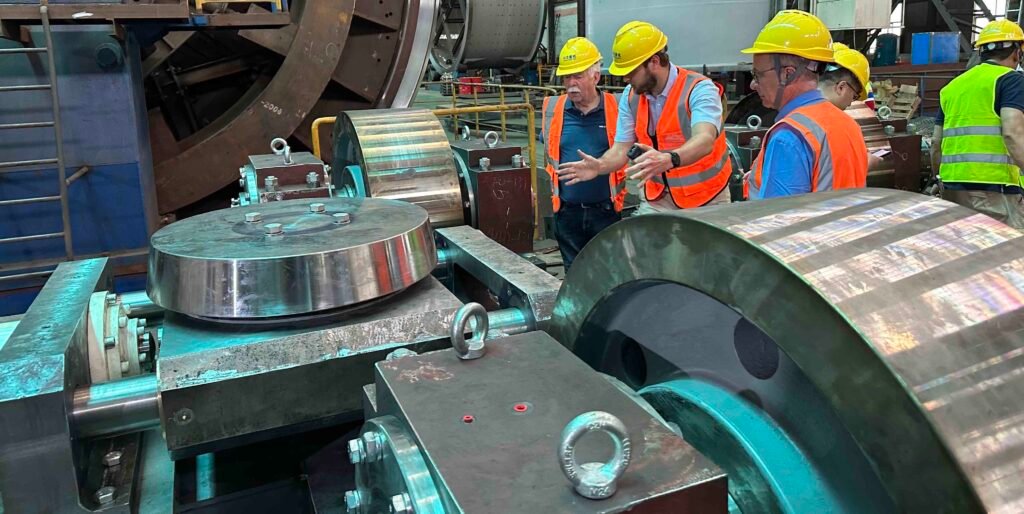
Introduction:
The medical hazardous waste incineration rotary kiln is the core equipment for treating medical waste and harmful waste. It achieves waste reduction, harmlessness and resource utilization through high-temperature incineration 850-1100℃. It adopts an inclined rotating cylinder structure to ensure the complete decomposition of organic pollutants through full contact between the material and the high-temperature flue gas, and the emission of toxic substances such as dioxins meets international standards. In July 10th Customers from Europe came to Tongli to inspect their customized 4.2x15 meter hazardous waste incineration kiln and secondary combustion chamber. The factory acceptance test (FAT) is a key step before the equipment leaves our factory, which aims to verify the design performance, manufacturing quality and operating stability of the rotary kiln. The test content covers the welding quality of the kiln shell, process control documents, flawless detection, etc. The strict implementation of FAT not only lays the foundation for subsequent on-site installation and commissioning, but also ensures the safety and environmental protection of the medical waste treatment process. So in this article we will firstly introduce what incineration is in case you don't know yet, then we will attach the photo taken during the visit of our European customer.
Fundamentals of Waste Incineration
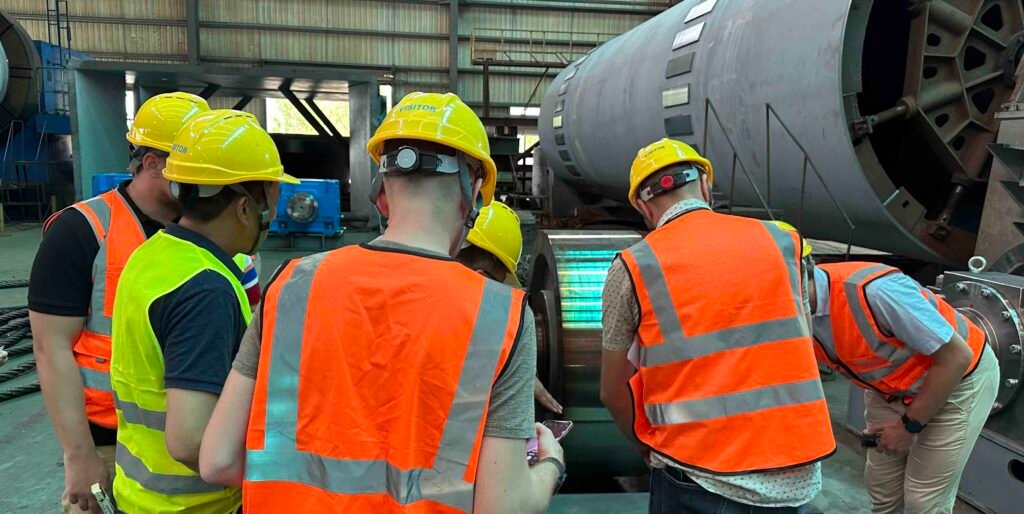
1. What Is Waste Incineration?
Definition: Harzardous waste incineration is a technology that treats solid waste through high-temperature oxidation. It uses a high temperature of more than 850°C to fully burn organic waste in the combustion chamber and convert it into carbon dioxide, water and ash, achieving volume reduction, volume reduction of 80%-90% and harmlessness.
2. How do incinerators for solid waste work? Working principle and mechanism.
Hazardous waste incineration rotary kilns are the core equipment for the incineration of hazardous waste. Through an inclination angle of 3°-5° and a rotation rate of 1.5-3r/min, the waste undergoes a drying and pyrolysis process in the kiln for 15-20 minutes, and the organic components are initially decomposed in the main combustion zone of 850-1000℃. However, due to the complex composition of hazardous waste (including drug residues, chemical reagents, there may be partial incomplete combustion in the main combustion chamber, so it is necessary to connect the secondary combustion chamber to form a secondary incineration system. The secondary combustion chamber raises the flue gas temperature to above 1100℃ through an auxiliary burner, and at the same time uses a wind distribution device to create strong turbulence, so that unburned hydrocarbons, dioxin precursors, etc. are fully mixed with excess air, forcing the flue gas residence time to be ≥2 seconds, and finally achieving a dioxin degradation rate of over 99.99%, and complete oxidation of persistent pollutants such as polycyclic aromatic hydrocarbons. This combined process of "hazardous waste kiln pretreatment + secondary combustion chamber deep purification" not only ensures uniform heating of the material through the rotation of the kiln body, but also relies on the high-temperature turbulent environment of the secondary combustion chamber to compensate for the incomplete reaction in the main combustion stage, jointly meeting the environmental protection requirements of Chinese GB 18484-2020 for hazardous waste incineration.
3. Incineration vs. Other common Waste Disposal Methods.

- Landfilling has low cost and simple operation, but it occupies a lot of land and is prone to soil and groundwater pollution, so it is more suitable for inert waste. Composting is only applicable to organic waste and can be converted into fertilizer, but the processing cycle is long, the volume reduction is limited, and the heavy metal content must be strictly controlled.
- Recycling achieves resource regeneration through classification and sorting, which is environmentally friendly, but is limited by waste types (such as plastics, metals, etc.) and recycling technology, and is less applicable to complex mixed waste.
Incineration vs. Other Waste Disposal Methods comparison table:
Disposal Method | Core Principle | Applicable Waste | Volume Reduction Rate | Environmental Impact | Cost | Limitations |
Incineration | High-temperature oxidation decomposes organic components into flue gas and ash | Hazardous waste, medical waste, complex mixed waste, etc. | 80%-90% | Requires supporting flue gas purification systems (to prevent dioxins, heavy metals, etc.); can meet standards if properly handled | High (equipment investment + operational energy consumption) | High energy consumption, strict emission control required, risk of secondary pollution |
Landfilling | Waste is compacted and buried underground, relying on natural degradation | Inert waste, residues that cannot be incinerated/recycled | 30%-50% | Prone to soil and groundwater contamination; generates landfill gas (methane and other greenhouse gases) | Low (mainly land cost) | Occupies large areas, long degradation cycle, high pollution risks |
Composting | Microbial decomposition of organic waste into organic fertilizer | Biodegradable organics like kitchen waste, crop straw | 30%-60% | Good environmental performance; enables resource recycling | Medium (site + management costs) | Only applicable to organic waste, long processing cycle (weeks to months), needs control of heavy metals and pathogens |
Recycling | Resource regeneration via physical/chemical methods after sorting | Recyclables such as plastics, metals, paper, glass | Varies by type (e.g., metal recycling has almost no volume reduction, only morphological transformation) | Most environmentally friendly; reduces resource consumption and pollution | High (classification cost + recycling technology investment) | Limited by waste type and purity; complex mixed waste requires complicated sorting; some recycling processes still cause pollution |
What are the types of Waste Incineration Systems?
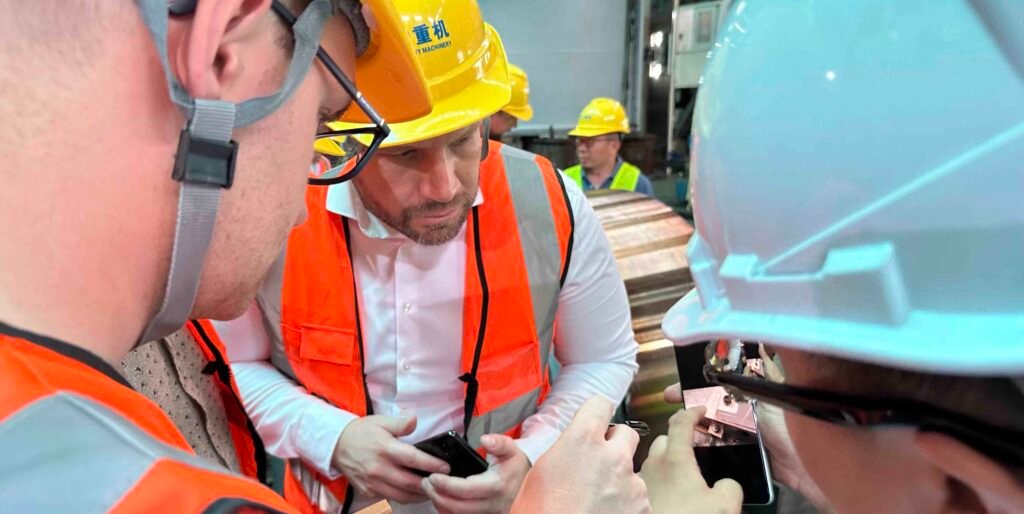
1. Medical Waste Incinerators system:
- Purpose: For medical waste carrying pathogens and chemical pollutants syringes, infectious dressings, discarded medicines, the primary goal is to completely inactivate pathogens and destroy toxic components.
- Technical features: It needs to meet extremely high incineration temperatures usually ≥850℃, chlorine-containing waste needs to be ≥1100℃ and flue gas residence time ≥2 seconds, equipped with a multi-stage flue gas purification system such as activated carbon adsorption, bag dust removal, focusing on the removal of dioxins, heavy metals and pathogenic microorganisms.
- Application scenarios: Medical waste generated by hospitals, disease control centers, etc. belongs to the category of mandatory harmless treatment and must comply with local strict regulations such as the "China Medical Waste Incineration Pollution Control Standards".
2. Hazardous Waste Incineration Technology and Applications
- Function: Treating corrosive, toxic and flammable hazardous wastes (such as waste chemicals, waste oil, heavy metal sludge, etc.). The core is to destroy the chemical stability of the waste and reduce its toxicity.
- Technical features: Using special furnaces such as rotary kilns and fluidized beds, adjusting the feeding method according to the solid, liquid and gaseous forms of the waste, the incineration temperature is 850-1200℃, and the flue gas quenching is required to inhibit the resynthesis of dioxins, and the wet deacidification process is used to control emissions, and the residues must be disposed of according to the hazardous waste standards.
- Application scenarios: Industrial hazardous waste, laboratory waste liquid, etc., are strictly restricted by the "China Hazardous Waste Incineration Pollution Control Standards" and have high technical barriers.
3. Municipal and Yard Waste Incineration Systems
- Function: Treating urban domestic waste such as kitchen waste, plastic, paper and other mixed waste and courtyard greening waste branches, fallen leaves, etc., with volume reduction and energy recovery such as power generation and heating as the main goals.
- Technical features: Due to the complex composition of waste containing high moisture and low calorific value substances, mechanical grate furnaces are often used, with an incineration temperature of 850-1000℃, and heat energy is recovered through waste heat boilers. Flue gas purification focuses on removing dust, acidic gases such as HCl, SO₂ and nitrogen oxides, and the residue can be landfilled or recycled (such as building materials).
- Application scenario: Urban waste treatment plants, taking into account environmental protection and energy regeneration, are regulated by the "China Municipal Waste Incineration Pollution Control Standard".
So far, we have covered what waste incineration is. Now, let's move on to the second part of the article, the factory acceptance test of the key equipment of waste incineration, the rotary kiln.
Hazardous Medical Waste Incineration Rotary Kiln FAT Factory acceptance test:
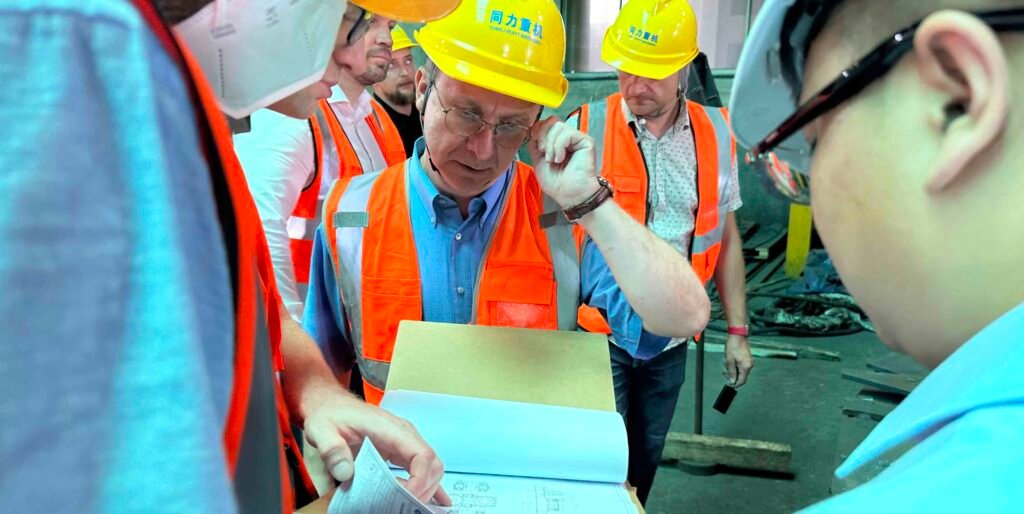
On July 10th, Customers from Europe and Poland visited Tongli to check their waste incineration rotary kiln manufacturing process and schedule.
What is a factory acceptance test for incineration rotary an kiln?
Incineration rotary kiln factory acceptance test (FAT) is a systematic inspection and verification conducted at the manufacturer's facility before shipment, aiming to confirm that the kiln and its components (such as drive system, support structure, combustion system) meet the design specifications, technical requirements, and performance criteria outlined in the purchase contract. It typically includes visual checks, dimensional measurements, functional tests, rotation accuracy, sealing performance, and partial load trials to ensure the equipment is ready for on-site installation and commissioning. But usually the load trial will only be performed on-site.
What are the parts of a medical hazardous waste incineration plant rotary kiln?
1. Rotary Kiln Shell:
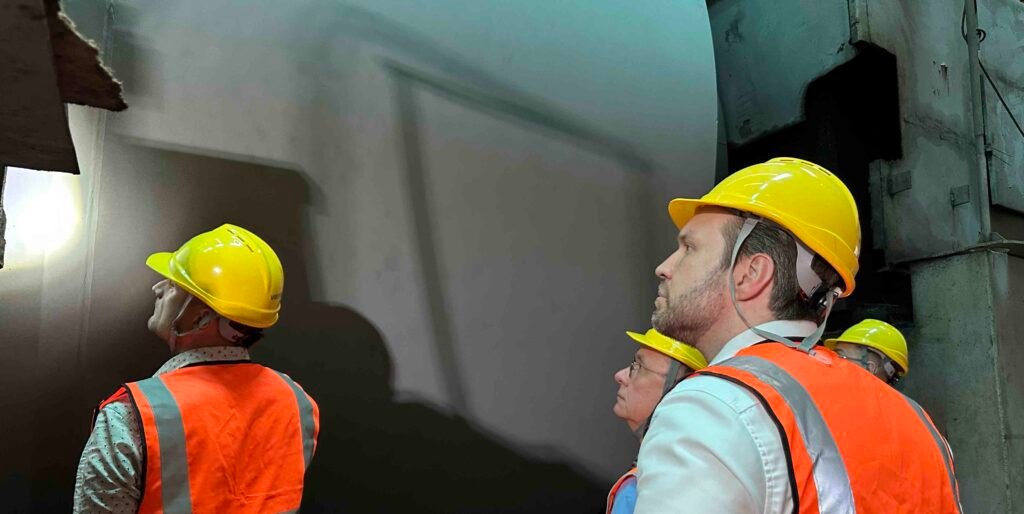
The waste incineration kiln shell is a long, cylindrical, horizontally mounted steel shell, typically inclined at a slight angle (1–5 degrees) to facilitate the movement of waste from the feed end to the discharge end as it rotates. It Serves as the primary combustion chamber where waste is heated, dried, and oxidized at high temperatures (850–1,200°C, depending on waste type). The rotation (1–5 rpm) ensures uniform mixing and exposure to heat, preventing localized cooling and ensuring complete combustion.
2. Support Rolls and Riding Rings and Thrust roller:
Riding ring:
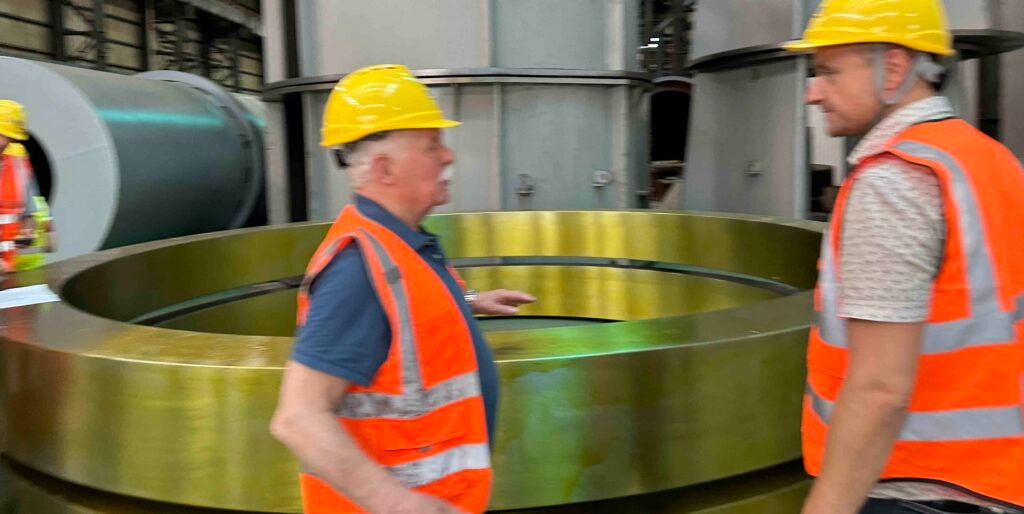
The riding ring of a incineration kiln is a large steel ring that is sleeved on the outside of the kiln shell. It is a key component that connects the kiln shell and the supporting wheel. Its core function is to evenly transfer the weight of the kiln body to the supporting wheel and reduce the deformation of the kiln shell.
Features of incineration kiln riding ring:
- Structure: Usually a solid or hollow forged ring, the size is designed according to the diameter of the kiln and the load (the diameter can reach several meters and the weight can reach tens of tons). Some rollers are fixed to the kiln shell by welding or bolts, and there is also a "loose sleeve" design (retaining a small gap with the kiln shell), allowing the kiln shell to slide relative to each other when it expands due to heat to avoid stress concentration.
- Material: High-strength heat-resistant steel (such as ZG35CrMo, ZG42CrMo, etc.) is used, which must have high temperature resistance (long-term resistance to 300-500℃ kiln shell heat conduction), fatigue resistance and wear resistance to cope with long-term rotational friction and temperature fluctuations.
- Function: Load transfer, the weight of the kiln body itself (including the steel kiln shell, internal refractory lining), the weight of the garbage to be incinerated, and the impact load of the materials generated during the incineration process are all transferred to the supporting wheel below through the roller to avoid direct force deformation of the kiln shell.
- Function: Stabilize the kiln body. The rollers limit the radial shaking of the kiln body by contacting the supporting wheel to ensure the concentricity during rotation. At the same time, multiple rollers (usually 2-3 groups) are distributed at different positions of the kiln body to form multi-point support to balance the deflection of the long kiln body (avoid "drooping" due to the kiln body being too long).
- Function: Adapt to thermal deformation. During garbage incineration, the kiln shell will expand due to high temperature (the temperature in the kiln can reach 800-1200℃). The "loose sleeve" design or elastic connection structure of the rollers allows the kiln shell to expand and contract slightly in the axial or radial direction to prevent cracking due to thermal stress.
- Special design requirements: It needs to withstand temperature fluctuations during garbage incineration (the external temperature of the kiln shell may fluctuate violently due to changes in the working conditions in the kiln), so the material needs to have good thermal shock resistance;
- Special design requirements: Due to the complex composition of garbage (may contain corrosive substances), the surface of the rollers needs to have a certain degree of corrosion resistance, or extend its life through regular maintenance (such as painting high-temperature resistant paint).
Support roller:
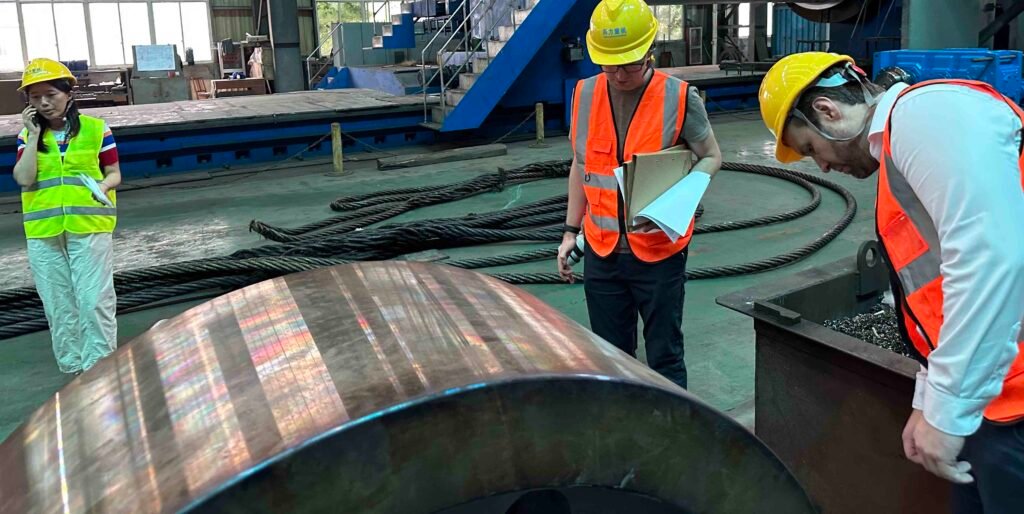
The support roller is a steel roller installed in pairs under the roller ring. It supports the entire kiln body through rolling contact with the roller ring and allows the kiln body to rotate around the axis. It is the "fulcrum" that bears the weight of the kiln.
Features of support roller:
- The support roller is a steel roller installed in pairs under the roller ring. It supports the entire kiln body through rolling contact with the roller ring and allows the kiln body to rotate around the axis. It is the "fulcrum" that bears the weight of the kiln.
- Structure: Usually two groups are symmetrically arranged on both sides of the roller ring (forming an "eight-shaped" or "horizontally symmetrical" support). Each group of support rollers consists of rollers, shafts, bearing seats and bases. The roller surface is processed into an arc shape to match the outer cylindrical surface of the roller ring to ensure uniform contact.
- Material: The roller body is mostly made of high-strength alloy forged steel (such as 42CrMo), and the surface is heat treated (quenching + tempering) to improve hardness (HRC40-50) and wear resistance; the bearing needs to adapt to high temperature environment, usually self-aligning roller bearings or sliding bearings, and equipped with a forced cooling system (such as water cooling or oil cooling).
- Load and support: Directly bear all the loads transmitted by the roller ring (including kiln body, garbage, refractory materials, etc., with a total weight of hundreds of tons), and disperse the load to the foundation or steel structure support.
- Auxiliary rotation: Through rolling friction (not sliding friction) with the roller, the resistance of the kiln body during rotation is reduced, so that the kiln shell can rotate smoothly under the drive device (such as gears, motors) (the speed is usually 0.5-5 rpm, adjusted according to the working conditions of waste incineration).
- Guiding and centering: The installation angle and position of the support wheel are precisely adjusted to indirectly limit the radial deviation of the kiln body, ensure the maximum contact area between the roller and the support wheel, and avoid excessive local wear.
- Special requirements: Due to the unstable load of the waste incineration kiln (fluctuations in the amount of waste feed may cause sudden load changes), the support wheel needs to have high impact resistance;
- Special requirements: Regular lubrication (using high-temperature grease or lubricating oil) is required to reduce friction and wear with the roller, and prevent excessive temperature due to frictional heat (which may cause bearing failure).
Thrust roller:
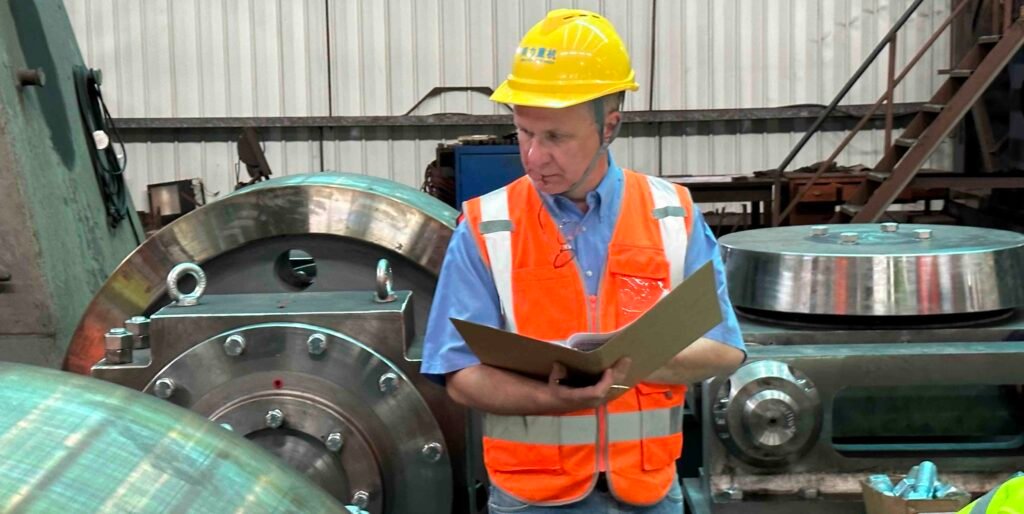
The thrust wheel is an auxiliary supporting component used to limit the axial (horizontal) movement of the kiln body during rotation and ensure the relative position stability of the kiln body and other equipment (such as the feed port, discharge port, and secondary combustion chamber).
Features:
- Structure: Usually a single or paired cylindrical roller, installed on the side of the roller (close to the end face of the roller), and in contact with the axial end face of the roller. Some thrust wheels are designed as adjustable structures (position adjustment by hydraulic or mechanical devices) to adapt to the thermal expansion of the kiln body.
- Material: Similar to the support wheel, it is made of high-strength alloy forged steel, the surface must be wear-resistant and high-temperature resistant, and equipped with a buffer device (such as a spring or hydraulic cylinder) to absorb axial impact.
- Function: Limit axial movement. When the kiln body rotates, axial displacement (horizontal forward and backward movement) may occur due to temperature changes (thermal expansion and contraction), eccentric load of materials or slight deviation of the drive device. The thrust wheel contacts the end face of the roller to prevent excessive movement (usually allow a slight displacement, such as ±5mm), and avoid collision between the kiln body and the feed port, discharge port and other components.
- Function: Compensate for thermal expansion. When the kiln body is heated and elongated during garbage incineration, the thrust wheel can be adjusted through elastic design or gap adjustment to allow the kiln body to axially expand and contract within a safe range, while preventing structural deformation caused by excessive expansion.
- Function: To protect other components. If the kiln body moves too much in the axial direction, it may cause poor gear meshing (kiln body drive gear and motor gear misalignment) and increased wear of sealing devices (such as kiln head and kiln tail seals). The existence of thrust wheels can reduce such risks.
- Special design requirements: It must have sensitive responsiveness and be able to prevent abnormal axial displacement in time (such as movement caused by load eccentricity caused by garbage agglomeration);
- Special design requirements: The contact pressure with the end face of the rolling ring must be strictly controlled. Too much pressure will cause local wear or overheating, and too little pressure will not play a thrust role. Therefore, it is usually equipped with a pressure sensor or a gap monitoring device.
How do the above 3 parts work together as a whole? riding ring/thrust roller/support roller?
During the operation of the waste incineration rotary kiln, the roller transfers the weight of the kiln body to the supporting roller, the supporting roller supports the kiln body and assists in rotation, and the thrust wheel limits axial movement. The three form a closed-loop system of "support-rotation-positioning": when the kiln body rotates driven by the drive device, rolling friction is generated between the roller and the supporting roller to ensure low-resistance operation; when the kiln body moves axially due to thermal expansion and contraction or load changes, the thrust wheel contacts the end face of the roller to prevent excessive displacement; the materials and structures of the three must adapt to the high temperature, corrosive, and load-fluctuating waste incineration environment, and require regular maintenance (such as checking wear, adjusting clearance, and replacing grease) to extend their service life.
3. Drive transmission system
The transmission system of the incineration rotary kiln is mainly composed of four parts: motor, gearbox, pinion, and ring gear. Each component works together to complete the whole process of "power generation - torque conversion - power transmission":
Motor:
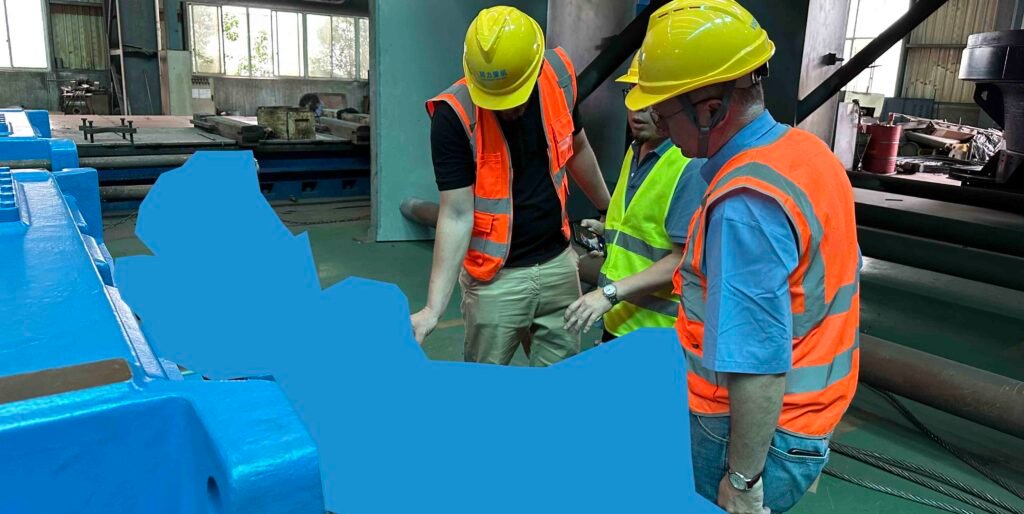
As a power source, AC asynchronous motors (small and medium-sized kilns) or DC motors (large kilns or scenarios requiring speed regulation) are usually used. Some high-end systems will be equipped with variable frequency speed regulators (VFDs) to achieve precise speed control.
- Function: Output high-speed, low-torque initial power (speed is usually 1000-1500 rpm), adjust the output power through an electrical control system (such as PLC) to adapt to changes in the amount of material in the kiln and the incineration load (for example, increase the speed when the feed amount increases to avoid material accumulation).
- Special design: Considering the high temperature and dust characteristics of the incineration environment, the motor needs to be equipped with a cooling system (air cooling or water cooling) and a dust cover. Some scenarios use explosion-proof motors to deal with potential flammable gas risks.
Gearbox:
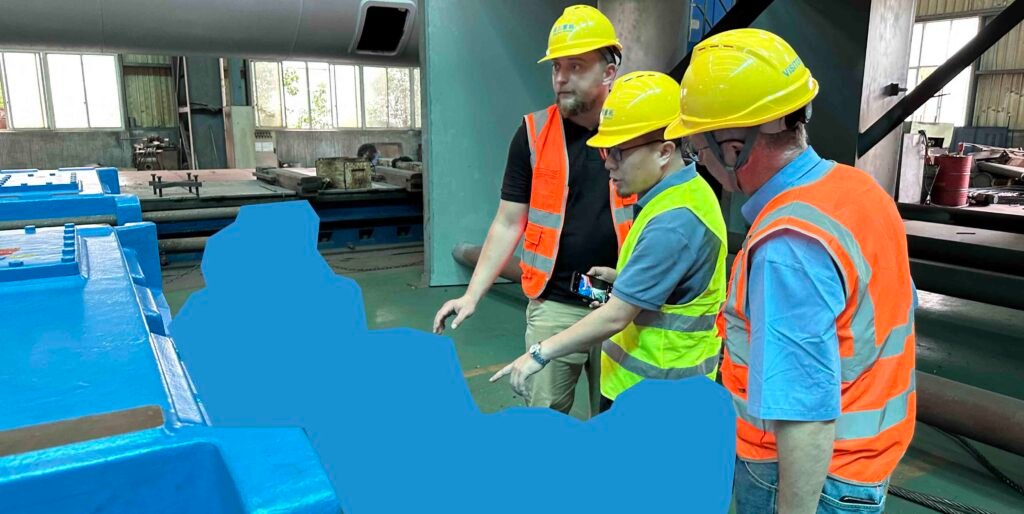
Also known as reducer, it is the "torque converter" of the transmission system. It converts the high speed and low torque output by the motor into the low speed and high torque required to drive the kiln through multi-stage gear meshing (usually helical gear or planetary gear structure).
- Reduction ratio: According to the design speed of the kiln, the reduction ratio of the gearbox is usually 100:1 to 500:1 (for example, the motor input is 1500 rpm, and the output is 5 rpm after 300:1 reduction).
- Core requirements: It must have high-strength load-bearing capacity (to withstand the axial and radial forces of the kiln), a good lubrication system (forced circulation lubrication to avoid gear wear at high temperatures) and overload protection functions (such as torque limiter to prevent gear damage when foreign objects are stuck).
Pinion gear:
Forged from high-strength alloy steel (such as 42CrMo) and surface hardened (hardness HRC55-60), the tooth shape is designed as helical teeth (compared with straight teeth, it can reduce meshing impact, reduce noise and improve transmission efficiency).
- Installation location: Connected to the output shaft of the gearbox through a coupling, it maintains precise meshing with the large ring gear (meshing clearance is usually 0.2-0.5mm), and converts the torque transmitted by the gearbox into circumferential force.
Girth gear:
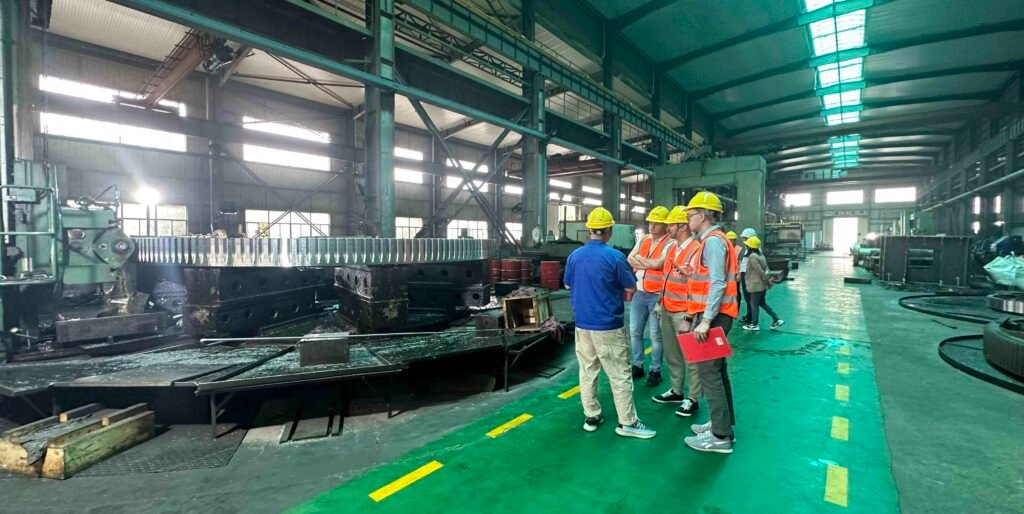
As the terminal actuator of power transmission, it is a large ring gear fixed in the middle of the kiln body or near the support roller by bolts or welding (needs to be concentric with the kiln body, radial runout ≤0.5mm/m).
- Material and structure: It is made of cast steel (such as ZG35CrMo) as a whole or segmented splicing (large kiln), and the tooth surface is quenched and tempered to improve wear resistance; an elastic buffer device (such as a rubber pad) is usually set between the inner ring and the kiln shell to reduce the influence of thermal deformation of the kiln body on gear meshing.
- Function: When meshing with the pinion, the circumferential force is converted into torque to drive the kiln body to rotate, driving the entire kiln shell and the internal materials to rotate synchronously.
How do the above 3 parts work togethe?
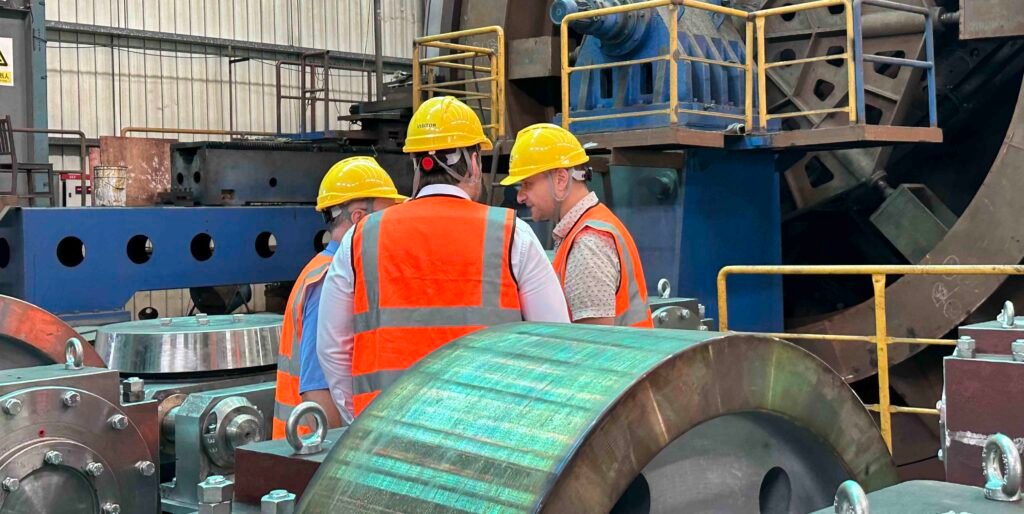
The power transmission path of the transmission system can be summarized as follows: The motor outputs high-speed power → The gearbox amplifies the torque through multi-stage reduction → The small gear transmits power to the large ring gear → The large ring gear drives the kiln body to rotate at a low speed. Key logic: The core purpose of the kiln body rotation is to achieve full contact with the high-temperature flue gas (improve the incineration efficiency) and uniform heating of the material (avoid local overheating or incomplete combustion) through the turning of the material in the inclined kiln body (the kiln body is usually tilted 1-3°), and at the same time push the material to move to the slag discharge end of the kiln tail. The speed stability of the transmission system directly determines the material residence time (usually 1-2 hours), which is a key parameter to ensure the thoroughness of incineration (incineration removal rate ≥ 99.99%).
Challenges facing in terms of high temperature waste incineration:
Low-speed, high-torque characteristics
The total weight of the kiln body can reach hundreds of tons (such as a kiln body with a diameter of 4 meters and a length of 30 meters). The transmission system needs to continuously output thousands of Newton meters (or even tens of thousands of Newton meters) of torque. Therefore, the structural strength and material toughness (impact resistance and fatigue resistance) of the gearbox and gear pair are the core of the design.
Dynamic adaptability
The fluctuation of the amount of material in the kiln (such as "agglomeration" caused by uneven garbage composition) and the thermal deformation of the kiln body caused by high temperature (the axial expansion can reach tens of millimeters) will cause the transmission load to change instantly. Therefore, the system needs to have: flexible transmission capability (such as adjustable gear meshing clearance); overload protection mechanism (such as motor overload tripping, gearbox torque limiter slippage).
High-temperature environment adaptability
The surface temperature of the kiln body can reach 300-500℃ when it is working, and the heat affects the nearby transmission components (especially the large ring gear and pinion) through radiation and conduction. The design needs to adopt:
- Forced cooling (such as large ring gear spray cooling, gearbox oil cooling system);
- Thermal expansion compensation (such as the position of the pinion can be fine-tuned to compensate for the thermal deformation of the large ring gear).
4. Refractory Lining
Material: Heat-resistant materials (e.g., high-alumina bricks, castable refractories, or ceramic fiber) lining the inner surface of the kiln shell. Function: Insulates the steel shell from extreme temperatures (preventing deformation or melting), retains heat within the kiln to maintain combustion temperatures, and resists abrasion from waste materials. Since refractory is done on-site so we are not expanding it.
5. Feed System & Front panel
Waste Charging/feeding portal:
- Ram Feeder: A hydraulically driven push rod is used to periodically push garbage into the kiln. It is suitable for large or tough garbage. The feed amount can be adjusted by stroke and frequency.
- Screw Conveyor: A rotating screw is used to push garbage. It is suitable for loose materials. It has both quantitative conveying and sealing functions. It needs to be equipped with wear-resistant linings to deal with hard impurities in the garbage.
- Chute: A simple inclined channel that relies on gravity feeding. It is usually used with a gate valve to control the flow rate. It is mostly used for fine garbage after pretreatment.
Air Lock
- Core function: Isolate the high pressure (or slightly negative pressure) environment in the kiln from the outside atmosphere during the feeding process, prevent cold air from infiltrating or smoke from overflowing, and ensure stable combustion conditions.
- Dual-Chamber Valve: It consists of two gate valves in series, which are switched alternately to achieve "close first and then open" - when feeding, the upstream gate is opened first, and the garbage enters the middle chamber and is closed, and then the downstream gate is opened to send it into the kiln to avoid direct airflow.
- Rotary Valve: The chamber is separated by a rotating rotor with blades. The gap between the blade and the shell is extremely small (usually ≤1mm), which is suitable for continuous feeding and needs to withstand garbage impact and high temperature radiation.
6. Secondary Combustion Chamber (SCC)
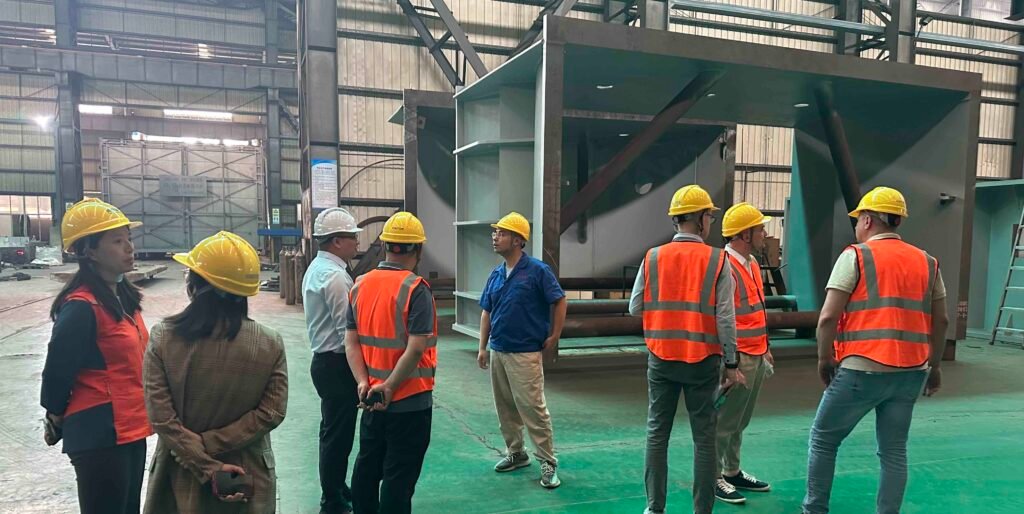
Positioned downstream of the kiln’s discharge end, it ensures destruction of hazardous compounds (e.g., dioxins, furans, volatile organic compounds) by maintaining high temperatures (typically 1,000–1,200°C) for a minimum residence time (2+ seconds), as required by environmental regulations.
SCC Structural design:
- Spatial layout: mostly vertical or horizontal steel containers, lined with high-aluminum refractory bricks (resistant to high temperatures of 1200-1400℃), the volume is designed according to the "smoke residence time" (usually ≥2 seconds), and the cross-sectional wind speed is controlled at 3-8m/s to ensure turbulent mixing.
- Air distribution method: secondary air nozzles are set on the top or side (usually arranged in multiple layers and multiple angles), the secondary air temperature is ≥250℃ (after preheating), and it forms a strong swirl or counterflow with the flue gas to enhance mass transfer and heat transfer.
- Key interface: the inlet is connected to the kiln tail (expansion joints are required to compensate for thermal deformation), the outlet is connected to the waste heat boiler or quenching tower, and an ash hopper is set at the bottom to collect high-temperature molten ash.
Secondary combustion chamber core function:
- Complete combustion: oxidize the unburned combustibles (such as CO, hydrocarbons) in the kiln into CO₂ and H₂O, with a removal rate of ≥99.9%, so that the CO concentration in the flue gas is ≤50ppm.
- Pollutant decomposition: Under the conditions of above 850℃ and residence time ≥2 seconds, the decomposition efficiency of dioxin-like substances can reach 99.99% (based on the "3T+E" principle: Temperature, Time, Turbulence, Excess Air).
- Heat recovery: After passing through the secondary combustion chamber, the high-temperature flue gas (1000-1200℃) enters the waste heat boiler to achieve heat recovery (generating steam for power generation or heating) and improve the energy efficiency of the system.
Secondary combustion chamber Key points of operation control:
- Temperature control: By adjusting the secondary air flow and auxiliary burners (such as natural gas burners), ensure that the center temperature of the furnace is stable at 850-1100℃ (the critical temperature for dioxin decomposition is 800℃, and the decomposition rate increases 10 times for every 50℃ increase).
- Parameter coordination: Strictly follow the "3T principle" - temperature (≥850℃), residence time (≥2 seconds), turbulence (oxygen content 6-10%), all three are indispensable.
- Anti-corrosion design: For corrosive gases such as HCl and SOx in flue gas, the refractory material must be corrosion-resistant magnesia-chrome bricks or silicon carbide products, and the metal shell is equipped with an insulation layer (external wall temperature ≤50℃).
7. Ash Discharge System
- Cooling Conveyor: A system (e.g., water-cooled screw conveyor or vibrating conveyor) that removes ash and slag from the kiln’s discharge end, cooling it to prevent re-ignition and facilitate handling.
- Ash Collection: Hoppers or bins to collect bottom ash (from the kiln) and fly ash (from downstream gas cleaning systems) for further treatment (e.g., stabilization) or disposal.
8. Flue Gas Cleaning System
Post-Combustion Treatment: Equipment downstream of the SCC to remove pollutants from exhaust gases, including:
- Acid Gas Scrubbers: Remove sulfur dioxide (SO₂), hydrogen chloride (HCl), and hydrogen fluoride (HF) using lime or sodium-based reagents.
- Particulate Control: Baghouses or electrostatic precipitators (ESPs) to capture fly ash and fine particulates.
- Heavy Metal and Dioxin Removal: Activated carbon injection to adsorb heavy metals (e.g., mercury) and dioxins.
- Denitrification Systems: To reduce nitrogen oxide (NOₓ) emissions, often using selective non-catalytic reduction (SNCR) or selective catalytic reduction (SCR).
9. Stack (Chimney)
Releases treated flue gases into the atmosphere at a height sufficient to disperse remaining pollutants, ensuring compliance with local air quality standards.
10. Combustion Air System
- Primary Air: Fans that blow air directly into the kiln through ports in the shell or feed end, providing oxygen for initial combustion of volatile components in the waste.
- Secondary Air: Preheated air injected into the kiln’s discharge end or a downstream secondary combustion chamber (SCC) to support complete oxidation of unburned gases (e.g., CO, hydrocarbons) and reduce emissions.
Energy Recovery & Economic Considerations Harzardous incineration:
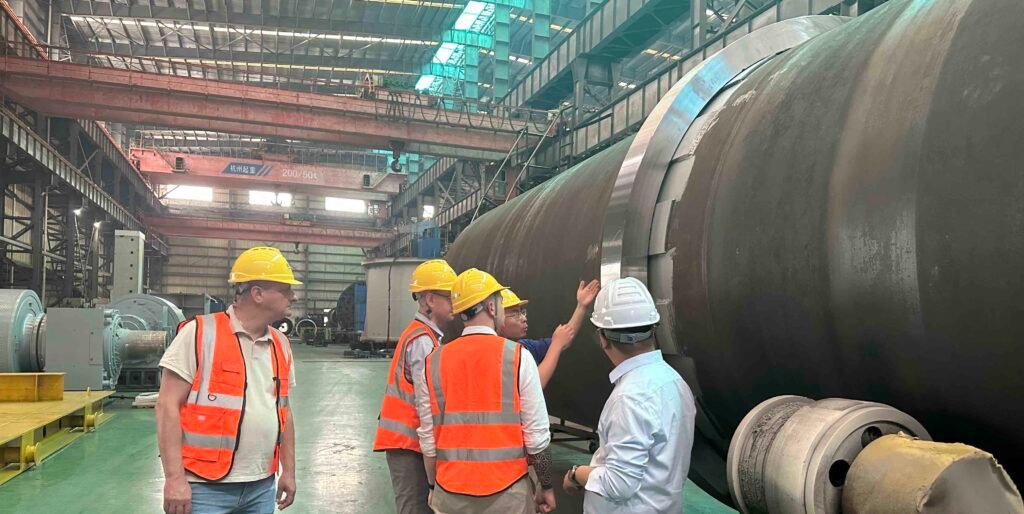
If we go one step further, then the process of waste incineration can also integrate power generation. Please check the below option for waste incineration:
1. Waste-to-Energy (WTE) Incineration Explained
Waste-to-Energy (WTE) is another efficient treatment method that converts solid waste, such as municipal solid waste, into electrical energy through high-temperature incineration. Its core lies in converting the chemical energy contained in the garbage into usable electrical energy.
Waste to energy process flow
In terms of process flow, the garbage first enters the pretreatment system. At this stage, impurities such as metals and masonry are separated through mechanical sorting, magnetic separation and other technologies to improve the calorific value and uniformity of the garbage and ensure the stability and efficiency of the subsequent incineration process. The pretreated garbage enters the incinerator. Common furnace types include mechanical grate furnaces and fluidized bed incinerators. In a high temperature environment of 850-1000℃, the organic components in the garbage are fully burned. Taking the mechanical grate furnace as an example, the movement of the grate drives the garbage to roll, so that it is fully in contact with the air and completes the combustion process. The high-temperature flue gas generated by incineration enters the waste heat boiler, exchanges heat with the water in the boiler, and heats the water into high-temperature and high-pressure steam. The steam drives the steam turbine to rotate at high speed, which in turn drives the generator to generate electricity. The steam after power generation is cooled by the condensation system and turned back into water for recycling. At the same time, the flue gas containing pollutants such as acidic gases (such as HCl, SO₂), dust, dioxins and heavy metals generated during the incineration process will enter the multi-stage purification system. Through semi-dry deacidification, activated carbon adsorption, bag dust removal and other processes, pollutants are removed to ensure that the final flue gas emissions meet national environmental protection standards, such as GB 18485-2014 "Standards for Pollution Control of Domestic Waste Incineration".
Economic benefit of waste incineration to energy
In terms of economic benefits, waste incineration power generation projects have diversified income. Power generation income is one of the main sources, generally accounting for 65%-75%. Each ton of garbage can generate 300-500 kWh of electricity, which is affected by factors such as the calorific value of the garbage, the incineration equipment and the efficiency of the power generation system. Taking a power plant that processes 1,000 tons of garbage per day as an example, if a ton of garbage generates 400 kWh of electricity, based on the industrial electricity price of $0.07/kWh, the income from power generation alone can reach approximately $27,800 per day. Another important source of income is the waste disposal fee, which is paid by local governments and accounts for 25%-35% of the project income. Due to differences in economic level and waste production in different regions, the standard of disposal fee ranges from $11 to $28 per ton. Some projects can also increase their income through the comprehensive utilization of slag. The slag produced after waste incineration is separated and recycled by magnetic separation, screening and other processes. The remaining slag can be made into cement bricks, paving substrates and other building materials to achieve resource utilization. In addition, with the improvement of the carbon trading market, waste incineration power generation projects can obtain additional income through carbon trading by reducing greenhouse gas emissions such as methane generated by landfills.
2. Adventage of waste Incineration
Significant reduction effect:
After high-temperature incineration, the volume of garbage can be reduced by 80%-90%, and the weight can be reduced by 70%-80%, which greatly reduces the land occupation demand for subsequent landfill or stacking. For cities with tight land resources (such as Tokyo and Shanghai), this advantage is particularly critical and can effectively alleviate the pressure of landfill site selection.
Energy recovery and resource utilization:
The heat energy released during the incineration process can be converted into steam through waste heat boilers to drive steam turbines for power generation or heating, realizing "waste-to-energy" conversion. In a typical project, each ton of garbage can generate 300-500 kWh of electricity, which is enough to meet the electricity needs of 1-2 households for one day. Some projects can also provide steam for surrounding industrial facilities to form a circular economy chain.
Reducing greenhouse gas emissions:
Compared with landfill (which produces a large amount of methane, whose greenhouse effect is 28 times that of CO₂), incineration converts organic matter into CO₂ through high-temperature oxidation, and energy recovery can replace fossil fuel power generation, indirectly reducing carbon emissions. According to EU data, waste incineration projects can reduce greenhouse gas emissions by about 0.5 tons of CO₂ equivalent per ton of waste on average, which meets the environmental protection requirements under the "dual carbon" goal.
Harmless treatment of risky substances:
High-temperature incineration (above 850℃, some furnace types reach 1100℃) can completely decompose pathogenic microorganisms and toxic organic matter (such as dioxin precursors) in the garbage, and through the flue gas purification system (such as activated carbon adsorption, bag dust removal), it can effectively control the emission of pollutants such as heavy metals and acidic gases, and reduce the risk of soil and groundwater pollution.
Diversified economic benefits:
In addition to power generation income, the project can obtain government waste treatment subsidies (such as 80-200 yuan/ton in some cities in China, 30-50 euros/ton in some European countries), and the slag can be processed into building materials (such as unburned bricks, roadbed aggregates) to generate additional income. For areas with stable garbage production, long-term operation can achieve cost coverage and profitability.
2. Disadventage of waste Incineration:
2.1 High initial investment and operating costs:
The construction of incineration plants requires a large amount of capital for core equipment (such as mechanical grate furnaces, waste heat boilers, flue gas purification systems) and supporting facilities (such as garbage storage tanks, leachate treatment stations). The investment per ton of garbage treatment capacity is about 500,000-800,000 yuan (China) or 100,000-150,000 US dollars (Europe and the United States). During operation, flue gas purification (such as deacidification, dioxin removal), equipment maintenance and personnel costs account for a high proportion, which may put economic pressure on small and medium-sized enterprises.
2.2 Difficulty in controlling pollutant emissions:
Despite significant technological advances, incineration may still produce pollutants such as dioxins, a highly toxic persistent organic matter, heavy metals such as mercury and lead, and nitrogen oxides. If the purification system is not operated properly or supervision is lacking, it may cause pollution of the surrounding air and soil. For example, in the 1990s, some old incineration plants in Europe caused public protests due to excessive emissions, which prompted stricter emission standards such as the EU Waste Incineration Directive.
2.3 Highly depends on the calorific value and stability of garbage
The incineration efficiency is closely related to the composition of garbage: if the kitchen waste and water content are too high for example, the water content of domestic garbage in some cities in China exceeds 50%, the combustion temperature will be reduced and the consumption of auxiliary fuels such as diesel and natural gas will be increased; if there are too many impurities such as metals and glass, it may wear the grate or affect the flue gas treatment. Therefore, a pre-treatment system such as sorting and drying is required, which further increases the cost.
Conclusion:
In this article, we have provided an overview of what a waste incineration rotary kiln is and how it operates within the context of solid, medical, or hazardous waste treatment. We covered the fundamental working principles, including waste feeding, combustion, temperature control, and gas flow management. Additionally, we introduced the main structural components of the incineration kiln system, such as the rotary shell, riding rings, thrust rollers, gear drives, refractory lining, burners, and sealing systems—all of which play a critical role in maintaining stable operation and thermal efficiency. To expand on this topic, our upcoming article will focus specifically on the factory inspection and quality assurance procedures for this CE-certified waste incineration rotary kiln. We will go into detail about the step-by-step inspection process, including dimensional checks, welding flaw detection, non-destructive testing (NDT), material traceability, alignment inspection, component load testing, and overall functional validation prior to shipment. This will provide a comprehensive view of how we ensure the kiln meets international standards and customer-specific technical requirements before delivery. If you want to see more picture taken during this customer's last visit in June click here: Rotary Kiln Incineration Plant Manufacturer Factory Visit by European Customer.