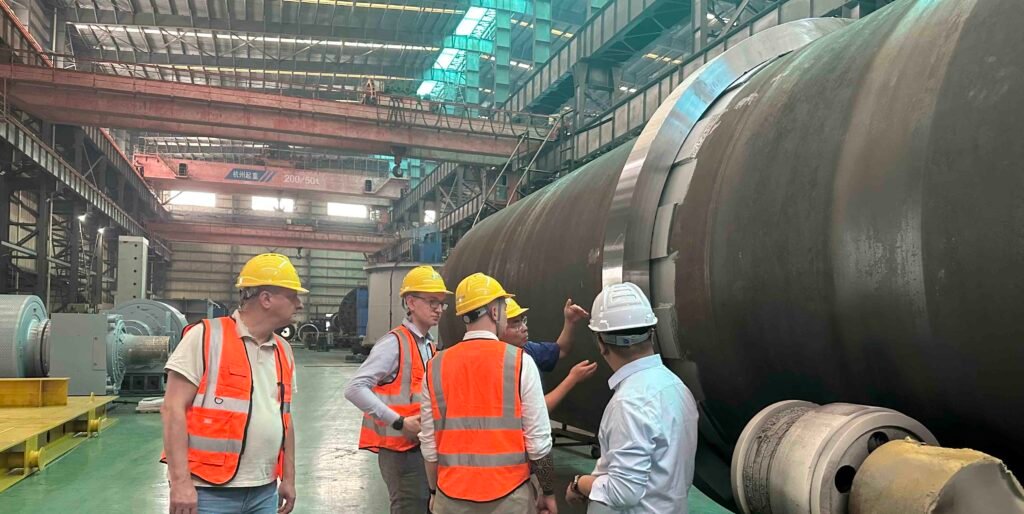
On June 5th, we welcomed three guests from Europe who visited Tongli Heavy Machinery to inspect our waste incineration rotary kiln for hazardous and medical waste. This group has already worked with Tongli on over five projects. Tongli has provided top-quality rotary kilns and secondary combustion chambers to this customer, which serve as the core components of their waste incineration plants. The waste incineration rotary kiln is a device that uses a tilted and rotating high-temperature resistant kiln body to incinerate and treat various types of waste such as domestic waste, industrial hazardous waste, and medical waste at high temperatures 800-1200℃. When working, it achieves preheating, combustion and oxidation through the movement of materials in the kiln, which can significantly reduce waste and destroy harmful substances. At the same time, heat energy can be recovered.
Why do customers visit Tongli for hazardous waste incineration rotary kiln?
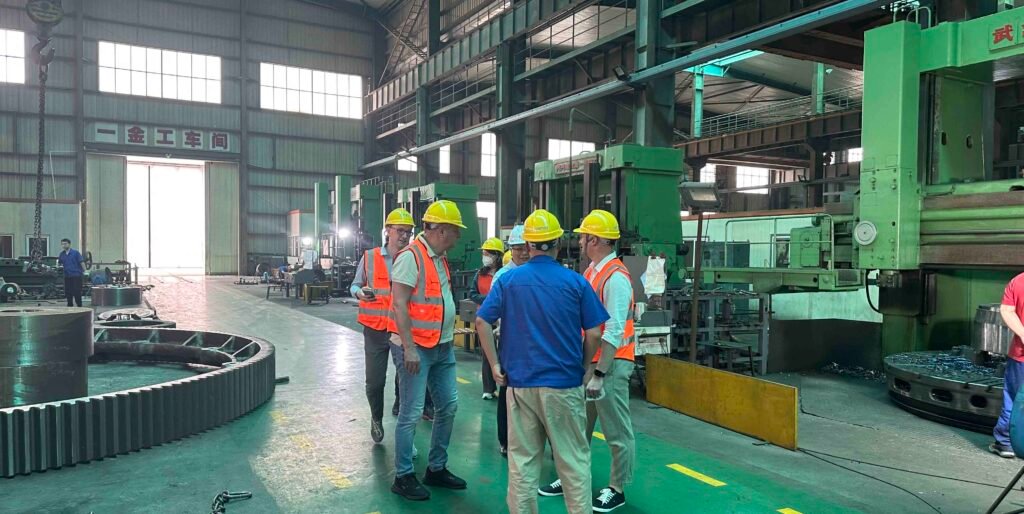
The reason why customers choose to visit Tongli to inspect hazardous waste incineration rotary kilns is, first of all, that they recognize its rich project experience. Tongli has accumulated a large number of actual cases in the field of hazardous waste treatment. These verified project operation data and results can enable customers to more clearly evaluate the adaptability and stability of the equipment under different working conditions.
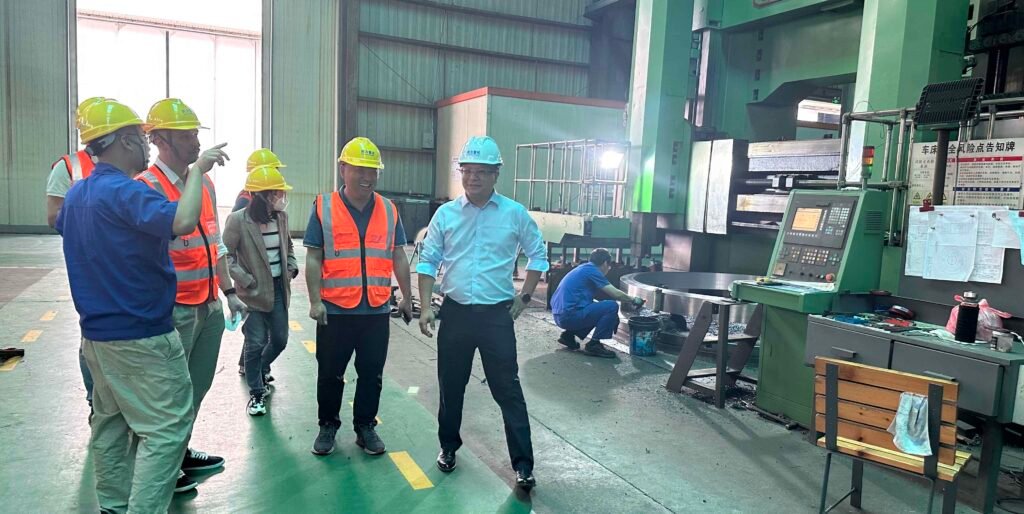
Secondly, advanced processing equipment is also a focus of customer attention. The core components of the rotary kiln, such as the shell and wheel tyre, have a direct impact on the service life and operating stability of the equipment due to their processing accuracy and material properties.
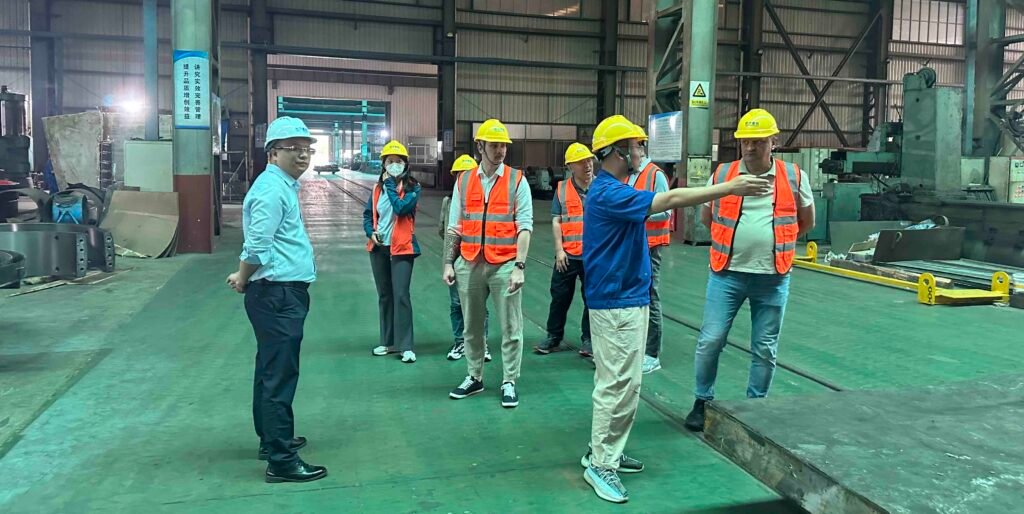
The advanced processing equipment equipped by Tongli can ensure the manufacturing accuracy and quality consistency of key components, and reduce the risk of later failures caused by equipment defects. Customers can further confirm the quality assurance capabilities of the equipment through on-site inspections of the processing links, providing a basis for cooperation decisions.
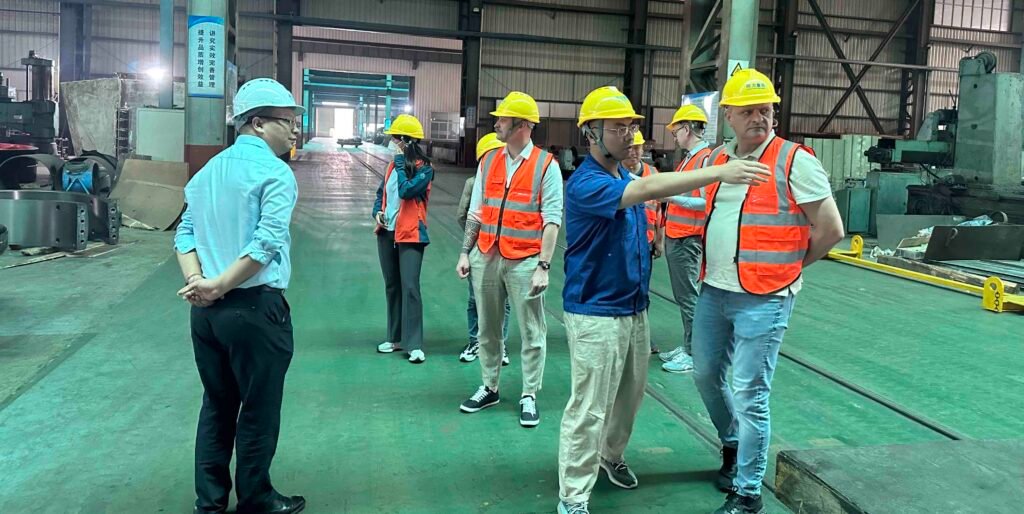
Riding ring of the incineration rotary kiln:
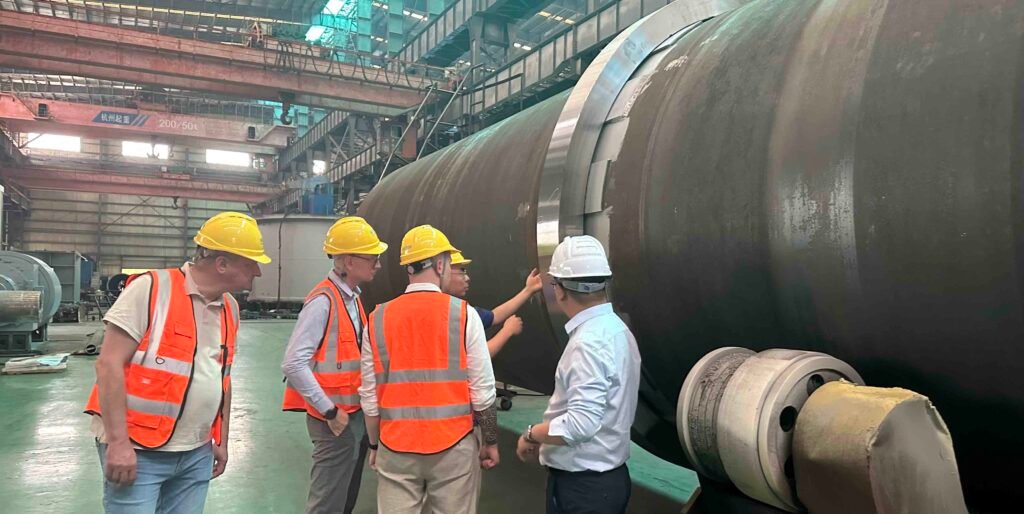
- The shell is rolled with high-strength steel plates, which has sufficient structural strength and toughness. It can withstand the impact and friction of different forms (solid, block, viscous) and corrosive wastes, and cooperate with the wheel band to provide stable support for the kiln body to ensure that the kiln body does not deform during rotation.
- The shell needs to be wrapped with high-temperature refractory materials, and it itself needs to have certain heat resistance and oxidation resistance to cope with the high-temperature combustion environment of 800-1200℃ in the kiln; the wheel band is made of high-quality alloy cast steel (such as ZG35CrMo), which is not only resistant to high temperatures, but also can maintain sufficient strength and wear resistance at high temperatures.
- The shell is installed at an angle (1°-4°), and the rolling friction structure of the wheel band and the support wheel enables the kiln body to rotate at a stable speed of 0.5-5 rpm, ensuring that the waste moves evenly in the kiln, fully contacts high temperature and oxygen, and achieves complete combustion; the precise matching gap control between the wheel band and the shell reduces vibration and deviation during rotation.
- The shell thickness design (10-30 mm) and welding process ensure the durability of the structure. The wheel belt, as the core load-bearing component, can bear the total weight of the kiln body, materials and refractory materials for a long time by optimizing the material and size.
- The sealing performance design of the shell and the sealing of the feed port and ash outlet reduce the leakage of cold air, ensuring that the temperature in the kiln is stable at above 850℃ to meet the dioxin decomposition conditions; the stable transmission of the wheel belt and the supporting wheel avoids the fluctuation of the kiln body speed and ensures that the combustion time is controllable.
Incineration rotary kiln shell characteristic:
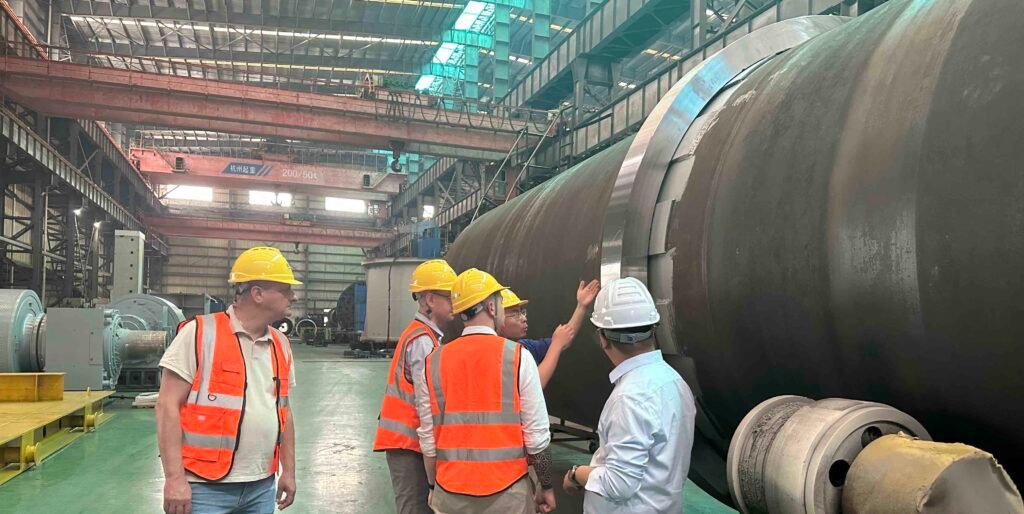
- The wheel belt is made of high-temperature resistant alloy cast steel ZG35CrMo and ZG42CrMo, which can maintain strength and toughness in the high temperature 300-500℃ conducted by the kiln body and the corrosive environment of flue gas, avoiding structural failure caused by high temperature softening or corrosion.
- Support heavy loads and ensure rotation stability: The wheel belt needs to bear the total weight of the kiln body including the shell, refractory materials, and materials. Its annular structure transfers the load evenly through contact with the supporting wheel, and accurately controls the thermal expansion and contraction compensation of the matching gap with the shell, reduces vibration and deviation during rotation, and ensures that the kiln body runs at a stable speed of 0.5-5 rpm, providing a mechanical basis for the dioxin burnout residence time ≥2 seconds.
- The surface of the wheel belt is precisely processed to form a low-friction rolling fit with the supporting wheel to reduce wear; the high wear resistance and fatigue resistance of its material can reduce the probability of frequent maintenance, meet the scenario where garbage incineration needs to run continuously for 24 hours, and reduce the impact of downtime on processing efficiency.
- In line with the requirements of sealing and temperature control: the tight assembly of the wheel rim and the shell, partially welded or elastically fixed, can reduce the radial deformation of the kiln body, indirectly ensure the sealing performance of the feed port and ash outlet, avoid the infiltration of cold air affecting the temperature stability in the kiln, ensure that the combustion temperature meets the standard, and create conditions for the thorough harmless treatment of pollutants (such as pathogens and toxic organic matter).
Customer visit rotary kiln shell manufacturer factory Process:
Plate rolling & bending
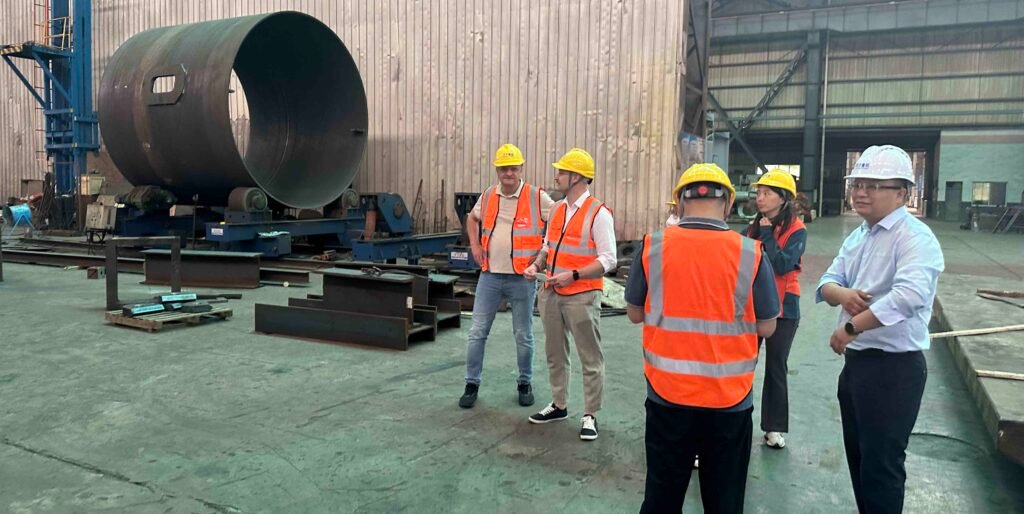
The plate rolling and bending of the hazardous waste incineration rotary kiln are key processes in manufacturing the kiln shell. The plate rolling is done by cold or hot bending the steel plate into a cylindrical shape through a large plate rolling machine to ensure the arc is accurate to ensure the roundness of the kiln body; the plate bending is done for special parts. These two processes directly affect the sealing, structural strength and assembly accuracy of the shell with components such as wheel tyres, and are the basis for ensuring the stable operation of the kiln body under high temperature and high pressure conditions.
Kiln shell machining
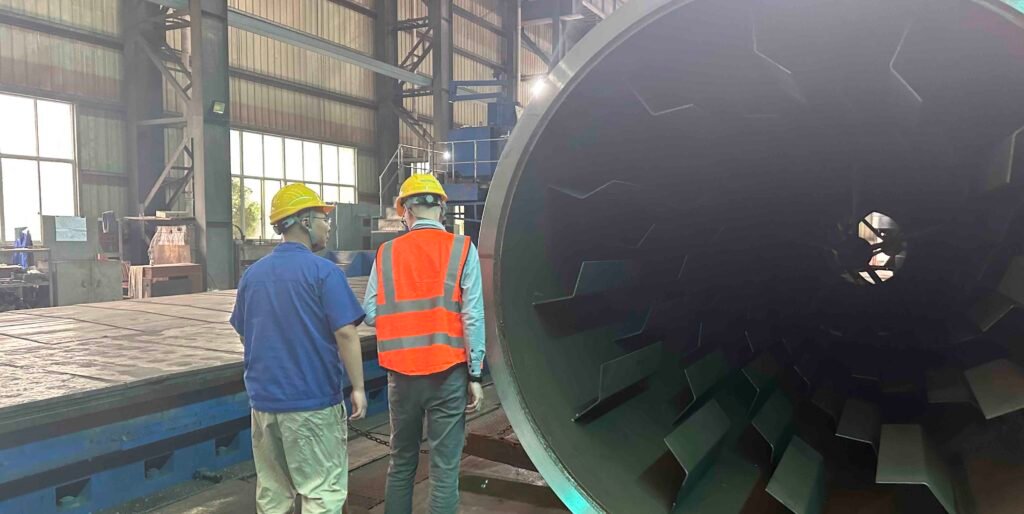
The kiln shell processing of hazardous waste incineration rotary kiln is a key link. It is made of high-strength alloy steel plate through CNC cutting, rolling and welding. The roundness and straightness of the cylinder must be guaranteed, and the welding points must be tested by non-destructive testing. The dimensional accuracy is strictly controlled during processing to ensure that it is compatible with the wheel belt and refractory materials, and can withstand high temperature, heavy load and thermal expansion and contraction, laying the foundation for the stable operation of the kiln body.
Incineration kiln in the warehouse
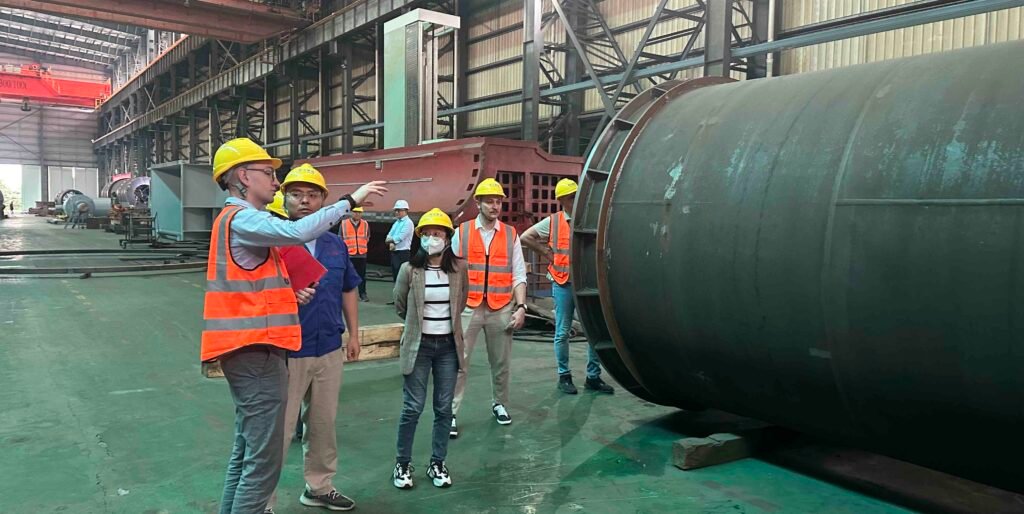
Hazardous waste incineration rotary kilns are usually waiting to be installed or overhauled in warehouses. The warehouse needs to be spacious and ventilated, equipped with lifting equipment for easy handling. The kiln body needs to be rust-proof and dust-proof during storage, and key components need to be protected separately. The warehouse also needs to be divided into zones to facilitate spare parts management and pre-processing to ensure that the equipment is in good condition when it leaves the warehouse.
Vertical boring and milling machine for rotary kiln
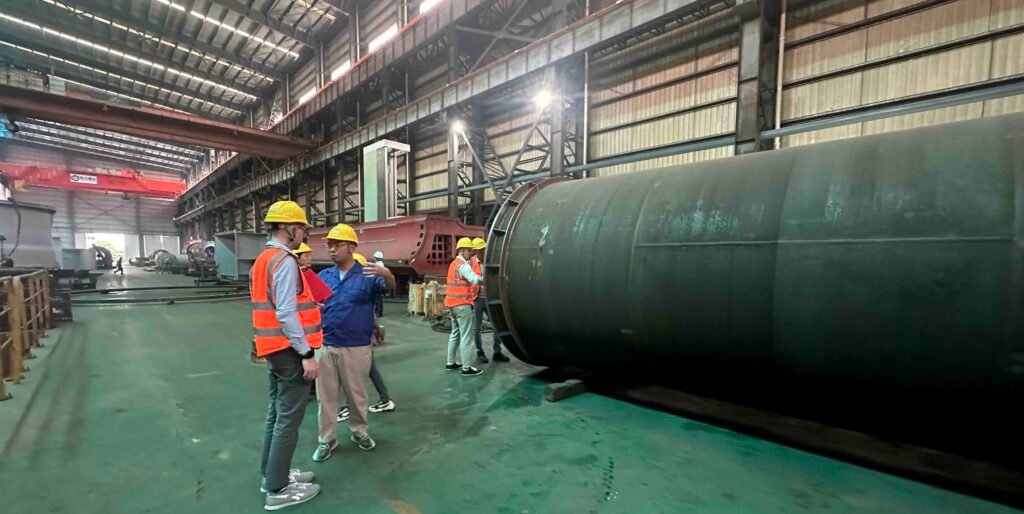
The rotary kiln vertical milling and boring machine is a key equipment for the processing of hazardous waste incineration rotary kilns. It has powerful digital control capabilities and can perform various processing such as milling, boring, and drilling on complex parts of rotary kilns. It has a profiling function and can accurately replicate and process special parts. The machine tool has three-axis control and linkage to ensure processing accuracy
Site visit Incineration kiln
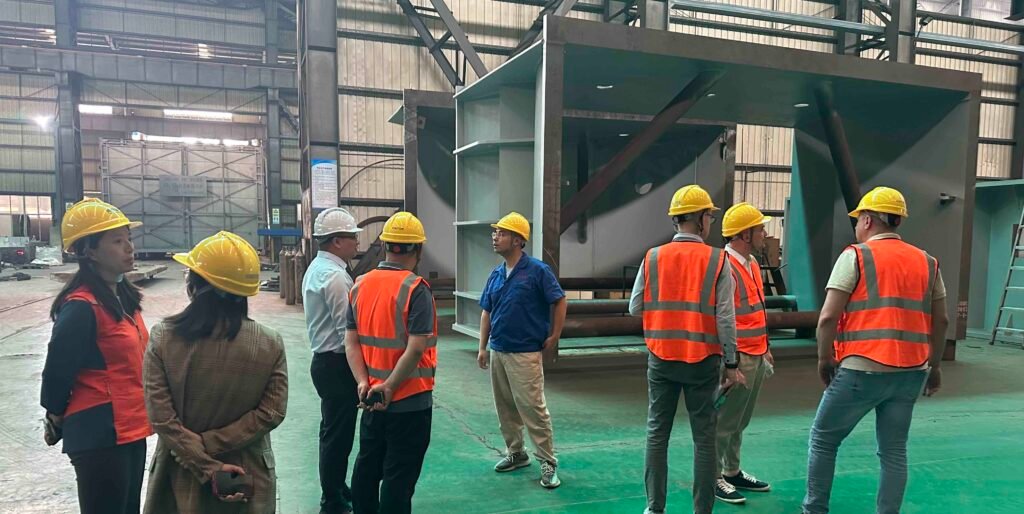
The on-site inspection of the hazardous waste incineration rotary kiln mainly checks the equipment operation status, including the kiln rotation stability, combustion temperature control and flue gas treatment effect. The core of the inspection is to verify its ability to handle complex hazardous waste.
Rotary kiln welding workshop
Tongli hazardous waste incineration rotary kiln welding workshop is a key link in the manufacturing of core components. The workshop is equipped with high-precision welding equipment and testing instruments, focusing on the welding of load-bearing structures such as kiln shells and wheel tyres.
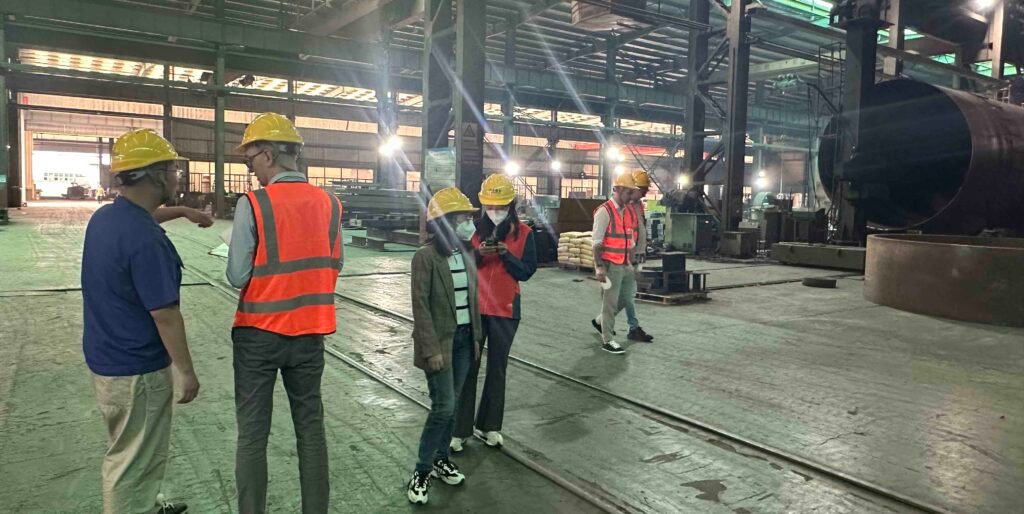
Rotary kiln welding workshop 2
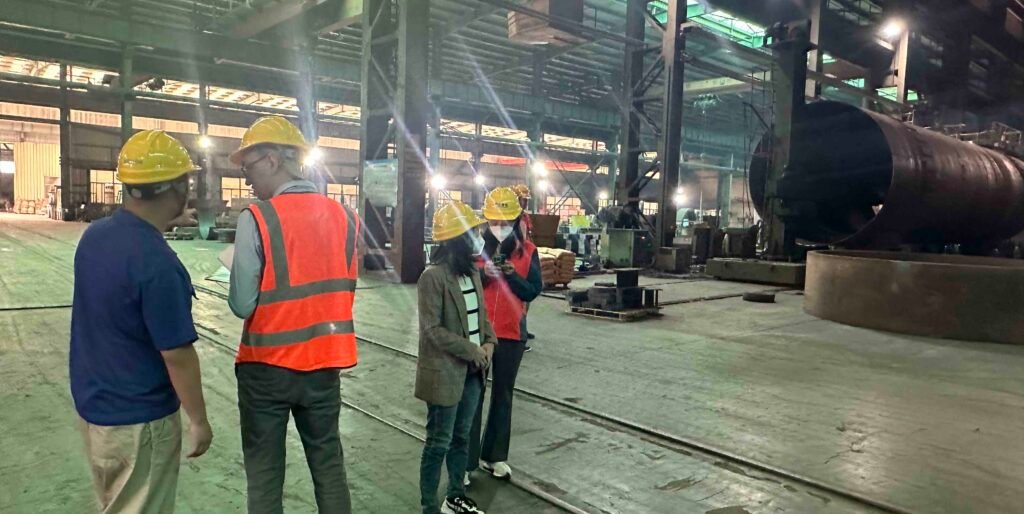
TONGLI welding workshop adopts mature welding technology, strictly controls the quality of welds, and ensures welding strength and sealing through non-destructive testing to meet the long-term stable operation requirements under high temperature and heavy load conditions.
Baseframe rotary kiln
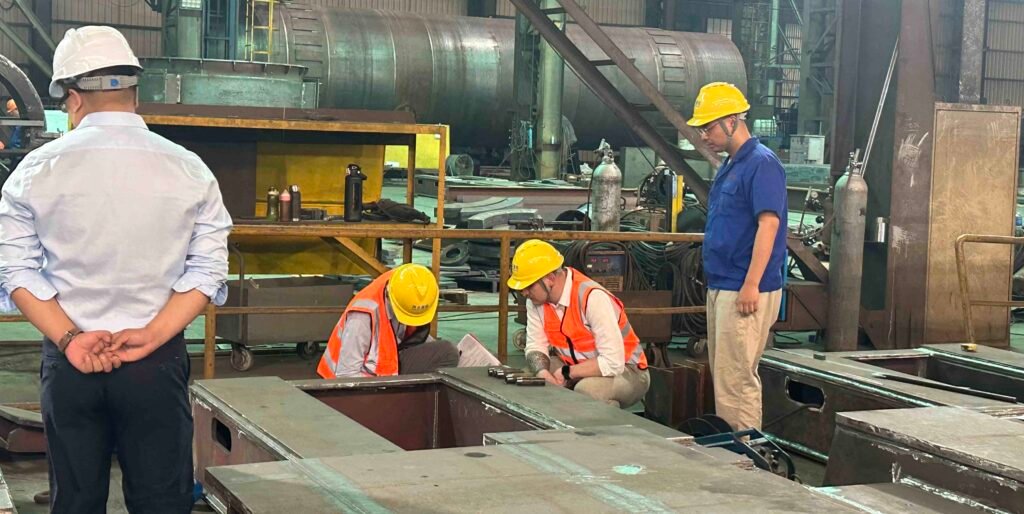
The base frame of the waste incineration rotary kiln is the key structure supporting the entire kiln body. It is usually welded from steel sections and needs to have high strength and stability. It needs to accurately position the supporting wheels, retaining wheels and other components to ensure the kiln body's tilt angle and rotation accuracy, while absorbing the vibration and load during equipment operation and adapting to thermal expansion and contraction under high temperature conditions.
baseframe grinding in progress
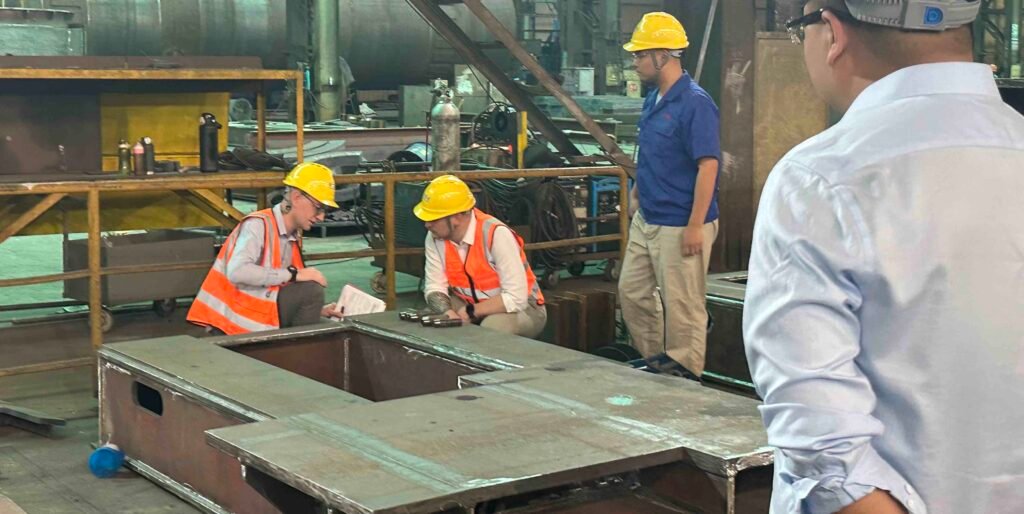
The base grinding of the hazardous waste incineration rotary kiln is in progress. This process is to precisely grind the metal surface of the equipment base to eliminate welding stress and surface unevenness, and ensure that the base fits tightly with the foundation installation surface. High-precision grinding can improve the stability of the equipment during operation and reduce the vibration of the kiln body caused by base errors.
Support roller incineration kiln transmission base
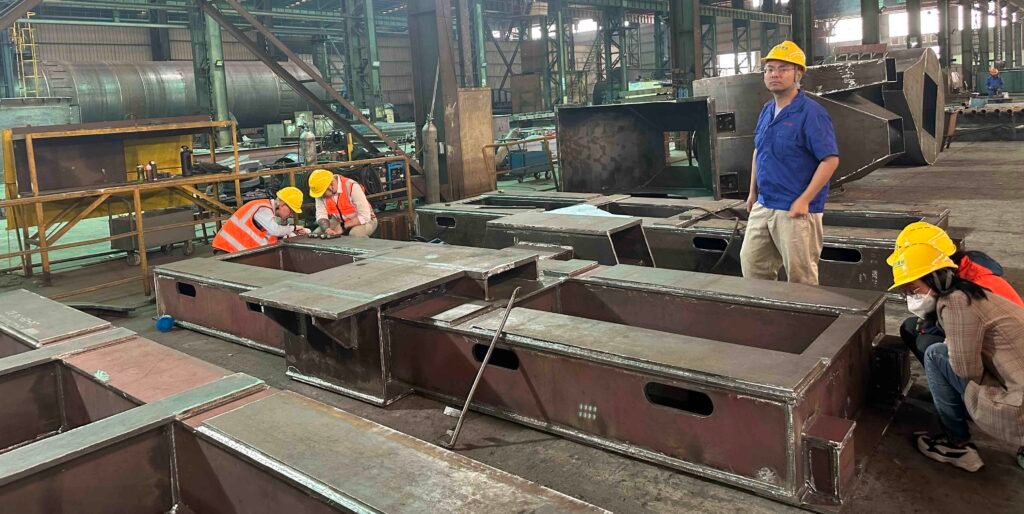
The supporting wheel and transmission base of the rotary kiln for incinerating hazardous waste are the key supporting and transmission components. The supporting wheel bears the weight of the kiln body and maintains the stable rotation of the kiln body through rolling contact with the wheel belt; the transmission base fixes the drive device and transmits power to accurately control the kiln speed. The two work together to ensure the stable operation of the kiln body.
Ultrasonic flaw testing incineration kiln
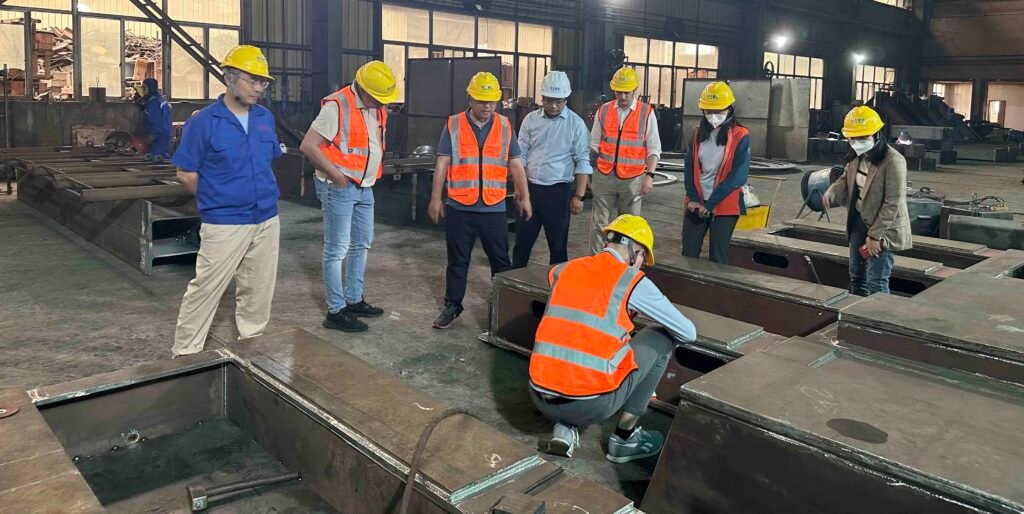
Ultrasonic flaw detection of hazardous waste incineration rotary kilns is a technology that uses ultrasonic detectors to detect key components such as kiln bodies and tires. It can penetrate metal materials, accurately identify internal cracks, interlayers and other defects, and promptly discover hidden dangers caused by welding or long-term high-temperature operation, ensuring the structural safety of equipment under high temperature and heavy load conditions.
Magnetic flaw testing waste incineration kiln
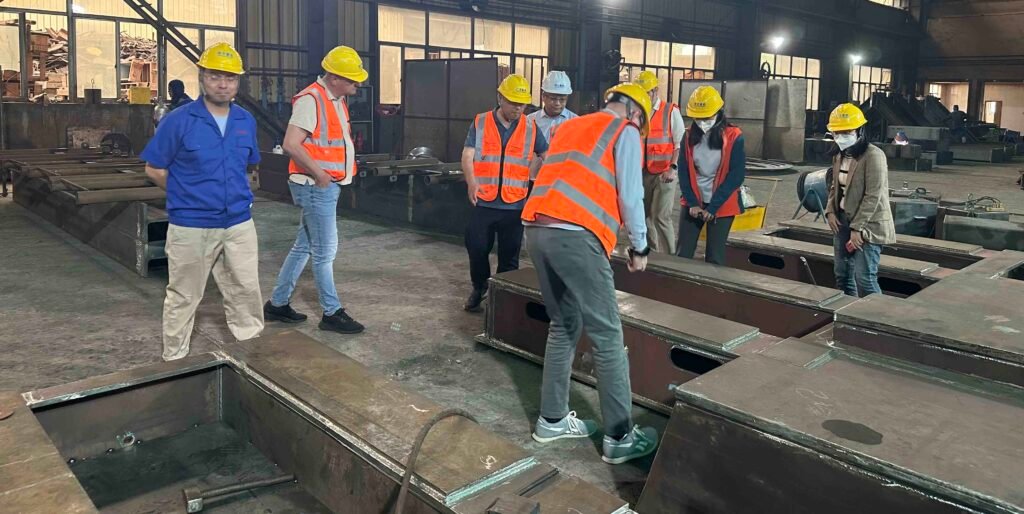
Magnetic particle inspection of hazardous waste incineration rotary kilns is a key means of detecting surface and near-surface defects of ferromagnetic parts such as shells and wheel tyres. By applying a magnetic field and spraying magnetic powder, the magnetic traces formed by the accumulation of magnetic powder at the defect can be used to accurately detect hidden dangers such as cracks and interlayers.
Penetration flaw testing waste incineration kiln
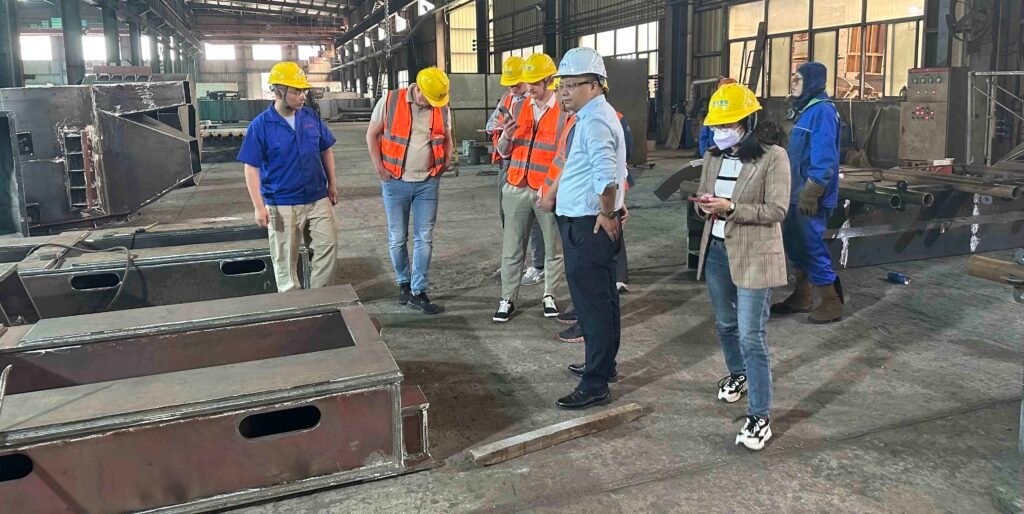
Penetrant testing is an important means of detecting waste incineration rotary kilns. By applying a penetrant to the surface of the kiln, the penetrant penetrates into the surface opening defects by capillary action. After cleaning and development, fine defects such as cracks and pores can be clearly displayed. This method is easy to operate and can effectively detect surface damage of key components such as shells and tyres.
Visual flaw detection rotary kiln
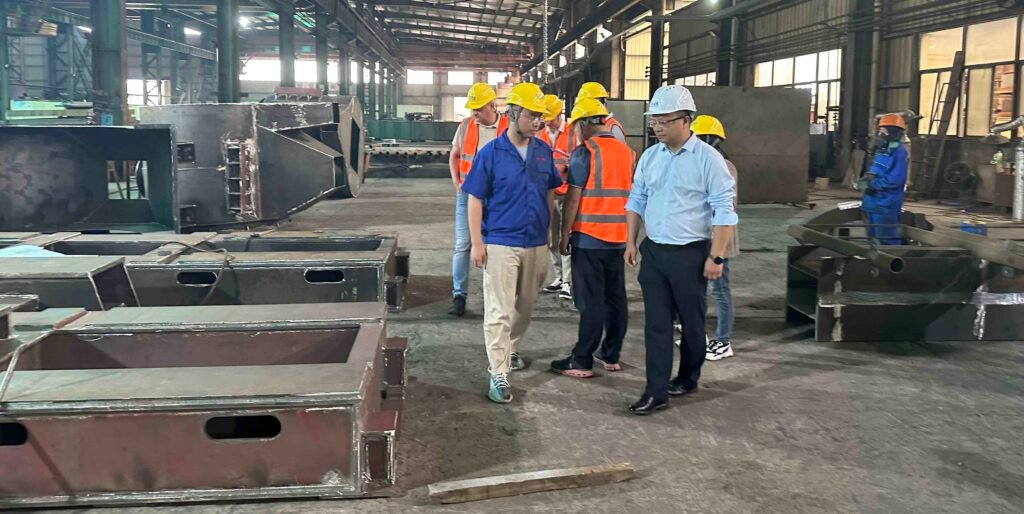
The appearance defect detection of hazardous waste incineration rotary kiln is an important part of ensuring the safety of the equipment. Check the kiln surface for cracks, deformation, corrosion, etc. by visual inspection or auxiliary tools, and check whether the wheel tyre and the supporting wheel are in uniform contact and whether the fasteners are loose.
Incineration rotary kiln bearing housing iron casting
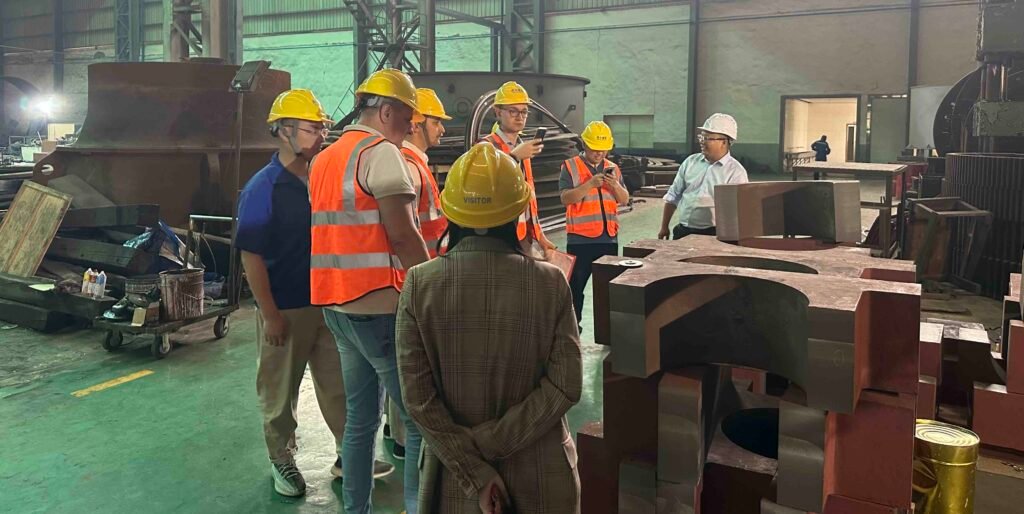
The bearing seat cast iron of the hazardous waste incineration rotary kiln is a key component that supports the rotation of the kiln body. It is made of high-strength cast iron, has excellent load-bearing capacity and wear resistance, and can withstand the combined loads of the kiln body's own weight, materials and high-temperature conduction. Its precision-machined mounting surface ensures precise matching with the bearing, reduces operating vibration, and ensures stable rotation of the kiln body.
Incineration rotary kiln support roller, heavy-duty design
The supporting wheel of the hazardous waste incineration rotary kiln is the core component supporting the kiln body. It cooperates with the wheel belt to bear the weight of the entire kiln body, including the shell, refractory materials and internal materials. Its surface is precisely processed to ensure uniform contact with the wheel belt, reduce local wear, and provide a basis for the stable rotation of the kiln body.
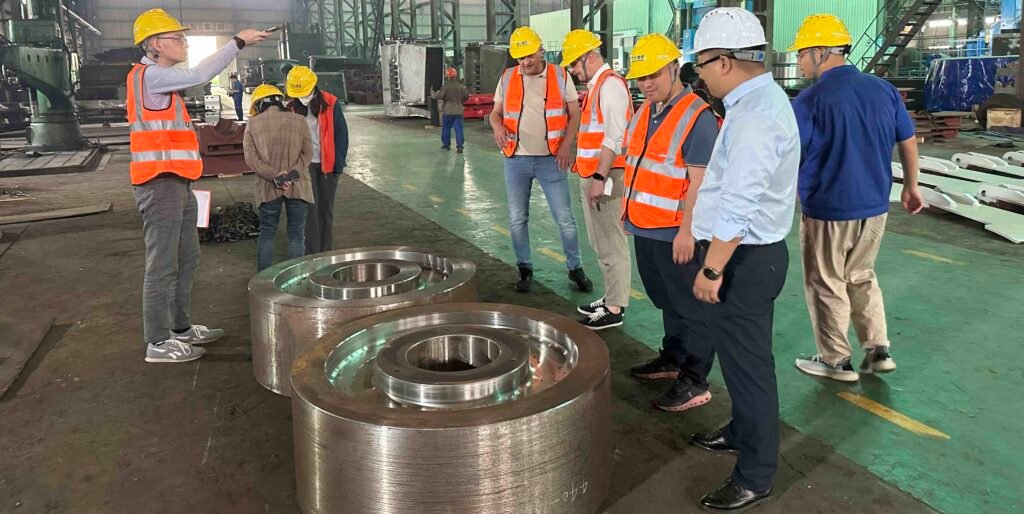
Waste incinerator rotary kiln support roller closeup
The supporting wheel is made of high-strength alloy cast steel and has excellent high temperature resistance and fatigue resistance. Under the continuous high temperature and alternating load transmitted by the kiln body, it can maintain structural stability, avoid deformation or breakage, and adapt to the harsh working conditions during hazardous waste incineration.
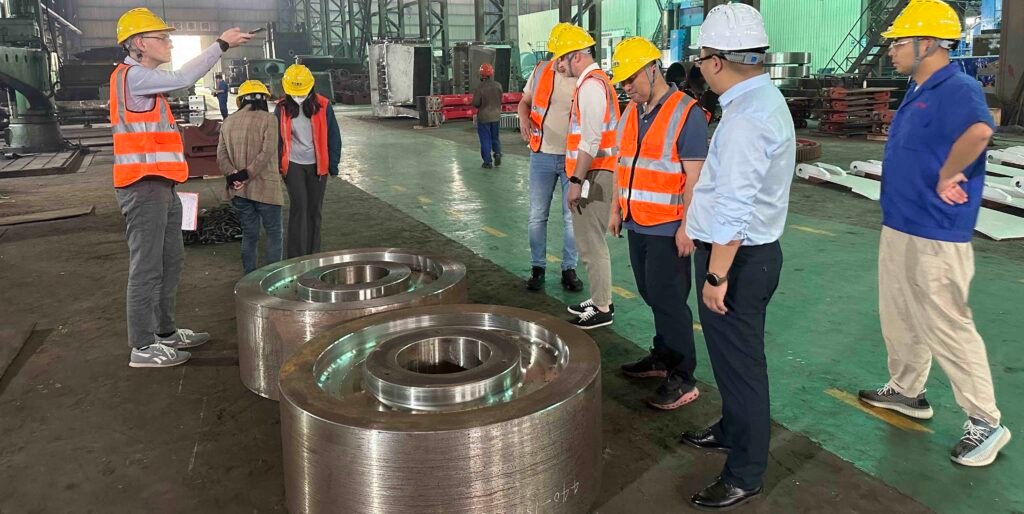
Support roller for hazardous waste rotary kiln installation
The structural design of the supporting wheel needs to match the inclination angle and rotation speed of the kiln body. Through rolling friction with the wheel belt, the kiln body is guided to rotate at the set speed to ensure that the materials move evenly in the kiln and burn fully. Reasonable contact stress distribution can extend the service life of the supporting wheel and wheel belt.
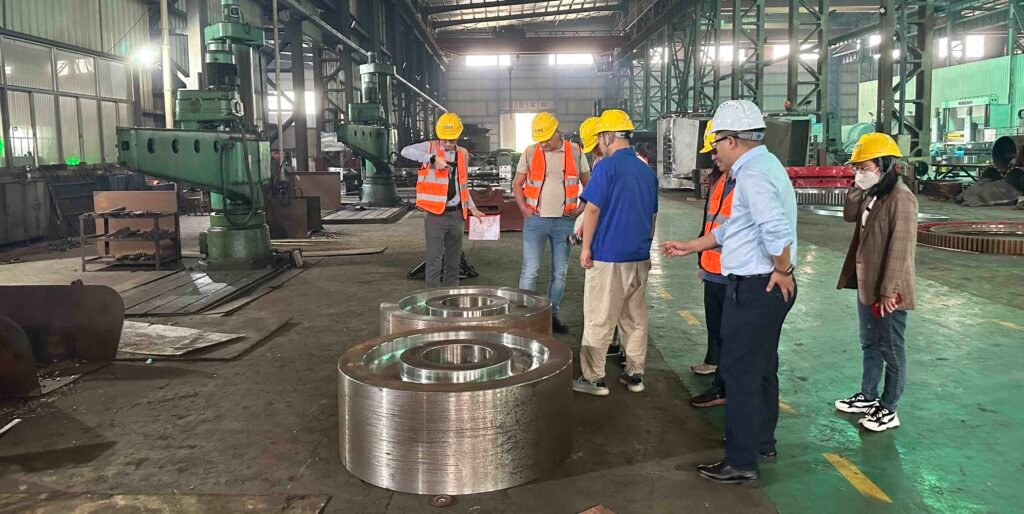
Rotary kiln support roller for medical waste incineration
The supporting wheel group is usually equipped with a self-aligning device and a lubrication system. The self-aligning device can compensate for installation errors and ensure balanced force; the lubrication system reduces friction loss, maintains efficient operation of the supporting wheel, reduces the risk of failure caused by friction overheating, and ensures continuous operation of the equipment.
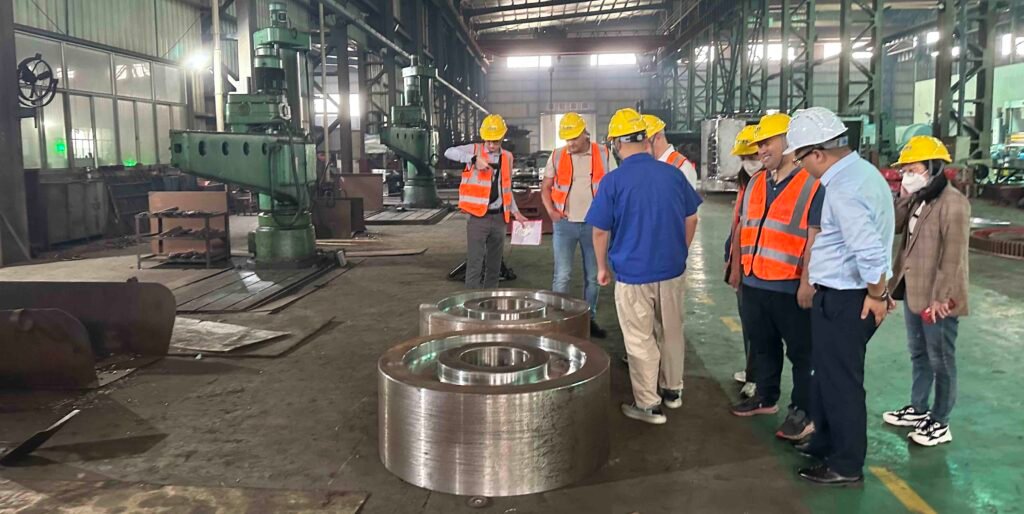
Incineration rotary kiln support roller forging
The installation accuracy of the support roller directly affects the operating stability of the rotary kiln. The horizontality and spacing must be strictly controlled to avoid the kiln body from deviating or vibrating too much. Regular inspection of the support roller wear and timely adjustment are important links to ensure the safe and efficient incineration process of hazardous waste.
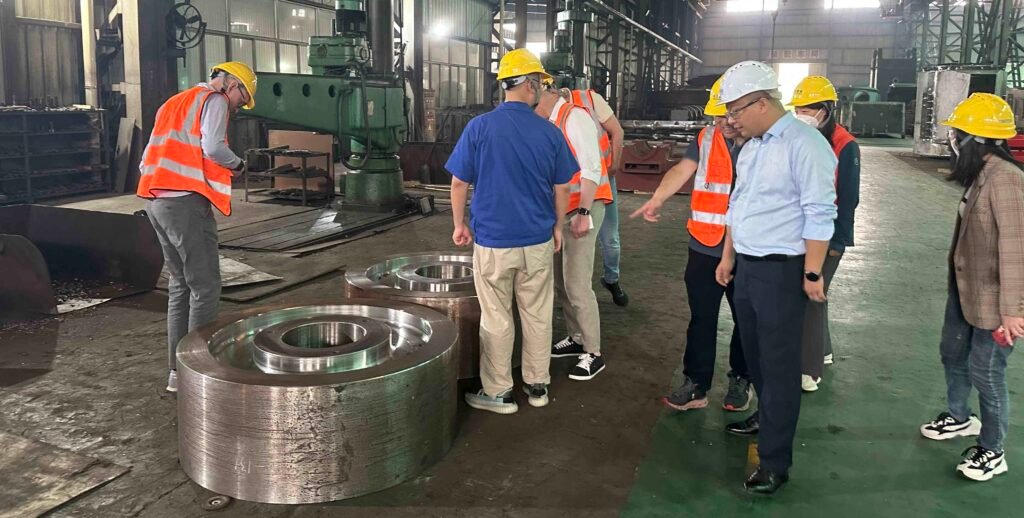
Rotary kiln gearbox inpection
The gearbox is the transmission hub connecting the motor and the kiln body, and transmits the motor power to the kiln body by reducing speed and increasing torque. It adopts hard tooth surface gear design, has strong load-bearing capacity and high transmission efficiency, and is equipped with forced lubrication and cooling system, which can reduce wear under heavy load and high temperature conditions.
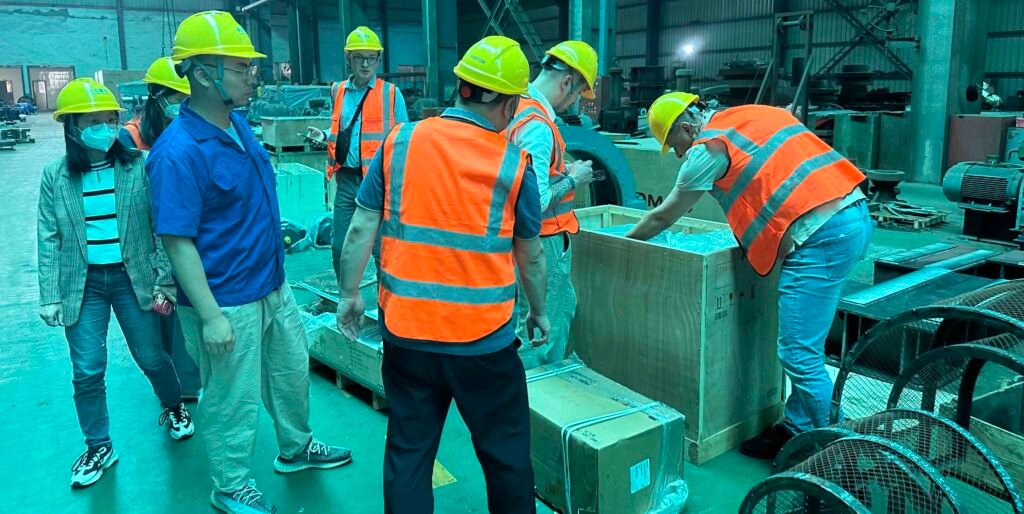
waste incineration kiln motor inpection
The motor of the hazardous waste incineration rotary kiln is the driving core. It mostly adopts variable frequency speed regulation asynchronous motor, which can adjust the kiln body speed (0.5-5 rpm) according to the incineration conditions. It has high torque output capacity, can overcome the heavy load starting resistance of the kiln, and has excellent high temperature resistance and vibration resistance.
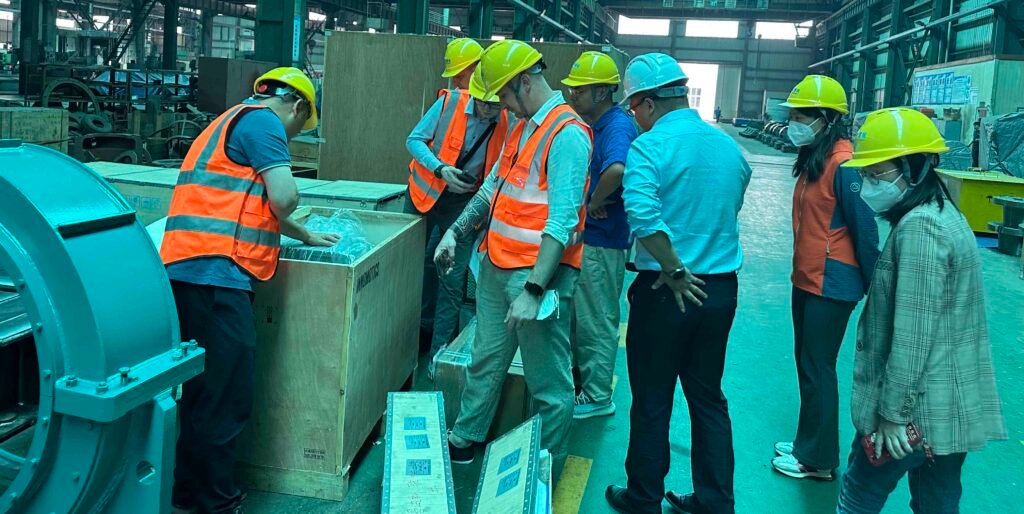
waste incineration kiln coupling inpection
The coupling is used to connect the motor and the gearbox, the gearbox and the kiln body, which can compensate for the equipment installation error and axial and radial displacement during operation, and buffer the impact load during transmission. It adopts elastic or rigid structure to adapt to the low speed and heavy load characteristics of the rotary kiln.
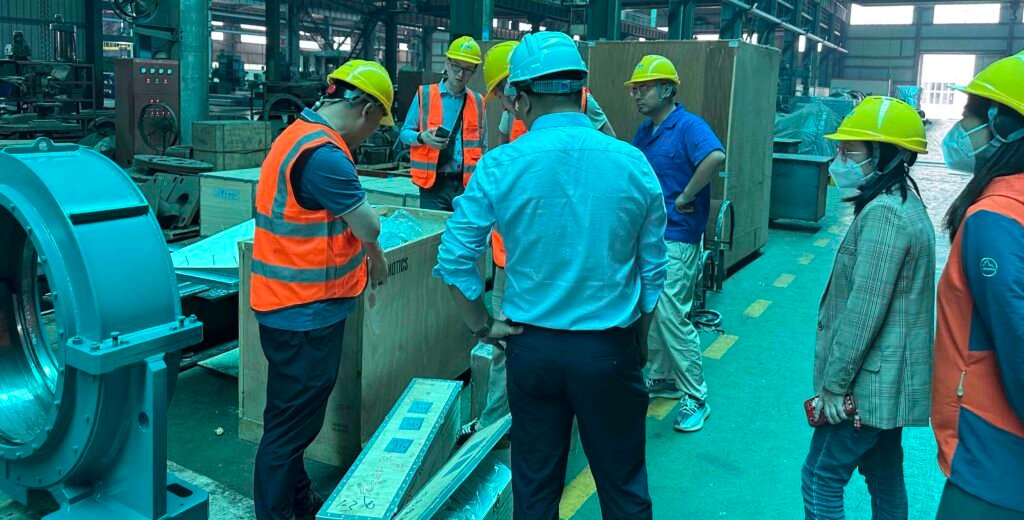
waste harzardous medical rotary kiln support roller device assembly
The support device consists of a supporting wheel group, a stopper wheel, etc., and is a structure that bears the overall weight of the rotary kiln. The supporting wheel supports the kiln body and guides the rotation by contacting the wheel belt, and the stopper wheel limits the axial movement of the kiln body. The base is made of high-strength castings, and the horizontal and vertical degrees are strictly calibrated during installation, so it can remain stable under high temperature and heavy load.
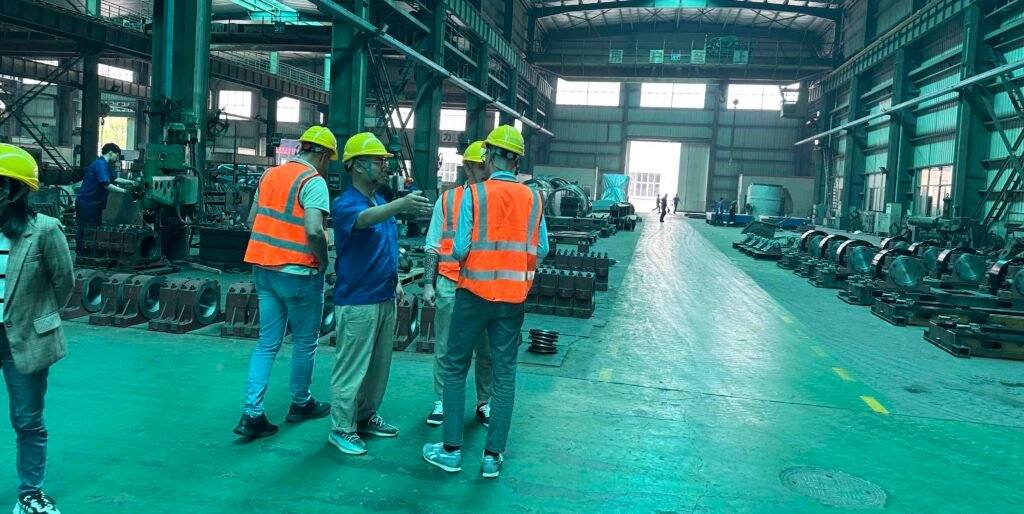
Tongli incineration rotary kiln spare parts warehouse
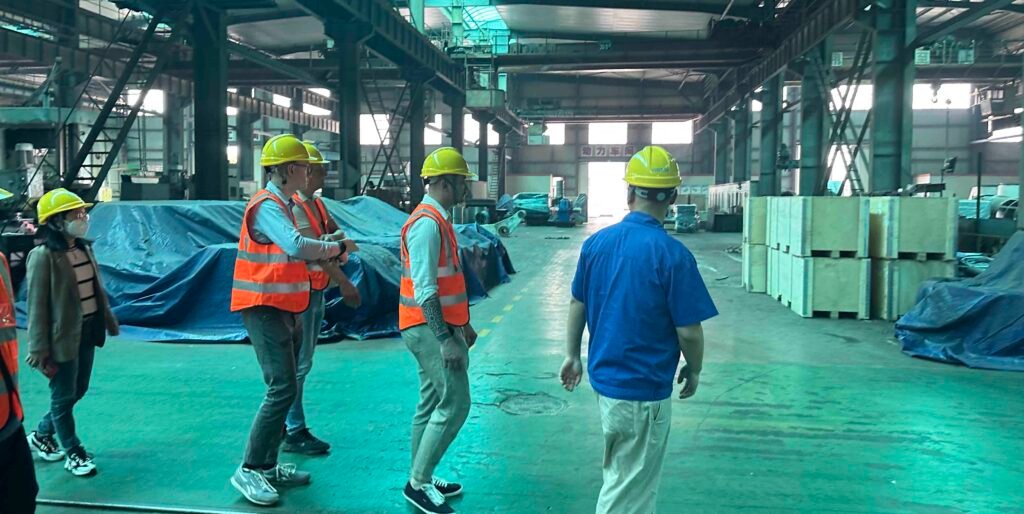
Tongli incineration rotary kiln spare parts warehouse 2
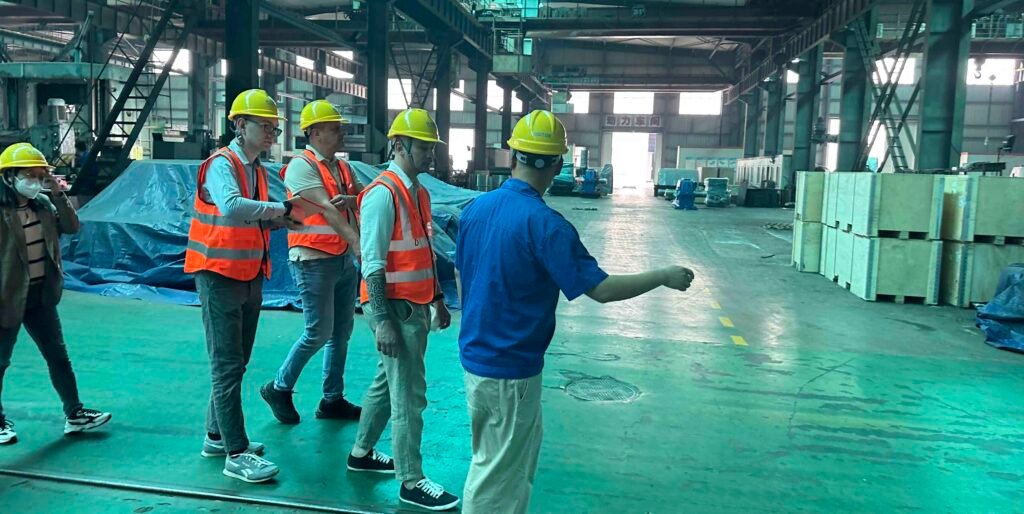
incineration kiln support roller forged shaft heat treating
Through normalizing, quenching and tempering processes, the internal grains of forged steel can be refined, forging stress can be eliminated, and the comprehensive mechanical properties of the shaft can be improved. After high-temperature tempering, the support wheel shaft can obtain an appropriate balance of hardness and toughness, ensuring that it is not easy to crack or deform when it is subjected to heavy kiln loads, high temperature conduction and alternating stress for a long time.
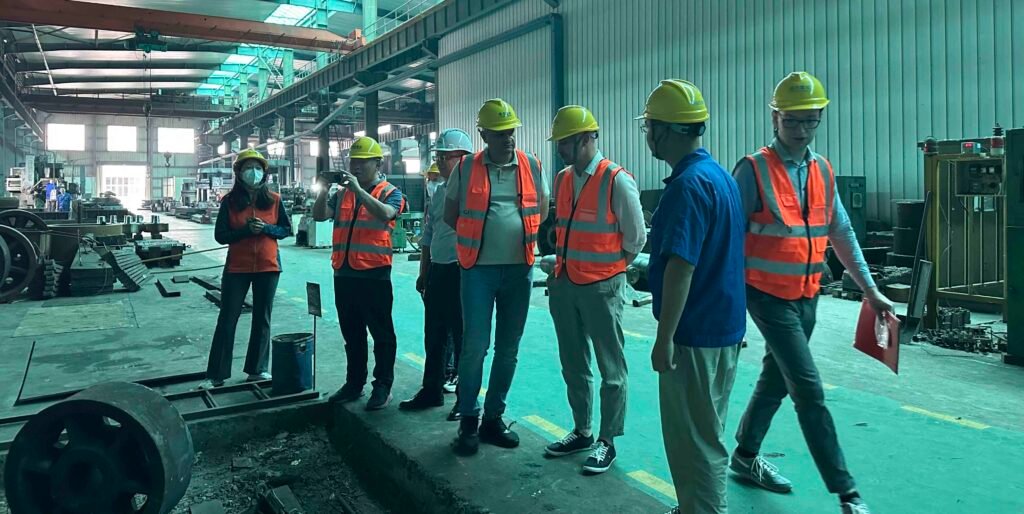
hazardous-waste-rotary-kiln-girth-gear-installation
The large girth gear is the power transmission hub of the hazardous waste incineration rotary kiln, meshing with the small gear to drive the kiln body to rotate. It converts the motor power into the circular motion of the kiln body through stable tooth surface contact, ensuring that the kiln body runs at the set speed (0.5-5 rpm).
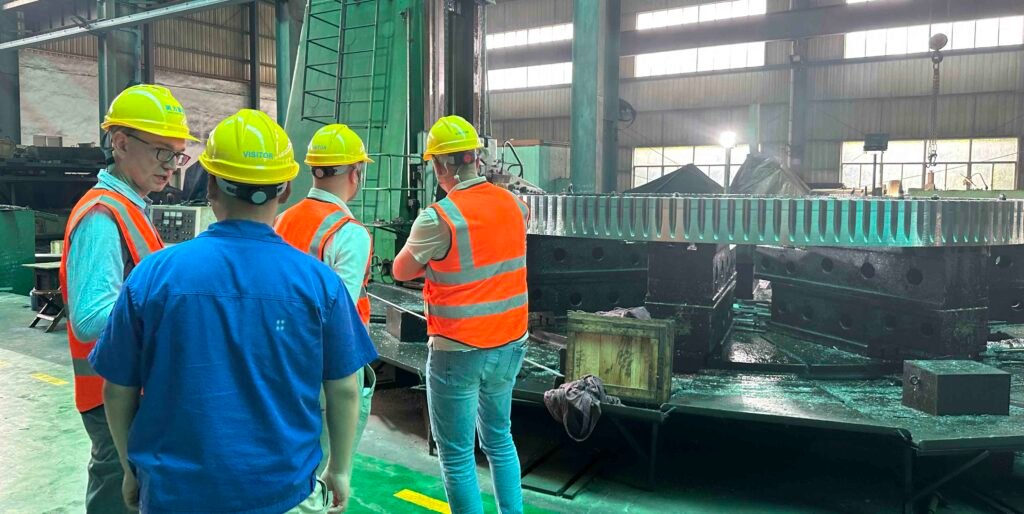
incineration-rotary-kiln-girth-gear-for-hazardous-waste
Because it is in a high temperature environment for a long time, the large gear is mostly cast with alloy cast steel (such as ZG35CrMo), and the hardness and toughness are improved after quenching and tempering. This material can resist the heat conducted by the kiln body and the high temperature of tooth surface friction, avoiding deformation or tooth surface wear.
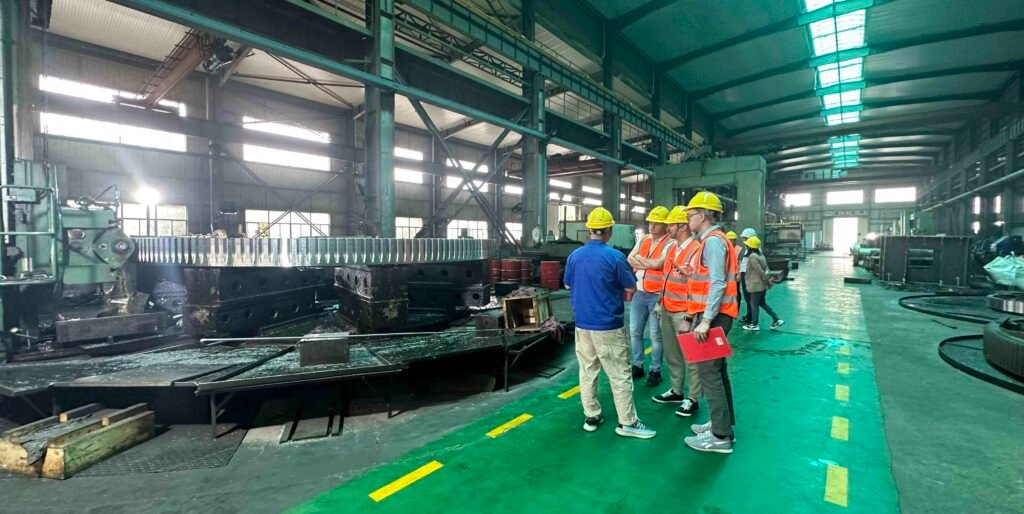
heavy-duty-girth-gear-hazardous-waste-incinerator
The large gear is mostly a split structure, which is easy to install and maintain. The gear ring and the wheel hub are connected by bolts, and the gap for thermal expansion and contraction is reserved. The tooth shape is optimized to ensure smooth meshing with the pinion and reduce impact loads.
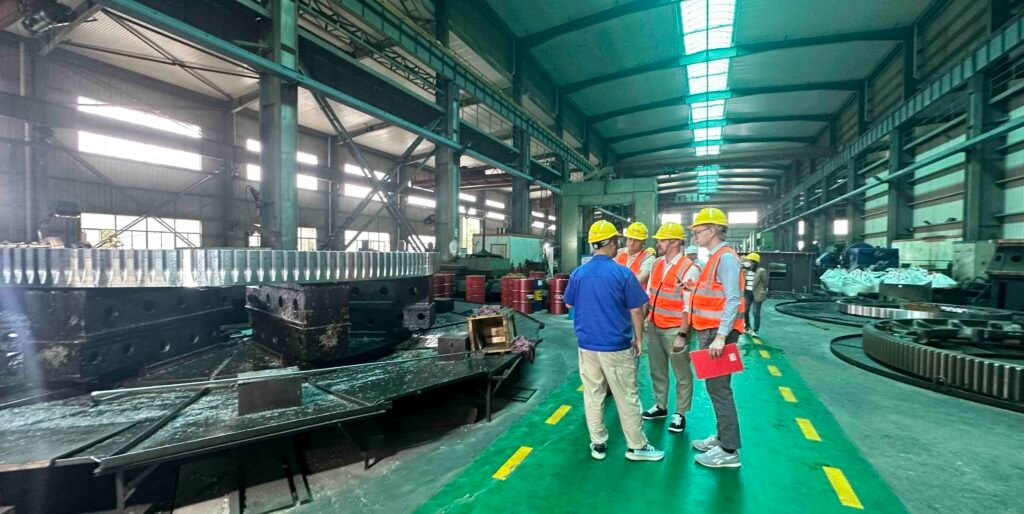
rotary-kiln-girth-gear-closeup-hazardous-waste-plant
The tooth surface needs to be precisely processed to ensure the accuracy of the pitch and tooth shape, and to ensure uniform meshing gap with the pinion. The concentricity must be strictly calibrated during installation to avoid local wear caused by eccentricity.
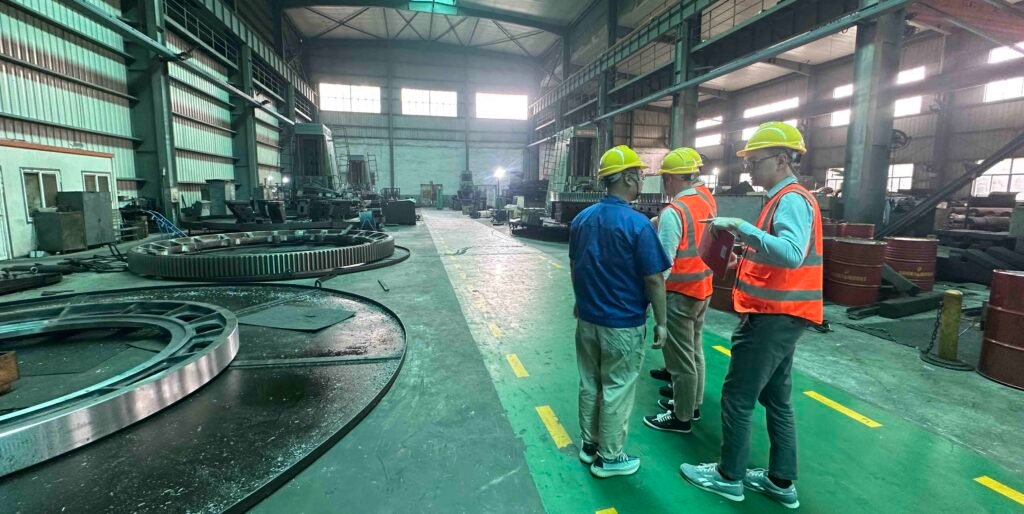
precision-machined-girth-gear-for-waste-incineration-kiln.
It is necessary to regularly check the tooth surface wear, meshing clearance and bolt tightness, and clean the debris between the teeth in time. Use high-temperature grease for lubrication to reduce friction loss on the tooth surface. If cracks or excessive wear on the tooth surface are found, they must be repaired in time.
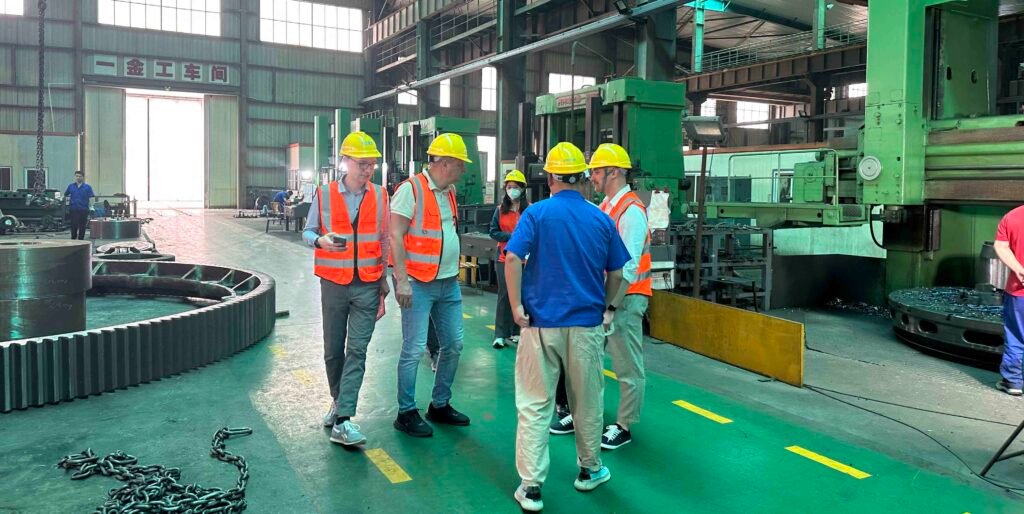
Conclusion:
Overall, the customer was very satisfied with the machining capability, quality, and process control of the medical waste incineration rotary kiln. As a result, we successfully passed the pre-inspection. One month later, they will return with the investor to conduct the final acceptance test of the incineration kiln and the secondary combustion chamber. After all, the incineration rotary kiln is a critical component of the waste incineration plant. If you are looking for high-quality equipment, please contact us.