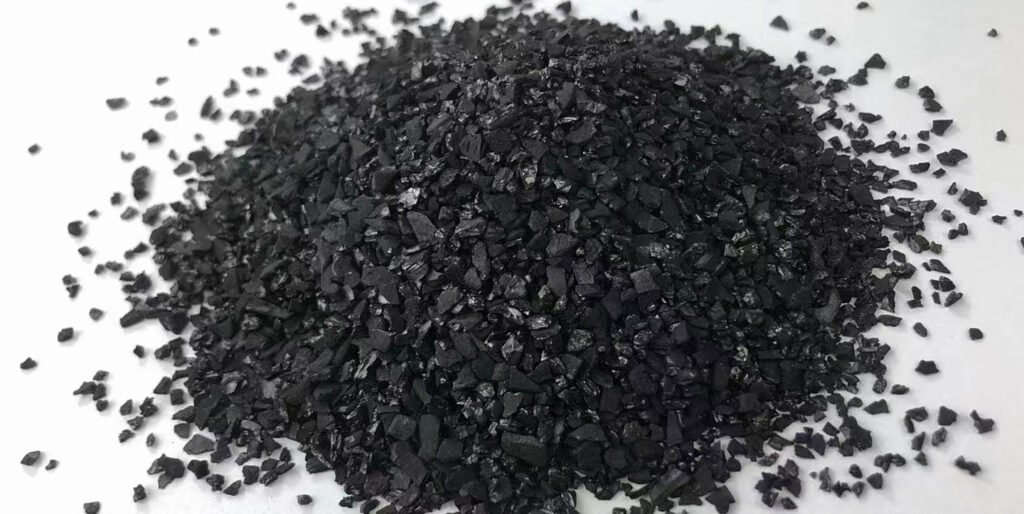
As a porous adsorption material, activated carbon plays an irreplaceable role in environmental protection, energy storage, and chemical separation. The essence of activated carbon production is to open the pore structure of carbonaceous raw materials by physical or chemical methods to create a huge specific surface area. After oxygen treatment, carbon with a high porosity surface is formed. This unique structure enables activated carbon to effectively adsorb and remove impurities from liquids and gases. Activated carbon has a wide range of uses, from air and water filtration to medical and cosmetics. However, to ensure the efficacy and safety of activated carbon, it is crucial to make it correctly. Poor-quality activated carbon will contain harmful contaminants or lack the porosity required to effectively adsorb impurities. We will guide you step by step through the activated carbon production process to help you make high-quality activated carbon that meets your needs. We will also discuss the importance of using the right equipment and taking safety precautions during the production process.
What is Activated Carbon
Activated carbon is a microcrystalline, non-graphite-like carbon that has been processed to increase its porosity. Activated carbon is characterized by a large specific surface area, typically 800 to 1500 square meters per gram, and in some cases up to 2500 square meters per gram. Activated carbon has a wide range of uses due to its large specific surface area, both as a catalyst support and as an adsorbent. As a catalyst support, activated carbon provides a large specific surface area for chemical reactions and is more stable than ordinary inorganic molecular sieves at high temperatures. The adsorption properties of activated carbon are due to its large surface area, high surface reactivity, and suitable pore size, which allows gases and liquids to pass through its internal surface area. Generally, the larger the surface area of activated carbon, the greater its adsorption capacity. The available surface area of activated carbon depends on its pore volume. Since the surface area per unit volume decreases as the individual pore size increases, the larger surface area can be optimized by maximizing the number of very small pores and/or minimizing the number of very large pores. Activated carbon can be used as an adsorbent to efficiently remove pollutants from liquids and gases in environmentally relevant processes. Activated carbon can also be used as a gas storage material. One of the most promising applications is methane storage. The adsorption of methane in the micropores of activated carbon increases the density of the gas. Therefore, the amount of methane stored using adsorbents is much higher than that obtained under pressure.
Activated carbon preparation
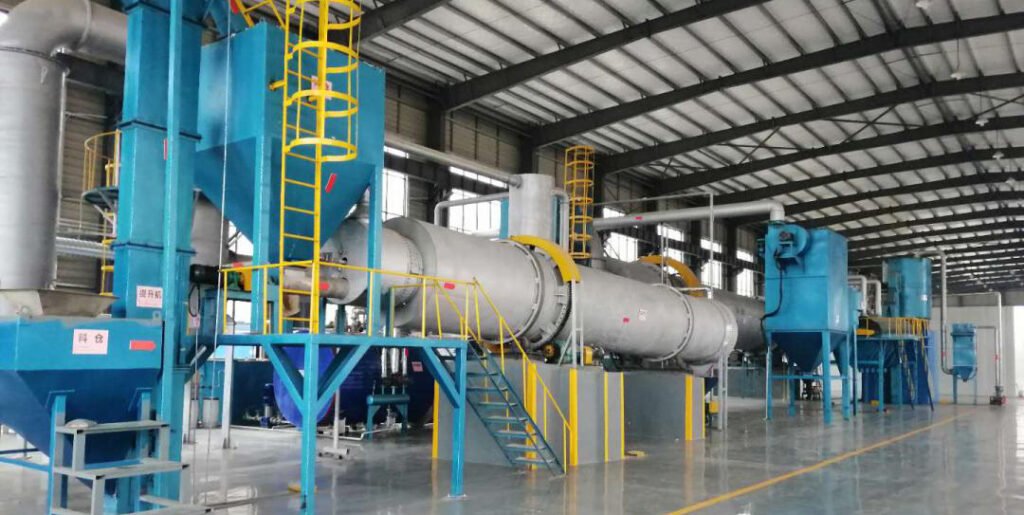
Basic Principles
The preparation of activated carbon is based on two core processes: carbonization and activation. Carbonization is the heating of biomass or mineral raw materials to 400-600℃ in an oxygen-deficient environment to remove volatile components and form a carbon-rich skeleton. This stage is divided into three reaction processes: a primary decomposition reaction below 400℃, an oxygen bond breaking reaction at 400-700℃, and a deoxidation reaction at 700-1000℃, which eventually forms a carbonized product with a three-dimensional network structure. However, the adsorption capacity of carbides is limited because their pores are blocked by pyrolysis products. Activation selectively oxidizes the carbon skeleton at 600-1200℃ through an oxidizing medium (such as water vapor, carbon dioxide or chemical reagents), removes pore blockers, expands existing pores and creates new micropores, thereby forming a developed porous structure.
In essence, the original carbon material is filled with other substances, such as organic matter, which fill the micropores or pores in the carbon material. The process first removes these substances, leaving pure (or nearly pure) carbon. The microscopic pores that were previously filled with other substances are now empty, greatly increasing the surface area of the carbon. The measurement of the voids in the material is called porosity. But the process is not yet complete. The carbon now needs to be "activated" through oxidation. Once the material has gone through the activation process, it can adsorb and hold toxins and molecules. There are two common methods for activating carbon (or charcoal) materials. The first is called steam activation, also known as physical activation. In this process, hot gases are used to transform the raw materials, and then the gases are burned off with air. Physical activation uses carbonization or activation/oxidation, which can require temperatures in excess of 600 degrees Celsius. Another method used to activate carbon is chemical activation. In this process, the raw materials are impregnated with a chemical, usually an acid, base, or some kind of salt. It is then treated at lower temperatures, usually around 450 to 900 degrees Celsius. Due to the lower temperatures required, chemical activation is generally a more efficient and effective method for activating activated carbon.
Mainstream preparation methods and processes
Physical activation method
The physical activation method, also known as gas activation method, is the most traditional activated carbon preparation process:
- Raw material processing: After crushing and screening, raw materials such as wood, coconut shells or coal are first carbonized in an inert atmosphere to obtain initial carbonized materials
- Activation stage: The carbonized materials are exposed to water vapor, CO₂ or flue gas at high temperature (about 900℃) to develop pores through oxidation reactions
- Process optimization: Activation temperature, gas flow rate and time directly affect pore distribution. For example, extending the water vapor activation time can increase the proportion of mesopores, which is suitable for macromolecular adsorption
Chemical activation method
The chemical activation method simultaneously completes carbonization and activation in a single step by adding an activator. The main methods include:
- Zinc chloride method: The raw material is mixed with a 40% ZnCl₂ solution in a ratio of 1:1-4 and heated at 600-700℃. The dehydration of ZnCl₂ promotes aromatization to form microporous carbon with uniform pore size. Especially suitable for wood raw materials, but it is seriously corrosive to equipment and requires strict wastewater treatment
- Phosphoric acid method: phosphoric acid and raw materials are heated at 400-600℃, and activated carbon with developed mesopores is generated through catalytic dehydration and cross-linking reaction, which is suitable for dye decolorization (methylene blue adsorption value can reach 12mL/g)
- Potassium hydroxide method: KOH is used as an activator (alkali carbon ratio 1-5), and treated in nitrogen at 800℃ to produce ultra-high specific surface area (>3000m²/g) activated carbon. For example, petroleum coke reacts with 3 times KOH at 850℃, and the specific surface area of the product reaches 2600m²/g, which is particularly suitable for supercapacitor electrodes
Activator | Raw Material Ratio | Temperature Range (℃) | Duration | Specific Surface Area (m²/g) | Application Field |
Zinc Chloride | 1:0.5–4 | 600–700 | 1–2 hours | 800–1,200 | Gas-phase adsorption |
Phosphoric Acid | 1:1–3 | 400–600 | 30–90 minutes | 1,000–1,500 | Liquid-phase decolorization |
Potassium Hydroxide | 1:1–5 | 700–900 | 1–4 hours | 2,000–3,000 | Electrochemical energy storage |
Microwave Heating Method
Microwave activation is a highly efficient and energy-saving technology developed in recent years, which uses the dielectric loss of carbon materials to generate heat:
- Mix raw materials such as ash-free coal (HPC) with KOH and place them in a microwave reactor
- Activation can be completed in only 6 minutes at 2000W power and 600℃
- The product has a specific surface area of 1035m²/g, a mesoporosity of 38%, and excellent electrochemical performance (specific capacitance 277F/g in 3mol/L KOH)
Steam Activated Carbon vs. Chemically Activated Carbon: Is There a Difference?
Generally, these two different activation processes produce very similar products, but subtle differences can lead to huge differences in filtration performance. For example, steam activated carbon requires an acid wash to purify the activated carbon. Chemical activation, on the other hand, does not require an acid wash.
Steam activation typically produces activated carbon that is approximately 1 to 3 millimeters thick. This activated carbon is then crushed and screened to remove dust and other impurities and meet specific specifications.
On the other hand, activated carbon produced by chemical activation typically does not require further crushing. In fact, it may need to be made into a larger size to meet certain needs. If desired, small pieces of activated carbon can be impregnated with an activating agent to make the particles larger. In addition, chemically activated carbon can be steam activated a second time, which will give it additional properties.
Therefore, steam and chemical activation produce different products, but they can often be modified through further processing to produce similar results.
A step-by-step guide to making activated carbon
Materials and equipment
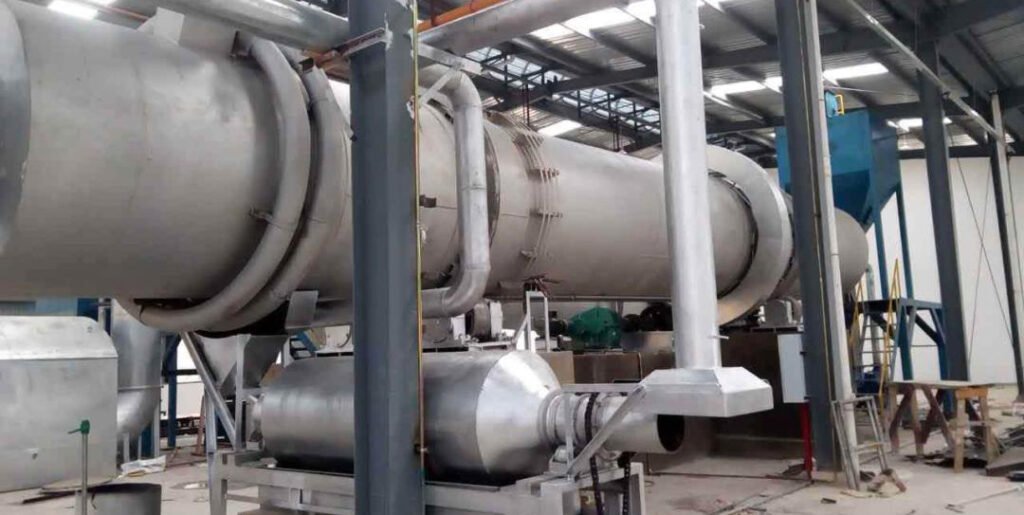
- Coconut shells, wood, bamboo, and other carbonaceous materials are commonly used to produce the charcoal base. It is essential to use high-quality natural materials to avoid harmful contaminants.
- Rotary kilns or furnaces are equipment used to heat and burn the raw materials to form charcoal. Specialized kilns or furnaces are needed to ensure a controlled combustion process and prevent the formation of ash.
- Dryers are used to dry the material before combustion to reduce the moisture content and ensure a more complete combustion.
- Using grinders or hammer mills, charcoal is crushed into a fine powder, thereby increasing its surface area and porosity.
Each material has a specific purpose in the activated carbon production process. Using natural materials and specialized roatary kilns or furnaces can ensure that the charcoal is free of harmful contaminants and has the porosity required to effectively absorb impurities. Drying the material before combustion helps to reduce the moisture content, which affects the quality of the charcoal. Finally, fine grinding of the charcoal can increase its surface area and porosity, making it more effective for a variety of applications.
Raw material preparation
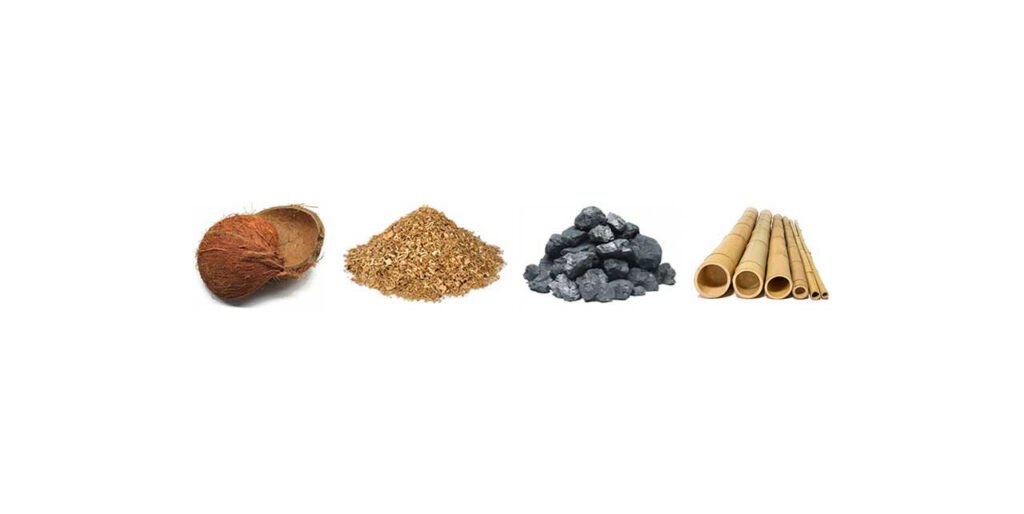
- Washing raw materials: First, we should collect raw materials such as coconut shells, wood, bamboo, coal, walnut shells, fruit cores, etc. and wash them to remove dirt, debris or other impurities.
- Drying raw materials: Second, we should dry the raw materials at low temperature. This step helps to reduce moisture, ensure more efficient combustion and improve the quality of charcoal.
- Crushing raw materials: Crush the dried raw materials into small pieces with a grinder or hammer mill. This makes it easier to burn evenly and form a uniform carbonaceous matrix.
Proper preparation of raw materials is essential to the production of high-quality activated carbon. Moisture content, impurities, and uneven combustion will affect the porosity and effectiveness of the final product. By collecting and cleaning raw materials, drying them thoroughly, and crushing them evenly, you can make a stable and effective carbon base suitable for a variety of uses.
Carbonization
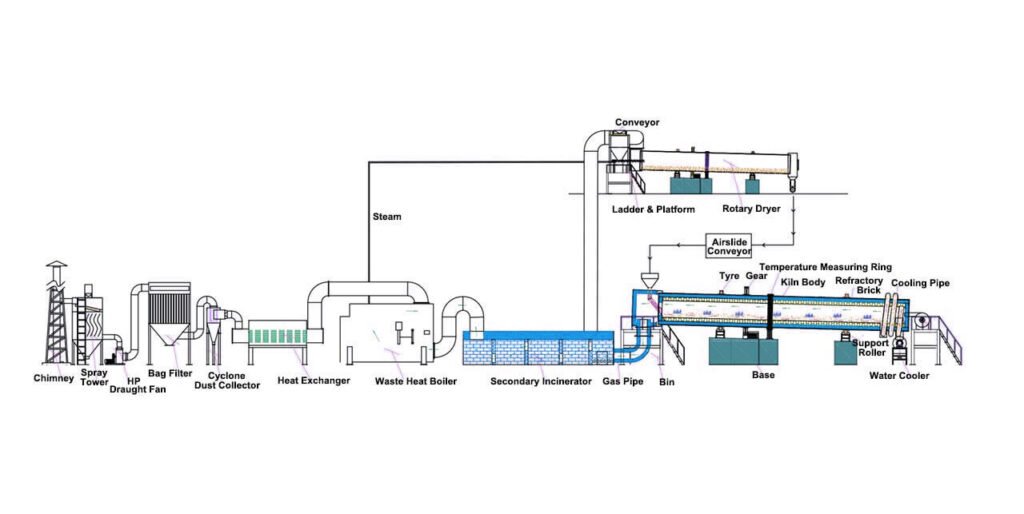
Carbonization is a critical step in the activated carbon production process. In this step, the prepared raw materials are heated in the absence of oxygen, causing them to degrade and release volatile gases, leaving behind a solid carbon base.
Carbonization methods include traditional pit carbonization, rotary drum carbonization, and others. Each method has its advantages and disadvantages, and the method chosen depends on the desired results and the available resources.
Regardless of the method used, temperature control during carbonization is critical. High temperatures will cause the charcoal to burn prematurely, reducing its effectiveness; low temperatures will result in incomplete carbonization and reduced porosity in the final product. The temperature should be maintained between 600 and 900 degrees Celsius.
The effect of temperature on the final product varies depending on the raw materials used and the intended use of the activated carbon. Higher temperatures generally produce products with higher porosity and better activated carbon, while lower temperatures produce harder and more durable products. Carbonization is a critical step in producing high-quality activated carbon and requires precise temperature control to achieve the desired results.
Activation
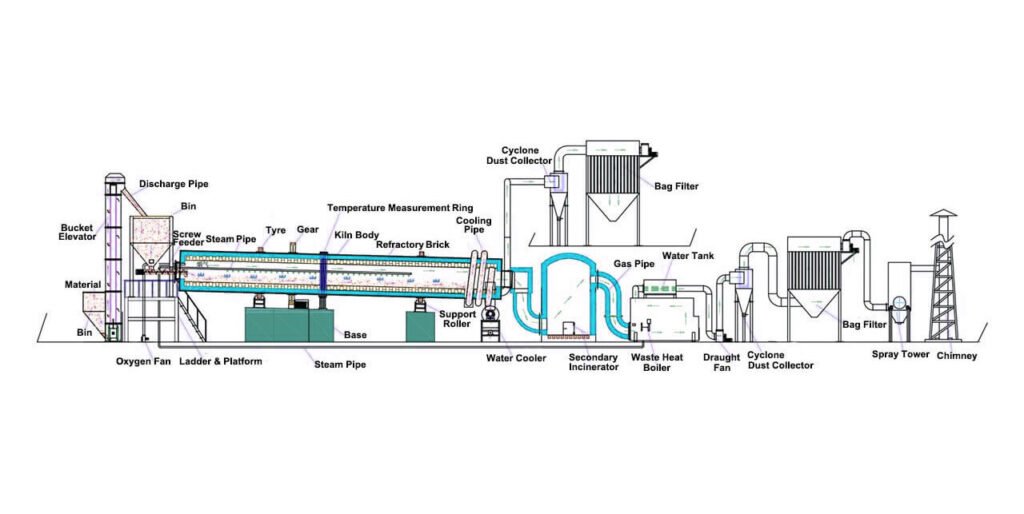
The charcoal produced after carbonization has not yet been activated. Activation is the process of exposing charcoal to a substance that creates pores and increases its surface area, making it more effective at adsorbing impurities and contaminants.
Activation methods include steam activation, chemical activation, and other methods. Each method involves exposing the charcoal to different substances and conditions, resulting in different properties and performance.
Steam activation is a common method that involves exposing the charcoal to high-temperature steam, causing it to expand and form pores. Chemical activation is the process of treating the charcoal with specific chemicals, such as phosphoric acid, to make it more porous.
Activated carbon requires activation to increase its surface area and adsorption capacity. The more porous the activated carbon, the greater its ability to adsorb impurities and contaminants from gases and liquids. Activated carbon has a wide range of applications, including air and water purification, medicine, and food processing.
Washing and Drying

After the activated carbon is made, it must be washed and dried to remove any remaining impurities and prevent mold growth.
Typically, the washing process requires soaking the activated carbon in water, draining the water, and repeating it multiple times until the water runs clear. This removes any chemicals or impurities left over from the activation process.
To avoid mold growth, activated carbon must be thoroughly dried after washing. There are various drying methods, such as sun drying and rotary dryer drying. Sun drying is a natural and economical method, but it takes several days and the activated carbon needs to be turned frequently to ensure even drying. Although dryers dry faster, they require careful temperature control to avoid overheating.
Drying is an important step in the activated carbon production process because any residual moisture can cause mold growth and reduce the activity of the activated carbon. It is important to ensure that the activated carbon is completely dry before storing or using it.
Quality Control
Activated carbon production requires quality control to ensure that the final product is effective and safe. Quality control test methods include iodine number testing and surface area analysis. The iodine number test determines the amount of iodine adsorbed by the activated carbon, which indicates its adsorption capacity. Surface area analysis determines the surface area of the activated carbon, which is an important factor in its adsorption capacity. Strict quality control measures must be taken to avoid common mistakes that can occur during the production process. One common mistake is to use low-quality raw materials, which will result in poor quality activated carbon. Another mistake is to fail to properly control the temperature during the carbonization and activation process, which can result in inconsistent product quality.
Production process guide of coconut shell activated carbon
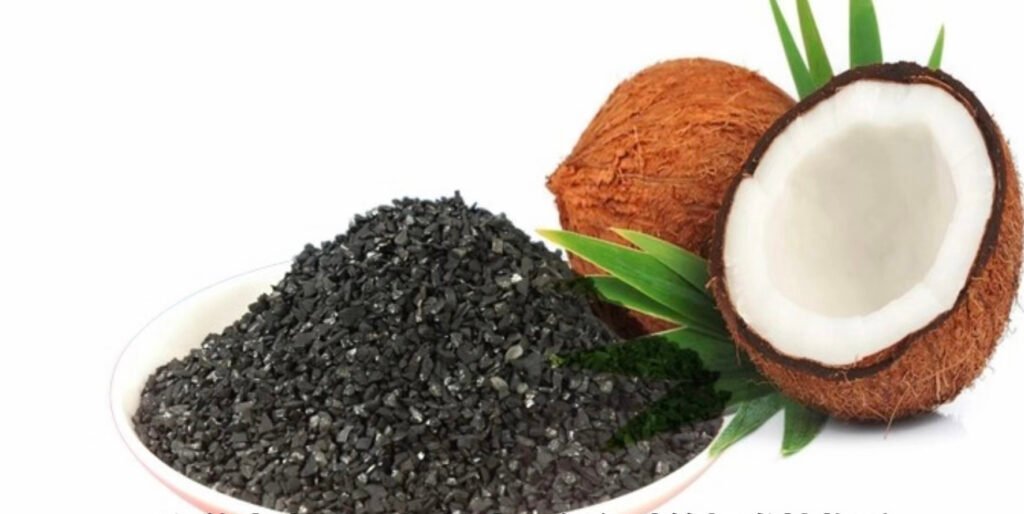
Coconut shell activated carbon is widely used in metallurgy, chemical industry, petroleum, electricity, food, drinking water, pure water, beverage, deep purification of industrial water, and turbidity reduction of precious metal refining liquid. Among them, the molecular sieve zeolite with better effect is well received by users. Coconut shell activated carbon is currently the main product of deep processing of coconut shell. Coconut shell is made into coconut shell charcoal after burning, and then activated to make coconut shell activated carbon. 1 ton of coconut shell can process about 300 kg of coconut shell charcoal, and then extract about 120 kg of coconut shell activated carbon. Coconut shell activated carbon factory is a good way to convert biomass into economic benefits and protect the environment. There are currently four main types of coconut shell activated carbon, including granular activated carbon, columnar activated carbon, powdered activated carbon, and honeycomb activated carbon.
Coconut shell activated carbon production process
There are several processes for making activated carbon with coconut shells. Let's take physical activation as an example. Physical activation refers to one of the methods of producing activated carbon under high temperature conditions using air steam mixed gas, water vapor or other gases as activators and special furnace types. The activated carbon produced by this method has the advantages of developed pore structure, large specific surface area, strong adsorption performance, high mechanical strength, small fluid resistance, stable chemical properties, high purity and easy regeneration.
Step 1: Raw material preparation
First, we screen the coconut shell. There are two main raw materials for coconut shell activated carbon on the market, one is Hainan coconut shell and the other is Indonesian coconut shell. Hainan coconut shell is relatively thin and has low density, while Indonesian coconut shell is relatively thick and has a higher density. In comparison, the quality of activated carbon processed from Indonesian coconut shell is better. After the raw materials are screened, the coconut shell needs to be pre-treated by drying, crushing, screening, etc. before entering the next step.
Step 2: Carbonization
Put the screened coconut shell into the carbonization equipment and dry the raw materials at a temperature of 170-600℃ to carbonize 80% of the organic tissue. After the high temperature is burned to a certain degree, the charcoal kiln is closed to allow air to enter, and then the waste heat is used to continue heating and distilling, so that the moisture and wood tar in the coconut shell are leached out, that is, coconut shell activated carbon is formed.
Step 3: Activation
Put the carbonized coconut shell into the activation rotary kiln and use water vapor, flue gas (mainly CO2) and other oxygen-containing gases as activators. Contact with carbon at high temperature and activate through redox reaction. The main operating conditions of the activation process include activation temperature, activation time, flow rate and temperature of the activator, feeding speed, oxygen content in the activation furnace, etc.
Step 4: Grinding and screening
After activation, the finished coconut shell activated carbon can be obtained. Sometimes customers have special requirements for size, then we need to send coconut shell activated carbon to the grinding machine (Raymond mill). The finished activated carbon will be screened according to the customer's particle size requirements. Common coconut shell activated carbon particle sizes are 6-12 mesh, 8-16 mesh, 10-24 mesh, 20-40 mesh, 200 mesh, 325 mesh, etc.
Step 5: Pickling, washing and drying (optional step)
This process is an optional process in the production process of coconut shell activated carbon. According to the process requirements, some finished activated carbon needs to be pickled to remove impurities. The pickling agent can be 5% hydrochloric acid, placed in a special pickling tank, heated and boiled, and the waste acid is discharged. The washing process is used to remove acidic substances in the material, and the pH value is generally controlled at 5-7. The washed material needs to be dried until the moisture content reaches 10% (or customized by the customer).
Step 6: Packaging
The final packaging specification of coconut shell activated carbon is generally 25kg/bag or ton bag. The packaging bag uses a double-layer woven bag, which is strong and moisture-proof.
Item | Range / Specification |
Material | Inlet flue gas temperature |
Induced Draft Fan | Power: 40 kW; Airflow: 35,000 m³/h; Air Pressure: 2590 Pa |
Raw Material | Moisture < 15%; Particle size: 1–20 cm; Ash content < 3% |
Feeding Method | Bucket elevator or screw feeder |
Final Carbonized Product | Moisture < 1%; Ash < 5%; Volatile content: 15–18%; Size: 1–10 cm; Iodine value: 120–200 mg/g |
Carbonization Condition | Oxygen-limited carbonization |
Gas Composition | Water, carbon dioxide, hydrocarbons |
Discharge Temperature | 350–400 ℃ |
Powder Collection | Cyclone collector, bag filter, spray system |
Post-cooling Temperature | < 50 ℃ |
Cooling Method | Rotary kiln natural cooling pipe, external water bath |
Power Consumption | < 100 kW |
Equipment Material | Q345 steel |
Steam Generation | 1.5–3 tons/hour |
Refractory Material | Steel fiber reinforced castable, high alumina bricks |
Steam Pressure | 5 kgf/cm² |
Insulation Thickness | > 40 cm |
Steam Flow Rate | 1.6–2.3 tons/hour |
Refractory Alumina Content | > 45% |
Inlet Flue Gas Temperature | 600–800 ℃ |
High-temp Material Resistance | > 1300 ℃ |
Furnace Temperature | < 660 ℃ |
Gas Volume | 15,000 m³/h |
Flue Gas Incinerator Temperature | 800–960 ℃ |
Temperature Sensors (Thermocouples) | Units: 6; Heat resistance: 1200 ℃ |
Guide to the chemical production process of wood activated carbon
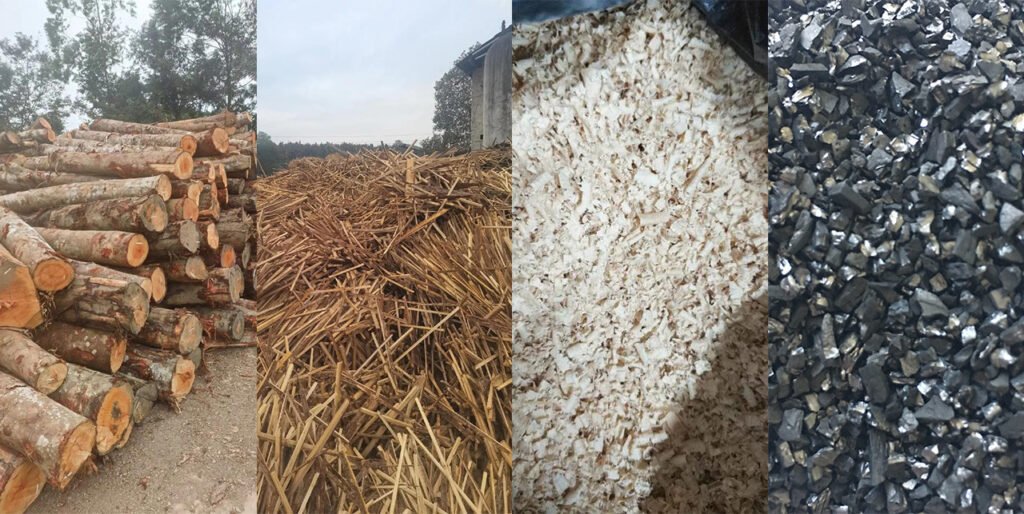
Chemical activation of wood activated carbon by phosphoric acid method
Preparation of raw and auxiliary materials
The main raw material for producing activated carbon by phosphoric acid method is sawdust, among which coniferous wood sawdust is better than hardwood wood sawdust, and fir wood sawdust is better than pine wood sawdust. Fresh pine wood sawdust contains more rosin, which has an obstructive effect on the penetration of phosphoric acid molecules. Therefore, if pine wood sawdust is stored for a period of time, the volatile components of rosin in it will naturally volatilize, decompose and oxidize before being used, which is more conducive to the production of activated carbon.
Item | Process Requirements |
Type | Cedar sawdust, pine sawdust, various mixed wood sawdust |
Particle Size | 0.425–3.35 mm |
Purity | Free from bark, wood chunks, soil, sand, iron scraps, etc. |
Moisture Content | Relative moisture content: 15%–20% |
Production process flow
The process flow of continuous production of powdered activated carbon by phosphoric acid method involves several key steps. The whole process usually includes sawdust screening, sawdust drying, phosphoric acid solution preparation, raw material and phosphoric acid mixing (or impregnation), carbonization activation, phosphoric acid recovery, rinsing (including acid treatment and water washing), centrifugal dehydration, drying and grinding. In addition, there is a special tail gas treatment system for recovering phosphoric acid and sulfuric acid in flue gas to minimize pollution to the environment. In order to ensure that the operation of each link can be carried out stably and efficiently, the control of key parameters is crucial. The following are the key parameters of each process step and main operation:
Process Step | Main Operation | Key Parameters |
Impregnation | Mixing raw materials with phosphoric acid | H₃PO₄ concentration: 40–60%, soaking time: 12–24 hours |
Carbonization & Activation | High-temperature carbonization and activation | Temperature: 400–600 ℃, duration: 2–3 hours |
Cooling & Washing | Cooling to room temperature and washing with hot water | Wash water temperature: 80–90 ℃, wash cycles: 3–5 times |
Production process operation
Screening and drying of sawdust
In order to ensure the quality of the final product and the stability of the process operation, the sawdust needs to be strictly screened and dried. Usually, a vibrating screen or a drum screen is used to screen the sawdust, and sawdust particles with a particle size between 0.425 and 3.35 mm are selected.
Sawdust within this particle size range is conducive to the smooth progress of subsequent processes and can effectively improve the quality of activated carbon. During the screening process, impurities such as plate skin, iron filings, soil, sand, and stones need to be removed to prevent these impurities from clogging in the subsequent impregnation and rinsing processes, increasing the equipment load, and thus affecting product quality.
Preparation of phosphoric acid solution
The preparation of phosphoric acid solution is one of the key links that affect the process and product quality. The concentration of phosphoric acid solution and whether the preparation meets the process requirements are directly related to the ratio of raw materials and phosphoric acid.
This has an important impact on the performance of the final product. Usually, a high-concentration industrial phosphoric acid solution of 85% (mass fraction) is used, and water is added to dilute it to the required concentration according to the process requirements to achieve the Baume degree specified in the process.
The Baume degree of phosphoric acid solution is closely related to temperature. When the mass fraction of phosphoric acid solution is constant, the Baume degree of the solution will decrease accordingly as the temperature increases. Therefore, during the operation, in order to ensure that the Baume degree of the solution meets the process requirements, the temperature of the solution must be indicated.
Understand the relationship between the Baume degree, density and mass fraction of phosphoric acid solution, as well as the corresponding values of these parameters at different temperatures, to ensure that the operator can accurately control the characteristics of the solution.
Mixing (or impregnation)
The main purpose of mixing is to fully stir and knead the sawdust and phosphoric acid solution, so that the two are evenly mixed, and to accelerate the penetration of phosphoric acid molecules into the biological tissue of the sawdust. The process is usually carried out in a mixer, which is made of acid-resistant steel, has a semicircular trough shape, and is equipped with a pair of serrated stirrers inside. The design of the stirrer ensures that the sawdust and phosphoric acid solution are fully contacted during the mixing process to achieve a uniform impregnation effect.
In addition to using a mixer, other equipment can also achieve similar impregnation purposes. For example, equipment such as twin-screw drills and rotary kilns can also achieve ideal mixing and impregnation effects under specific conditions. The selection of these equipment is usually adjusted according to specific process requirements and production scale.
Carbon activation process
The activation of carbon is one of the key steps in the preparation of activated carbon, and the quality of activation directly affects the performance of the final product. The activation of carbon is usually carried out in a rotary kiln, which is mainly divided into two types: internal heating and external heating. Japan mostly uses external heating rotary kilns, and China generally uses internal heating rotary kilns.
The main difference between internal heating rotary kilns and external heating rotary kilns is the contact method between the heat source and the material. In the external heating rotary kiln, the high-temperature airflow does not directly contact the material, but heats the material through the radiant heat of the furnace wall. This heating method has more uniform heat transfer, which is beneficial to improving product quality, but it has higher requirements on the heat resistance and corrosion resistance of the rotary kiln material. The internal heating rotary kiln directly heats the material through the high-temperature flue gas flow, so that the material is quickly heated and activated.
Phosphoric acid recovery
During the activation process, phosphoric acid and phosphoric acid polymers (such as pyrophosphoric acid, metaphosphoric acid, etc.) generated under high temperature conditions will remain in the activated carbon in large quantities. According to measurements, the content of these substances can be as high as about 75%, so recycling these substances is crucial to reducing "acid consumption". At the same time, the process also requires post-treatment of the activated carbon to remove these phosphoric acid polymers and other impurities. The recovery operation of phosphoric acid is essentially an extraction process. Through specific operating conditions, phosphoric acid and its polymers are separated from the activated carbon and recycled. Phosphoric acid is a non-volatile acid. When heated to 200~300℃, a dehydration reaction occurs to generate pyrophosphoric acid. The reaction formula is as follows:
2H 3 PO 4 → H₄P₂O₇ + H₂O (pyrophosphoric acid)
When the temperature is further increased to above 300°C, phosphoric acid loses water and is converted into tripolyphosphoric acid:
3H3PO4 → H5P3O10 + 2H₂O (tripolyphosphoric acid)
If the temperature reaches incandescent, phosphoric acid loses water and becomes polymetaphosphoric acid:
4H 3 PO 4 → (HPO 3 )4 + 4H2O (polymetaphosphoric acid)
Polymetaphosphoric acid will not decompose at high temperatures, but will only sublimate. Whether it is pyrophosphoric acid, tripolyphosphoric acid or polymetaphosphoric acid, it will be converted into orthophosphoric acid in water. In the preparation of activated carbon, due to the low activation temperature (usually between 450 and 500°C), phosphoric acid will not volatilize and will only exist in the form of pyrophosphoric acid, tripolyphosphoric acid or polymetaphosphoric acid. This means that during the activation process, phosphoric acid remains stable and no volatilization loss occurs.
Therefore, the recycling operation usually adds phosphoric acid solutions of different concentrations into the recycling barrel containing the activated material, and separates the residual phosphoric acid and phosphoric acid polymer by adjusting the solution concentration and soaking time. The recovered phosphoric acid solution can be reused in the impregnation activation process after treatment, which effectively reduces the acid consumption in the production process and improves resource utilization.
The phosphoric acid method is mainly used to prepare wood activated carbon, especially powdered activated carbon, which is widely used in food decolorization, fish protein purification, marine collagen decolorization, sugar, glucose, edible oil, vegetable oil, engine oil, and sewage decolorization and purification.
Conclusion
The production of activated carbon is a complex process such as raw material preparation, carbonization, activation, washing, drying, and quality control. Each step is critical so don't do it at home. The correct procedures must be followed to ensure that the activated carbon reaches the best quality, by following steps can produce high-quality activated carbon.