry and hard lean cement concrete that is compacted and formed by a vibration rolling construction process. It has the characteristics of fast construction speed, low cement consumption, and low project cost. It is mainly used in large-volume concrete projects such as dams.
Classification by application
Normal Strength Concrete
- Definition: Normal strength concrete is concrete with a compressive strength between 20MPa and 40MPa, and is one of the commonly used types of concrete in construction projects.
- Material: Made of cement, water, sand, gravel and appropriate admixtures in proportion.
- Performance characteristics: Good workability and can meet the construction requirements of concrete during mixing, transportation, pouring and vibration; Can withstand the load of general buildings and structures, and has a long service life.
- Scope of application: Used in general industrial and civil building foundations, walls, beams, slabs, columns and other structural components, and ordinary parts of infrastructure such as roads and bridges.
Reinforced Cement Concrete (RCC)
Reinforced Cement Concrete (RCC) is a structure made of concrete with ordinary steel bars, steel mesh or steel skeletons. Concrete mainly bears pressure, and steel bars mainly bear tension. The two work together by virtue of bonding force to jointly withstand external forces. Besides basic components of concrete, its constituent materials also include hot-rolled ribbed or plain round steel bars, etc., and are reasonably configured according to the structural force requirements. Reinforced concrete combines the strong compressive resistance of concrete and the tensile resistance of steel bars. It has high bearing capacity and good ductility. It can effectively withstand various loads such as static loads, dynamic loads and earthquakes, and has good durability and fire resistance. Because of this, it is suitable for buildings and civil engineering structures such as high-rise buildings, large-span bridges, hydraulic structures, underground structures, etc.
Prestressed Concrete
Prestressed concrete is a structure that applies compressive stress before the concrete components are subjected to external loads, so that the tensile stress areas generated during the use stage are compressed first to improve crack resistance and rigidity. In addition to ordinary concrete materials, its components also require high-strength prestressed steel bars (such as steel strands, steel wires, etc.) and special anchors and clamps. It can control the development of cracks in components, improve crack resistance and rigidity, reduce deformation, give full play to the performance of high-strength materials, reduce cross-sectional dimensions, reduce deadweight, and save materials. It is suitable for structures with large spans, heavy loads, and high requirements for deformation and crack resistance. It is often used in large-span bridges, large industrial plant trusses and crane beams, high-rise building transfer layers, hydraulic structures, and special building structures with high requirements for structural performance.
High Performance Concrete,HPC
High-performance concrete (HPC) is a new type of high-tech concrete made with modern concrete technology. Its constituent materials usually include high-quality cement, high-efficiency water-reducing agent, silica fume and other mineral admixtures and high-performance coarse and fine aggregates, and the quality and mix ratio of raw materials are strictly controlled. It has high durability and can resist various environmental erosions; it has good workability, high fluidity and cohesion, and low water seepage, which is convenient for construction; it has high strength, and the compressive strength is often above 60MPa; it has high volume stability, and small shrinkage and creep during hardening. It is suitable for special projects with high durability and strength requirements, such as marine engineering, ports, high-rise buildings, large-span bridges, nuclear power plants, etc., as well as projects in harsh environments.
Of course there could be more types listed according to different category but due to the time limit we just gonna stop here and continue to introduce about the types of cement.
What are the common types of cement?

Common types of portland cement:
- Ordinary Portland Cement: This is the most common type of Portland Cement, suitable for general construction projects, such as the pouring of foundations, walls, beams, columns and other structures of buildings, and can meet the strength and durability requirements of most conventional buildings.
- Rapid Hardening Portland Cement: This type of cement is characterized by fast setting and hardening speed and rapid early strength growth. It is suitable for emergency repair projects, winter construction projects and special projects with high early strength requirements. It can achieve higher strength in a shorter time and meet the needs of project progress.
- Low Heat Portland Cement: It has lower hydration heat and generates less heat during the hydration process. It is mainly used in large-volume concrete projects, such as dams and large foundations. It can effectively reduce the temperature rise caused by hydration heat inside the concrete, reduce the generation of temperature cracks, and ensure the stability and durability of large-volume concrete structures.
- Sulfate-resistant Portland Cement: It has high resistance to sulfate erosion. It is suitable for environments subject to sulfate erosion, such as seaport projects, hydraulic structures in water conservancy projects, underground projects, etc. It can resist the erosion and damage of sulfates on cement stone and extend the service life of engineering structures.
- White Portland Cement: also known as white cement, it is white in color and is mainly used in architectural decoration projects, such as wall and floor decoration, making white cement products, colored cement, and art sculptures to meet the requirements for the appearance and decoration of buildings.
- High-aluminum Portland Cement: Contains a high content of alumina and has the characteristics of fast hardening, high strength, and high temperature resistance. It is suitable for some special projects, such as the lining of high-temperature furnaces and heat-resistant projects for emergency repairs, but it is necessary to pay attention to its use conditions and restrictions when using it, because strength shrinkage may occur in some cases.
Common types of cement by grading:
- Portland cement: Strength grades are divided into six grades: 42.5, 42.5R, 52.5, 52.5R, 62.5, and 62.5R. Among them, R represents early strength cement, which has higher 3-day compressive strength and flexural strength than ordinary cement of the same grade, and can reach the strength requirements of the project more quickly, and is suitable for projects with high early strength requirements.
- Ordinary Portland cement: Strength grades are divided into four grades: 42.5, 42.5R, 52.5, and 52.5R. The strength growth of ordinary Portland cement is relatively balanced, which can meet the strength requirements of general building structures at different construction stages and is widely used in various industrial and civil construction projects.
- Slag Portland cement, volcanic ash Portland cement, fly ash Portland cement and composite Portland cement: The strength grades of these cements are divided into six grades: 32.5, 32.5R, 42.5, 42.5R, 52.5, and 52.5R. Grade 32.5 cement is suitable for some projects with relatively low strength requirements, such as general masonry projects, non-load-bearing wall materials, etc.; grades 42.5 and 52.5 can be used for general concrete structure projects, such as beams, slabs, columns and other structural components of multi-story buildings.
Common types of cement by materials composition:
Ordinary Portland cement:
OPC is made by grinding Portland cement clinker, 6% - 15% mixed materials and appropriate amount of gypsum, which is a naturally occurring sulfate mineral compound. The 28-day compressive strength of concrete prepared with OPC is 33 MPa, 43 MPa and 53 MPa, respectively called OPC 33, OPC 43 and OPC 53. Its performance is similar to that of Portland cement, with high early strength, fast setting and hardening speed, good frost resistance, etc. It is suitable for general industrial and civil construction projects and is one of the commonly used cement varieties in construction projects.
Portland Pozzolana Cement (PPC):
Pozzolanic silicate cement: It is made by grinding silicate cement clinker, volcanic ash mixed materials and appropriate amount of gypsum. It has good impermeability and water resistance, low hydration heat, and is suitable for large-volume concrete projects, concrete projects with impermeability requirements, and general above-ground, underground and underwater concrete projects. However, it has low early strength, slow coagulation and hardening speed, large shrinkage, poor frost resistance and wear resistance.
Portland Slag Cement (PSC):
Slag Portland cement: Made by grinding Portland cement clinker, granulated blast furnace slag and appropriate amount of gypsum. It has good heat resistance, water resistance and sulfate erosion resistance, low hydration heat, and is suitable for large-volume concrete projects, high-temperature workshops and concrete structures with heat resistance requirements, as well as general above-ground, underground and underwater concrete projects. However, it has low early strength, slow coagulation and hardening speed, and poor frost resistance.
Others:
- Portland cement: Made by grinding Portland cement clinker, 0% - 5% limestone or granulated blast furnace slag, and appropriate amount of gypsum. It has high early strength, fast setting and hardening, and good frost resistance. It is suitable for important structures in general construction projects, such as foundations, beams, columns and other structural parts of high-rise buildings and large-span bridges. However, it has high hydration heat and poor corrosion resistance, and is not suitable for large-volume concrete projects and projects affected by corrosive media.
- Fly ash silicate cement: It is made by grinding silicate cement clinker, fly ash and appropriate amount of gypsum. It has the characteristics of small shrinkage, good crack resistance, low hydration heat, etc. It is suitable for large-volume concrete projects, hydraulic concrete projects, and general industrial and civil construction projects. Above-ground, underground and underwater concrete structures. However, the early strength is low, the setting and hardening speed is slow, and the frost resistance is poor.
- Composite Portland Cement: It is made by grinding Portland cement clinker, two or more specified mixed materials and an appropriate amount of gypsum. Its performance depends on the type, dosage and proportion of the mixed materials. It combines the characteristics of a variety of mixed materials and has good adaptability. It can be used in general construction projects.
- Rapid-hardening Portland Cement: It is made by grinding Portland cement clinker and an appropriate amount of gypsum. It has the characteristics of fast early strength growth and is suitable for emergency repair projects, winter construction projects and special projects requiring high early strength.
- Low-heat Portland Cement: It has a low hydration heat and is suitable for large-volume concrete projects, such as dams and large foundations. It can effectively reduce the temperature increase caused by hydration heat inside the concrete and reduce the generation of temperature cracks.
- Anti-sulfate Portland Cement: It has a high resistance to sulfate erosion and is suitable for seaport projects, water conservancy projects and underground projects that are eroded by sulfates.
- White Portland Cement: also known as white cement, it is white in color and is mainly used in building decoration projects, such as wall and floor decoration, making white cement products and colored cement, etc.
- Road Portland Cement: It has good wear resistance, flexural strength and frost resistance, and is suitable for road pavement, airport runway and other projects.
Again, there are many types of cement, but in order not to bore you, we will list the above
Cement Vs Concrete Frequently Asked Question(FAQ)
What is the Concrete Mixing Process?
The concrete mixing process is the process of mixing raw materials such as cement, water, sand, stone and admixtures to make uniform and qualified concrete. First of all, the raw materials should be accurately weighed according to the designed mix ratio, which is the key to ensure the performance of concrete. Then, aggregates such as sand and stone are put into the mixer and dry mixed for a period of time to make them preliminarily mixed and uniform. Then cement is added and continued to be stirred to make the cement evenly distributed in the aggregate. After that, an appropriate amount of water is added and stirred at the same time to make the cement hydrate and form a slurry with fluidity and plasticity, which is wrapped on the surface of the aggregate and bonds the aggregate together. In this process, admixtures are added as needed, such as water reducers to improve the fluidity of concrete, retarders to prolong the setting time of concrete, etc. Through continuous stirring, the admixtures can be fully utilized to make the concrete meet the designed workability, strength and durability and other performance requirements. The mixing time should be reasonably determined according to factors such as the type of mixer, concrete mix ratio and slump, generally around 90-180 seconds, to ensure that the concrete is mixed evenly and the components are fully mixed.
Cost and Availability of cement and concrete
- Cement: The average price of cement in the United States in 2024 is about $160 per ton. Globally, the price of cement in Norway is higher, at $0.49 per kilogram, while in Nigeria it is lower, at $0.06 per kilogram. The average price in 41 countries is $0.21. Conventional cement is in stable supply in most regions, but special cement is difficult to obtain.
- Concrete: The average cost of concrete in the United States in the first half of 2024 is between $150 and $180 per cubic yard, with an average price of $166.39 per cubic yard. Concrete is easily available in cities and surrounding areas, but may be insufficient in remote areas. Special high-performance concrete is more limited in availability due to its high production requirements.
The Role of Cement in Concrete
In concrete, cement plays a core role. In terms of dosage, cement usually accounts for 10% - 15% of concrete by volume, combined with 20% water and 75% sand and gravel aggregates. Cement and water are mixed to produce hydration products with bonding force, such as hydrated calcium silicate gel, which firmly bonds sand and stone aggregates and gives concrete strength. Its strength development determines the growth of concrete strength. At the same time, cement particles can fill the gaps in aggregates and improve the density of concrete. Different types of cement, such as ordinary Portland cement and slag Portland cement, have different performances in terms of hardening speed and durability due to differences in mineral composition, affecting the performance of concrete to adapt to various projects.
How does the cement-to-water ratio affect concrete quality?
The water-cement ratio (mass ratio of cement to water) has a significant impact on the quality of concrete. If the water-cement ratio is too high, such as exceeding 0.6, the concrete mixture will be too fluid, resulting in increased porosity and reduced strength after hardening. For example, the 28-day compressive strength of concrete may drop from the designed C30 to around C20. At the same time, the impermeability and frost resistance will also deteriorate. If the water-cement ratio is too low, such as less than 0.4, the concrete mixture will be too dry and hard, difficult to vibrate and compact, and prone to defects such as honeycomb surface, which also affects strength and durability. Generally speaking, the water-cement ratio of ordinary concrete is more suitable between 0.4 and 0.6.
What types of projects require concrete versus cement?
Cement, as a powdery cementitious material, is often used in small repair projects, masonry mortar, and as a basic raw material for preparing concrete, such as road crack repair and wall jointing. The amount of cement used per cubic meter of mortar is about 300-400kg. Concrete is a composite material mixed with cement, aggregates, etc., and is widely used in various large-scale construction projects, such as the foundation and main structure of high-rise buildings. The compressive strength of concrete with strength grades of C30-C40 can reach 30-40MPa; the beams of large-span bridges require high-strength concrete of C50-C60 to ensure the structural bearing capacity; large-volume projects such as hydraulic dams often use low-heat concrete, which has a low cement hydration heat and can effectively avoid temperature cracks. The amount of cement used per cubic meter of concrete is about 150-250kg.
Cement cannot be used directly, mainly because its single-use performance is limited. Although cement can harden after adding water, it is brittle after hardening, with a compressive strength of only about 10-20MPa and a lower tensile strength (generally less than 3MPa), which cannot meet the strength and toughness requirements of building structures. At the same time, cement shrinks greatly when hardening, and direct use is prone to produce a large number of cracks. After being made into concrete with aggregates such as sand and gravel in a certain proportion, the compressive strength can be increased to 20-80MPa, which can meet the needs of different buildings. In addition, cement alone is expensive and difficult to form large-volume components, so it is rarely used directly in construction.
In terms of building structures, concrete is used for beams, slabs, columns and foundations of residential buildings and office buildings. For example, the foundations of general buildings mostly use C20-C30 concrete. In road engineering, whether it is the pavement of urban roads and highways, or the piers and bridge decks of bridges, it is indispensable. For example, cement concrete with high flexural strength is often used on highway pavements. In water conservancy facilities, dams and sluices are constructed with concrete and can withstand water pressure and water flow impact. In addition, airport runways, port terminals, tunnel linings, and even protective walls and fences will also use concrete because of its high strength, good durability, and easy construction.
Concrete production is the process of mixing cement, aggregates (sand, stone), water and admixtures in a specific proportion. Taking the common C30 concrete as an example, the proportion per cubic meter is approximately 350-400 kg of cement, 600-700 kg of medium sand, 1100-1200 kg of crushed stone, and 170-200 kg of water. Aggregates and cement are first put into a mixer for dry mixing, and then water and admixtures are added for wet mixing. The mixing time is controlled at 90-120 seconds, so that the concrete can achieve the workability, fluidity and other properties required by the design, and form a mixture that can be used for pouring construction.
Concrete has a longer service life. After hardening, cement is mainly a gel. Although it has a certain strength, it is easily damaged by external factors when used alone. Under normal conditions, the service life of pure cement products is mostly 10-20 years. Concrete uses cement as a gelling material and adds aggregates such as sand and gravel, which greatly improves its density and strength. For example, C30 concrete can have a service life of 50-100 years in building structures under normal use and maintenance. High-performance concrete for special projects can have an even longer service life with appropriate protective measures, because aggregates enhance the overall structural stability and durability.
The proportions of cement, sand and coarse aggregate in different grades of concrete are different. Taking the common C20, C30 and C40 concrete as examples, the C20 concrete mix ratio is generally cement: sand: coarse aggregate = 1:2.41:4.47, with a water-cement ratio of 0.61; C30 concrete is about 1:1.76:3.33, with a water-cement ratio of 0.44; C40 concrete is about 1:1.42:2.97, with a water-cement ratio of 0.37. These proportions will be appropriately adjusted according to factors such as raw material characteristics and construction requirements to meet the different strength and performance requirements of concrete.
The compressive strength test of cement/concrete is to make cement paste or concrete into standard size specimens (such as cement 40mm×40mm×160mm prism, concrete 150mm×150mm×150mm cube), and after curing to a specific age in a specified temperature and humidity environment, apply pressure through a pressure testing machine until the specimen is destroyed, record the failure load and calculate the compressive strength value. This test is a key indicator for evaluating the quality of cement and concrete. The 3-day compressive strength of ordinary Portland cement is generally not less than 17MPa, and 28 days is not less than 42.5MPa; the standard value of the 28-day compressive strength of C30 concrete is 30MPa. The test results can determine whether the material meets the design and construction requirements, ensuring the safety and reliability of the building structure.
The base materials of concrete mainly include cement, aggregates, water and admixtures. Cement is a cementitious material. Commonly used silicate cement strength grades are 42.5, 52.5, etc. Its hydration reaction gives concrete strength. Aggregates are divided into fine aggregates (such as natural sand, with a particle size less than 4.75mm) and coarse aggregates (such as crushed stone, with a particle size greater than 4.75mm), accounting for about 60%-75% of the volume of concrete, affecting its strength and durability. Water and cement undergo hydration reactions, and the water-cement ratio (generally between 0.4 and 0.6) directly affects the strength. Admixtures such as water reducers are usually added in an amount of 0.5%-2% of the cement mass to improve the performance of concrete. These base materials jointly determine the final performance of concrete.
Cement is usually not used alone, but as a cementing material for concrete or mortar. In actual engineering, cement is often mixed with sand, gravel, water, etc. in proportion to make concrete or mortar before application. Pouring is the most common construction method. For example, when pouring the foundation and beams of a building, concrete is poured and filled after formwork support. The pouring speed of C30 concrete is about 10-20 cubic meters per hour. Spraying technology is often used in tunnel lining, slope support, etc. Concrete is sprayed onto the construction surface at a speed of 60-100m/s by a concrete sprayer, which can quickly form and tightly combine with the base. At present, there is no professional corresponding process for "Sprouting" in cement application.
The selection of cement and concrete depends on the project requirements. Cement plays a bonding role and is used in masonry mortar, plastering, repair projects, etc. For example, in small repair projects, cement paste can quickly fill gaps. Its strength is generally between 32.5 and 62.5MPa. Concrete is a composite material composed of cement, aggregates, etc. It has high compressive strength. The standard value of C30 concrete compressive strength is 30MPa. It is suitable for load-bearing structures such as beams, slabs, and columns of buildings, as well as large projects such as roads and bridges. If you need to build a structure that bears a large load, concrete should be given priority; if it only needs to play a bonding and repairing role, cement is more suitable.
Nooooo waaaaaaay! Cement is a powdery cementitious material with limited strength after hardening. The 28-day compressive strength of its mortar specimen is usually between 32.5 and 62.5 MPa (corresponding to cements of different strength grades). Concrete is a composite material formed by mixing cement as a cementitious material with sand and gravel. The standard compressive strength of C20-C80 concrete is between 20 and 80 MPa. The compressive strength of C30 concrete commonly used in actual projects can reach more than 30 MPa. With a reasonable mix ratio, concrete can give full play to the bonding effect of cement and the skeleton effect of aggregates, and its overall strength is much higher than that of a single cement hardened body.
Generally speaking, cement is cheaper than concrete. For example, the price of common ordinary Portland cement is generally $200-400 per ton, which is about $0.1-0.2 per pound. Concrete is a mixture of cement, aggregates (sand, stone, etc.), water and admixtures. For example, C30 ordinary concrete costs $100-150 per cubic meter. Due to the low cost of aggregates, the overall price is lowered after amortization. However, if special cements such as white cement and rapid hardening cement are used, the price will increase significantly due to their complex production process, and may even be higher than ordinary concrete.
Cement is suitable for a variety of engineering scenarios. In construction projects, masonry mortar often uses cement with a strength grade of 32.5MPa, which can meet the bonding requirements of ordinary wall masonry; for non-load-bearing structures and ground cushions of general buildings, 42.5MPa ordinary Portland cement is often used in C15-C20 concrete. In road projects, 32.5MPa cement can be used to enhance the stability of road base stabilized soil; and when making road concrete prefabricated components, 52.5MPa high-strength cement can ensure that the component strength meets the standard. In small repair projects, such as tile joints and local damage repairs, 32.5MPa cement can meet the requirements.
Concrete is suitable for a variety of scenarios due to its excellent performance. When it needs to bear a large load, such as the foundation and beams of high-rise buildings (C30-C60 strength grade), its high compressive strength characteristics are used; in the construction of long-span bridges (C40-C80), it can meet the requirements of structural strength and durability; hydraulic structures such as dams and pools require highly impermeable concrete (impermeability grade P6-P12); during road pavement construction, wear-resistant and flexural-resistant concrete (C30-C40) can ensure long-term use; in special projects such as nuclear power plants that require extremely high durability, high-performance concrete can resist erosion in complex environments and extend the service life of the structure.
Conclusion:
To summrize it, cement is a powdered substance primarily used as a binder, concrete is the final construction material formed by mixing cement with water, sand, and coarse aggregates. More specifically, conncrete is a combination of stone (rock, gravel), sand, portland cement and water, in descending order of the amount of each material in the mix. Simply put cement is a powdered, hydraulic, inorganic cementitious material. Common Portland cement is made by mixing raw materials such as limestone, sand, bauxite, and gypsum. These materials are heated until they are completely melted and then cooled. The product after cooling is called clinker. The clinker is ground into a fine powder, which we call Portland cement. Their functions are completely different: cement acts as a bond, firmly combining various materials together; concrete, with its good plasticity and high strength after hardening, is directly used to construct the structure, walls, floors and other physical parts of a building. It is the main material for realizing building functions and load-bearing.