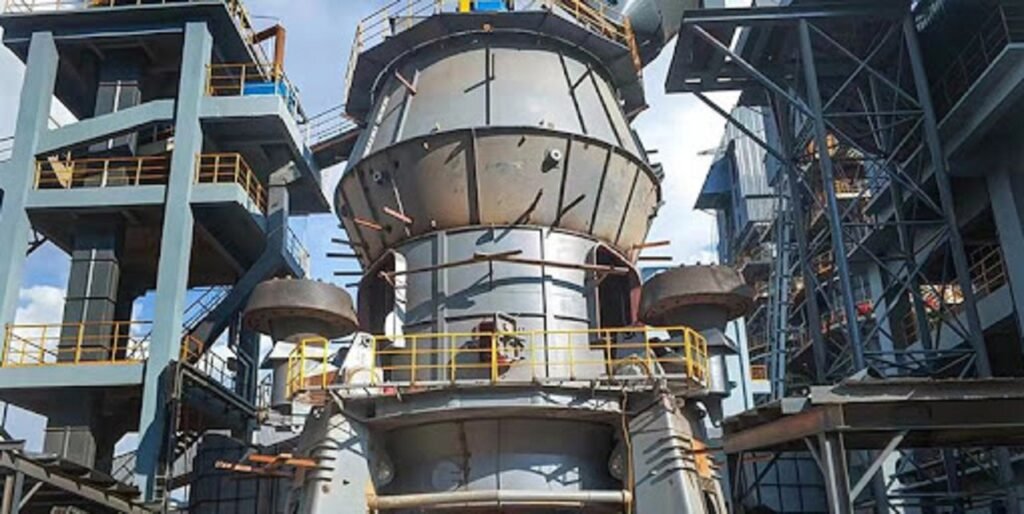
Introduction: FLsmidth Atox50 VRM Upgrade
TONGLI's customer has a 5,000t/d cement clinker production line, equipped with a FL-Smith ATOX50 raw material vertical mill system. The actual clinker output is 5,800t/d, and the raw material hourly output is about 425t/h. In order to fully tap the potential of the original equipment, reduce indicators such as clinker coal consumption and electricity consumption, and improve economic benefits, in 2021, TONGLI carried out production improvement transformation of the sintering system and the raw material grinding vertical mill system. The transformation goal is to achieve a clinker output of 6,800t/d and a raw material vertical mill hourly output of more than 470t/h. After the upgrade was completed, the clinker system quickly reached full production and met the standards, but the raw material vertical roller mill system did not meet the expected production increase. After the secondary upgrade of TONGLI, it finally achieved a relatively ideal capacity, met the needs of the sintering system after production increase, and reduced the raw material power consumption, achieving good results. The process of our company's ATOX50 raw material vertical mill production upgrade technical transformation is summarized for your reference.
Raw material analysis and ATOX50 equipment specification:
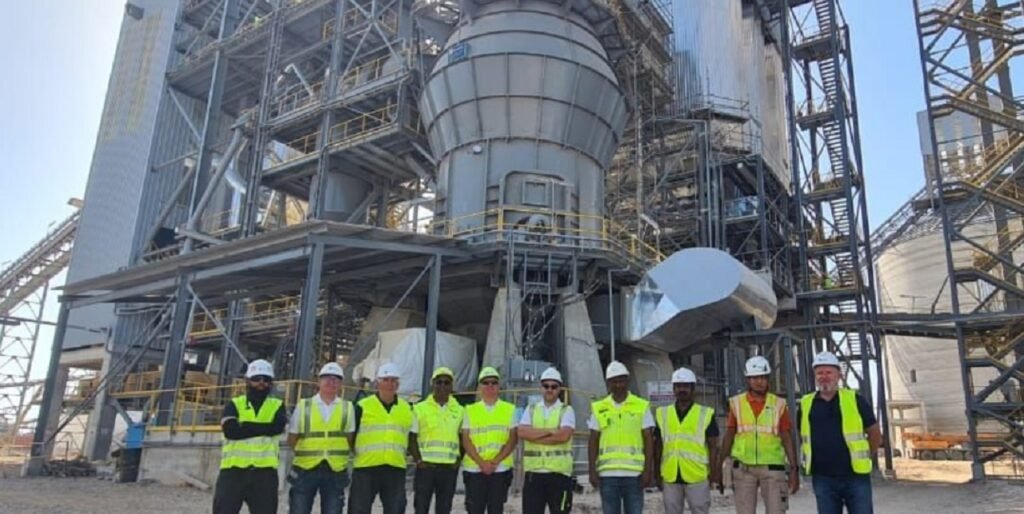
Raw material:
The raw material is limestone, but the quality is poor and the proportion is high; in addition, hard sandstone is used as the raw material, and the overall grindability of the material is poor. Before the upgrade, the average raw material hour in 2020 was 424t/h, the raw material power consumption was 16.37kWh/t, the fineness was controlled at 20% of the 80 sieve residue, the mill vibration value was 1.3mm/s on average, and the working condition was stable, which was at a normal level compared with the same type of domestic vertical mills.
Raw material composition table for atox mill:
Variety | Limestone | Sandstone | Bauxite | Sulfuric Acid Slag | Total |
Proportion /% | 90 | 6.5 | 0.5 | 3 | 100 |
Particle Size /mm | 80% ≤ 80, particle + block, maximum 100 | maximum 100 | ≤ 80 | Powder | |
Moisture /% | 1 | 7 | 2 | 20 | 2, maximum ≤ 3 |
Atox 50 vertical roller mill raw meal equipment specification:
Equipment | Details |
Vertical Mill | Model: ATOX50; Motor: YRKK900 - 6, 3800kW; Reducer: WPU200C, \(i = 39.8\) |
Powder Separator | Model: RAR - LV52.5; Motor: YSP355M2 - 4, 232kW; Reducer: B3SV11B, \(i = 25.19\) |
Circulating Fan | Air Volume: \(783071m^3/h\); Total Pressure: 11580Pa; Motor: YRKK900 - 6, 3800kW (Energy - saving renovation was carried out in 2017) |
Cyclone | 4 units, Diameter: 5600mm (Manufactured according to the drawings provided by Smith) |
So above are the basic parameters of the atox 50 mill that we carried out the upgrade. After the target of increasing the production of vertical mill was determined, we first communicated with FL-smidth, the original manufacturer of ATOX50 vertical mill. The other party suggested that the production be increased by modifying the powder selector to improve the powder selection efficiency and increase the grinding pressure, but the expected increase in production was small, and it could not be guaranteed that the needs of the kiln system could be met after the modification. Therefore, TONGLI finally chose a series of new technologies such as NU type powder selector, low resistance air ring, and middle shell air supply. These technologies have been widely used in Tongli ZJTL and TRM vertical mill systems. After the modification, the production was greatly increased, and the power consumption was greatly reduced. After a field investigation, the customer finally chose to carry out the modification according to TONGLI's technical solution.
Upgrade detail of the FL-smidth Atox 50 raw material grinding vertical roller mill
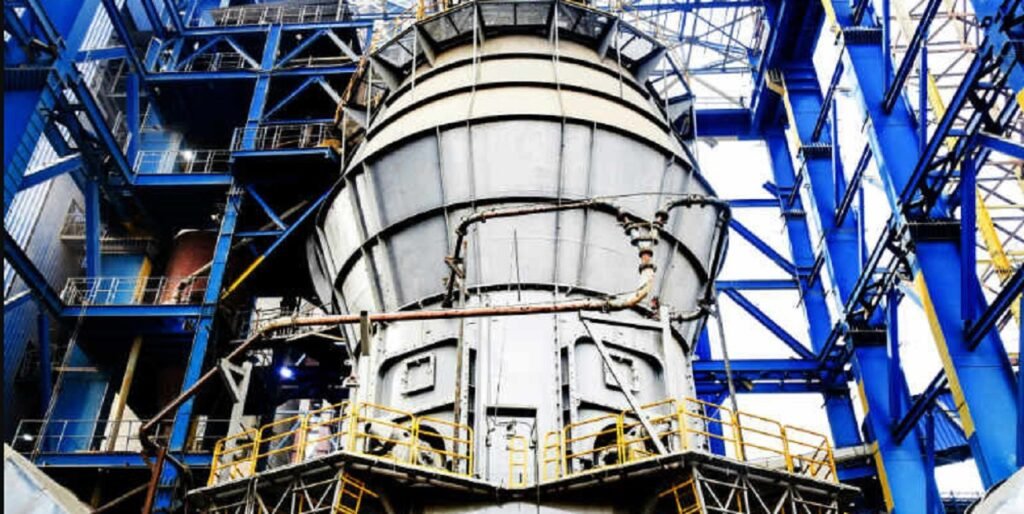
After the below modifications were implemented, the system output was stabilized to about 445t/h after nearly 3 months of debugging by adjusting the height of the retaining ring and the ventilation area of the air ring and increasing the grinding pressure and so on. Now let us explain it in detail:
Powder classifier upgrade:
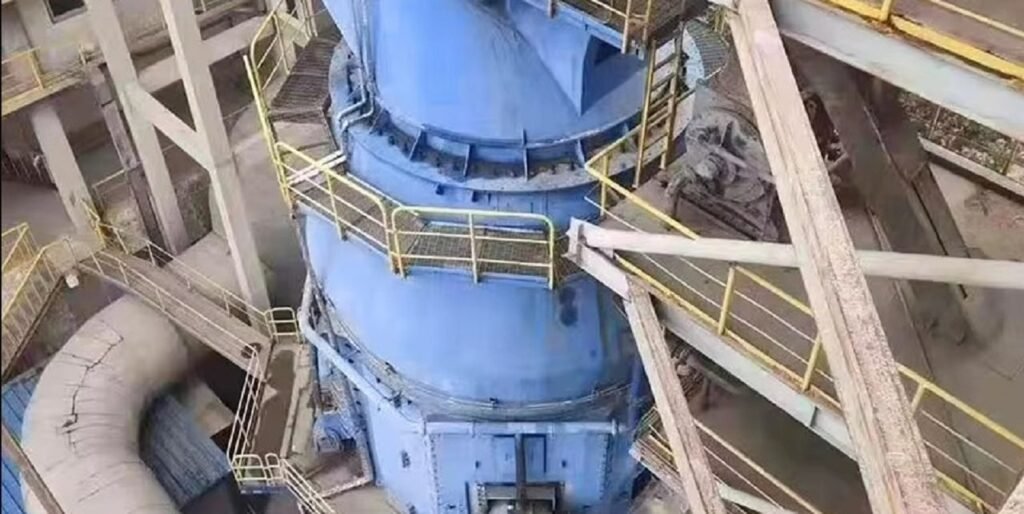
The powder selector was replaced with the NUR6033 powder selector, retaining the original transmission device, rotor shaft, and air outlet, and replacing the rotor, air guide blades, housing, and return cone. The special U-shaped rotor blades of the powder selector have lower resistance and higher powder selection efficiency than the straight blades under the same working conditions, which can reduce the circulation load, help increase system output, and reduce power consumption.
Forcible air circulation installed:
A new middle shell air supply device was added. A 1m diameter air duct was introduced from the top of each of the two hot air inlet pipes to the housing above the vertical mill spokes, so that part of the hot air does not pass through the air ring and directly enters the mill. An electric shutter valve was installed in the middle of the pipe to adjust the air volume. The starting point of this technology is to solve the contradiction between the air volume of powder selection and the air volume of grinding. Under the condition of ensuring the air volume for drying and subdividing and lifting, the air volume of the air ring is reduced as much as possible. When the air volume of powder selection is insufficient, the middle shell air supply pipe is provided. On the one hand, the resistance of the air ring is reduced, and on the other hand, the amount of unqualified coarse powder entering the powder selection machine can be reduced, thereby improving the powder selection efficiency, reducing the amount of return powder, stabilizing the material layer, and improving the grinding efficiency.
Replace air guide ring with low resistence wedge type:
The original straight plate type air guide ring is replaced with a low resistance wedge plate air guide ring. The wedge-shaped air guide plate is a double-layer structure, wide at the top and narrow at the bottom. It has an accelerating effect when the air flow passes through. Under the condition of lifting the same amount of material, the air volume is smaller, providing conditions for the use of middle shell air supply.
Feeding device upgrade:
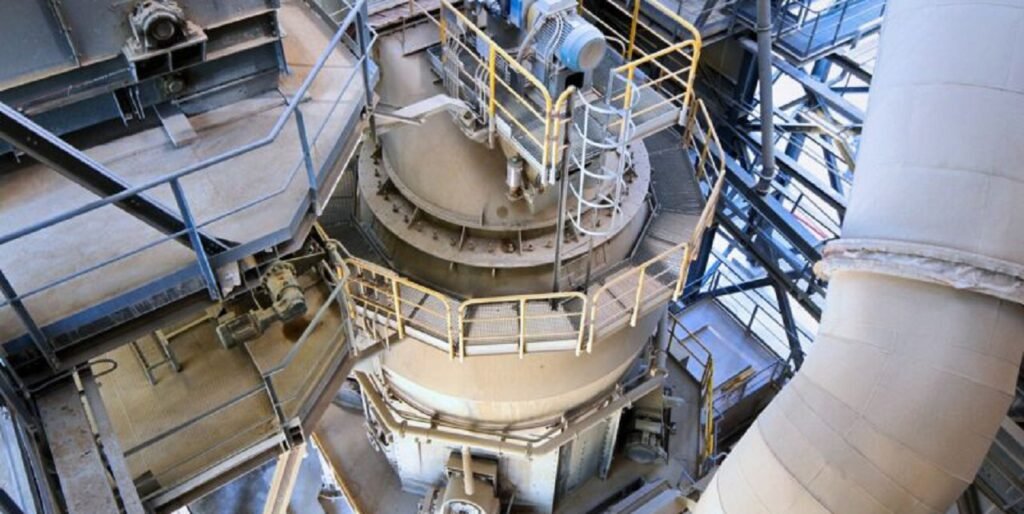
A new vertical mill classification grinding device is added. The powder return of the powder selection machine is changed from the original center discharge to three streams of diversion to the bottom of the grinding wheel for direct re-grinding, which can improve the stability and grinding efficiency of the vertical mill.
Edge feeding to center feeding:
Change the edge feeding to the center feeding. The ATOX vertical mill feeds materials into the mill from one side of the shell. The materials fall directly on the grinding disc lining and enter the three grinding spokes in turn, making the material layer difficult to stabilize. We extended the material discharge chute and welded a distribution cone bucket under the center frame of the grinding spoke. After the materials enter the distribution cone bucket, they evenly enter each grinding spoke from under the distribution cone, which can stabilize the material layer and improve the grinding conditions.
Increase mill outlet air duct:
Modification of non-standard pipelines at the mill outlet. The diameter of the mill outlet air duct was increased from 3.6m to 4.2m to reduce system resistance.
FL-smidth Atox 50 vrm mill secondary system upgrade
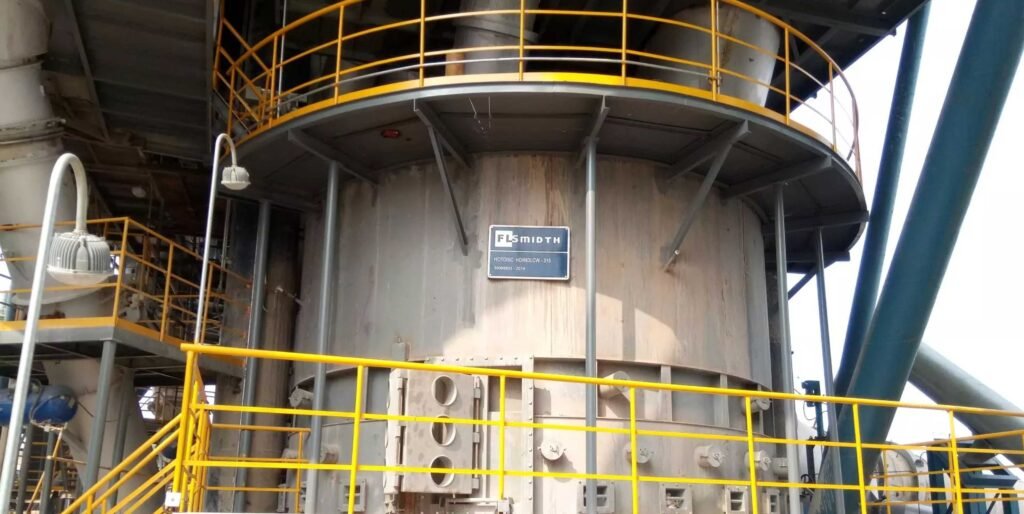
Why a secondary grinding system upgrade?
After the first upgrade, we notice the kiln system still cannot meet the needs of increased production, and other production increase plans must be considered. Through the summary of the commissioning and operation in the past six months, we believe that the NU powder selector, middle shell air supply, low-resistance wedge-shaped air ring, center discharge modification, and thickening of the mill air duct have all played their respective roles, improving the powder selection efficiency, reducing the mill pressure difference, and stabilizing the material layer. However, the newly added graded powder mill discharge pipe has no effect. We have conducted many tests, and the return pipe to the center of the grinding disc or to the bottom of the grinding spoke has little effect on the output.
So, What to do next?
The effect of graded grinding on the mill on ZJTL/TRM Series VRM is very obvious, but the effect is not obvious when using ATOX vertical mill. We believe that the biggest feature of ATOX vertical mill is flat disc and column spokes, large contact area between grinding roller and grinding disc, wide grinding area and small grinding pressure. Directly guiding the return material of powder selector to the bottom of grinding spokes cannot improve the grinding efficiency. We consider that the grinding spoke pressure has increased to 13.2MPa, and the vibration will increase when pressurized. In addition, the pressure is close to the upper limit allowed by the system, and the grinding efficiency can no longer be improved by increasing the grinding pressure. Therefore, we think that by reducing the width of the contact surface between the grinding disc and the grinding spokes and increasing the pressure of the local material layer outside the grinding disc, the grinding capacity of the mill can be improved.
Grinding zone(width of contact surface bewteen grinding table and roller)1000mm finished product distribution:
Particle Size (mm) | Particle Count(Qty) |
0.0760 | 269244.5 |
4.4803 | 107697.8 |
8.8846 | 26924.5 |
13.2890 | 0 |
17.6933 | 0 |
22.0976 | 323093.4 |
26.5019 | 0 |
30.9062 | 0 |
35.3106 | 0 |
39.7149 | 26924.5 |
44.1192 | 53848.9 |
48 | 0 |
Grinding zone 595mm finished product distribution:
Particle Size (mm) | Particle Count |
0.0762 | 367719.8 |
4.4805 | 122573.3 |
8.8848 | 40857.8 |
13.2891 | 0 (approximate, as no bar or negligible count shown) |
17.6934 | 0 (approximate, as no bar or negligible count shown) |
22.0978 | 449435.3 |
26.5021 | 0 (approximate, as no bar or negligible count shown) |
30.9064 | 0 (approximate, as no bar or negligible count shown) |
35.3107 | 40857.8 (approximate, based on bar height) |
39.7150 | 81715.5 (approximate, based on bar height) |
44.1193 | 81715.5 (approximate, based on bar height) |
48.5236 | 0 (approximate, as no bar or negligible count shown) |
After simulation calculations by TONGLI technicians using simulation technology, it was confirmed that under the condition of unchanged grinding pressure, the finished product output of the original grinding area width 1000nun grinding disc (≤80μm) was 251420 pieces/1e-7s; the finished product output of the grinding disc (≤80μm) was 377412 pieces/1e-7s when the grinding disc was changed to a flat outer and conical inner form with a flat surface width of 595mm, which was 50% higher than the same period last year.
Conclusion:
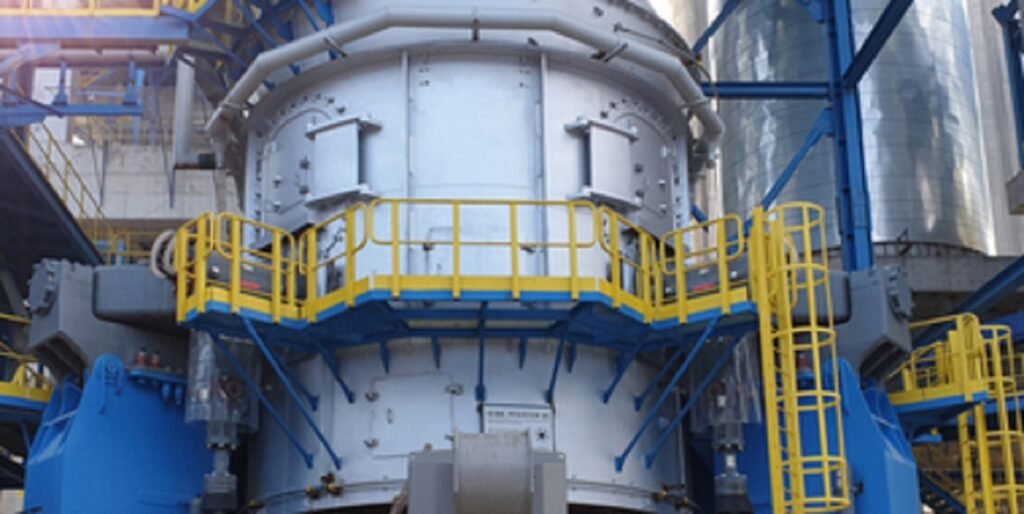
After the secondary upgrade finalized, we welded and repaired the 600mm wide part of the grinding disc liner on the outside to make it smooth, and then used an arc air planer to plane the 400mm inside of the grinding disc near the center of the mill into a conical surface, and then transformed the grinding disc. After the grinding disc was transformed, the stability of the mill was further improved by adjusting the height of the retaining ring, the opening of the middle shell air supply valve, the area of the air ring, etc. The output of the vrm mill was stabilized at about 470t/h per hour, which met the needs of the kiln system. So overall from the upgrade of the fl-smith atox vertical roller mill we concluded the following 4 points:
- The improvement of the powder selection efficiency of the powder selector can improve the condition of the mill and thus increase the hourly output of the vertical mill system, but it does not play a decisive role in most cases. It is more of a prerequisite for increasing production.
- The middle shell air supply and low-resistance wedge-shaped plate air guide ring have a great influence on the grinding indicators such as material layer thickness, pressure difference in the mill, powder selector speed, and mill vibration value. It is necessary to gradually explore and adjust them in coordination to play the role of reducing resistance and improving efficiency.
- The increase of the central distribution cone and the transformation of the grinding disc have made the material layer more stable, creating conditions for increasing the grinding pressure and reducing the height of the retaining ring.
- The transformation of the grinding area of the grinding disc and the guidance of the powder return of the powder selector to the high-pressure grinding area for direct grinding have fundamentally changed the grinding mechanism of the ATOX50 flat disc vertical mill, improved the grinding capacity of the mill, and became the key to the success of this transformation.
So if you are also a cement vertical roller mill owner who wants to upgrade your current vrm or buy a new one, you can contact us anytime. We have many years of experience in terms of manufacturing as well as maintenance of vertical roller mill, successfully upgraded more than 1000+ sets of vertical grinding machine.