
In this article we are going to explore what is a fluid bed dryer. Fluidized bed dryers are used to dry solid particles, including granules and powders. In this machine, hot air is blown through a bed of particles, causing the particles to float and mix freely. This looks like a flowing liquid, hence the name "fluidized bed". It is an efficient device that uses fluidization technology to achieve rapid drying of materials and is widely used in industries such as chemicals, pharmaceuticals, food, and ceramics. Regardless of the industry, efficient drying of bulk solids is an important aspect of modern industrial processing. Among the many available technologies, fluidized bed dryers have proven to be not only versatile and reliable, but also capable of handling a wide range of materials.
What is the Working Principle of Fluidized Bed Dryer?

Fluidized bed dryers rely on the fluidization of solids to effectively dry materials.Fluidization, where the material behaves as a liquid and remains suspended, is achieved by finding the right balance between the upward airflow and the weight of the particles. This is accomplished by passing air through a permeable bed of solids formed by a porous plate at the bottom of the drying vessel.Unlike static dryers, fluidized bed dryers have a greatly increased surface area of material exposed to the airflow. This also promotes mixing of the solids, further improving heat transfer and making this industrial dryer extremely thermally efficient.
Fluidized state
Fluid bed dryer manufacturers can use different fluidization patterns to customize the dryer according to the characteristics of the material and achieve the desired drying goals. The type of fluidization pattern depends on the air flow velocity.
How Material Properties Affect Fluid Bed Drying
As with any industrial dryer, the characteristics of the material being dried can greatly affect the drying process in a fluid bed dryer. The following material characteristics must be carefully considered. In each case, the uniformity of the feedstock should be given priority for best results.
Particle size and shape
Fluid bed dryers are suitable for processing a wide range of materials, from granules and pellets to crystals and powders, but particle size and shape can affect the drying process. This is most evident in terms of residence time and airflow velocity.The smaller the particles, the shorter the drying time will generally be, but it will also depend on how the material retains moisture (on the surface or in the core). However, it may be necessary to reduce airflow velocity to avoid “blowing” the material into the exhaust system.Irregularly shaped particles are more difficult to dry than uniform particles due to their lack of consistency. Therefore, some materials, such as manure, may require intensive pre-treatment before drying to provide a uniform feed to the dryer.
Moisture content
- High moisture materials generally take longer to dry, but again, this depends on how the material carries moisture.
- Moisture content also affects the “minimum fluidization velocity,” which is the minimum velocity required to suspend and support the weight of the particles—in other words, the minimum velocity required to achieve fluidization.
- As a result, materials with particularly high moisture content may require additional pre-treatment, such as back-mixing, to provide a feedstock suitable for fluidization.
Specific Heat
The specific heat of the material, the amount of heat required to raise the material's temperature by one degree, is another important consideration. Heat-sensitive materials require tight temperature control throughout the drying process to avoid overheating and subsequent degradation.
What are the Types of Fluid Bed Dryers?
Fluid bed dryers can be classified into different types based on their design and working principle. However, it is important to note that fluid bed dryers can be modified and hybrid designed to suit specific applications and requirements. The most suitable type depends on factors such as the material to be dried, the required drying quality, energy efficiency and process control requirements.
The main types of fluid bed dryers include:
Conventional fluidized bed dryer

Conventional fluidized bed dryers are simple in design and are widely used in a wide range of industries. They consist of a porous bed or plate that holds the material to be dried. When heated air is passed through the bottom of the bed, the material particles become fluidized. The fluidized particles then undergo efficient heat and mass transfer, resulting in water evaporation and drying. Conventional fluidized bed dryers are flexible and can be used in a variety of applications.
Vibrating fluidized bed dryer

Vibrating fluid bed dryers use an additional vibration mechanism to improve fluidization. These dryers use vibration to promote movement of larger particles or sticky wet agglomerates that cannot be fluidized by air alone. Vibration can also be used to reduce the fluidization velocity of materials with a wide particle size distribution, allowing the larger particles to be agitated by vibration while the finer materials are agitated by the fluidizing air. This will minimize the loss of fines with the exhaust air. Dedert's Vibrating Fluid Bed Dryers (VFB) use an unbalanced vibrating motor to achieve vibration and mount the fluidized bed unit on air springs to isolate it from the supporting structure.
Stirred fluidized bed dryer

Agitated fluid bed dryers combine a fluidized bed with mechanical agitation to improve drying efficiency. Within the bed, a stirrer or agitator continuously agitates the particles. This agitation action improves heat and mass transfer, resulting in faster drying. Agitated fluid bed dryers are ideal for drying materials that have poor fluidization or high moisture content, as well as for uniformly drying sticky materials.
What are the Applications of fluidized bed dryer?
Fluid bed dryers are becoming increasingly popular across industries due to their versatility, efficiency and high drying capacity. These dryers have a wide range of applications in the agricultural sector, pharmaceuticals, food processing and mineral processing. Let’s explore the many applications of fluid bed dryers.
Pharmaceuticals
Fluid bed dryers play an important role in the pharmaceutical industry, where precise drying of pharmaceutical powders, granules and tablets is critical. In fact, it is by far the most widely used dryer in the pharmaceutical industry. Key applications include:
Process | Description |
Drying of Active Pharmaceutical Ingredients (API) | FBD ensures uniform and slow drying of APIs, maintaining consistent potency and quality. |
Granule Drying | After wet granulation, FBD is used to dry the granules, ensuring proper particle size distribution and moisture content. |
Tablet Drying | FBD effectively removes moisture from tablets without damaging their structural integrity after coating or during humidity-sensitive processes. |
Chemical
As in the pharmaceutical industry, fluid bed dryers are widely used in the chemical industry to dry a variety of compounds. Some common uses include:
Process | Description |
Chemical Powder Drying | FBD effectively dries various chemical powders, including dyes, pigments, catalysts, and specialty chemicals. |
Polymer Drying | In the polymer processing industry, FBD is used to remove moisture and solvents from polymer granules, ensuring consistent quality and performance. |
Chemical Reaction Drying | In certain chemical reactions, FBD is used to remove water or other by-products, helping to drive the reaction to completion. |
Food processing industry
Correct drying of food is essential to maintaining its quality and shelf life. This is where fluid bed dryers come into play in the food processing industry.
Process | Description |
Grain Drying | FBD is used to remove moisture from grains, cereals, and seeds to enhance product stability and prevent spoilage. |
Coffee Bean Drying | During processing, coffee beans require gentle and uniform drying to preserve their flavor and aroma. FBD can be configured to achieve this. |
Fruit and Vegetable Drying | FBD is used to remove moisture from fruits and vegetables before further processing or packaging, thereby extending shelf life. |
Minerals and Aggregates
Fluidized bed dryers are also used in the mineral aggregates industry for drying and deagglomerating materials. Key applications include:
Process | Description |
Drying of Minerals and Ores | FBD can effectively remove moisture from minerals and aggregates, enhancing their handling and processing performance. |
De-agglomeration | In industries requiring particle size reduction of aggregates, fluid bed dryers offer effective de-agglomeration through gentle drying and controlled airflow. |
Other Industries
Fluid bed dryers are also used in many other industries:
Process | Description |
Biomass Drying | Moisture removal is crucial for efficient combustion of biomass fuels. FBD is used in the production of biomass fuel. |
Recycling and Waste Management | FBD aids in drying and processing various waste materials, enabling their conversion into usable products or fuel sources. |
Key Factors to Consider When Selecting a Fluid Bed Dryer & manufacturers:

Selecting the right fluid bed dryer is critical to optimizing the drying process and achieving desired results across a wide range of industries. With so many options available, it is important to consider a variety of factors to ensure the dryer you choose will meet your specific requirements.
Material properties
- Particle size and shape: The size and shape of the particles affect fluidization behavior and drying dynamics. To ensure efficient fluidization and drying, the dryer must be able to adapt to the specific particle characteristics.
- Moisture content: The initial moisture content affects the drying time and drying factor. It is essential to select a fluid bed dryer that can successfully remove the required moisture within the specified time.
- Thermal sensitivity: Some materials are susceptible to high temperatures and must be dried at lower temperatures to avoid deterioration. In this case, it is essential to select a fluid bed dryer with precise temperature control.
Capacity and throughput
- Drying capacity: Determine the required drying capacity based on the weight or volume of material processed per unit time. Make sure the selected dryer can meet your production needs without compromising drying efficiency.
- Residence time: The time required for complete drying varies depending on the material. Choose a fluid bed dryer with sufficient residence time to allow for proper moisture removal and avoid the risk of over-drying or under-drying.
Heating method
- Energy Efficiency: Evaluate the heating method for its energy efficiency and its compatibility with existing energy sources. Select a heating method that strikes a balance between energy use and drying efficiency.
- Temperature Control: Evaluate the heating method for its ability to precisely control temperature. Temperature regulation is critical to maintaining product quality and avoiding overheating or underheating.
Process control and automation
- Control systems: Analyze the control system’s ability to monitor and adjust drying parameters such as temperature, airflow rate, and humidity. Look for a wide range of control options as well as an easy-to-use interface.
- Automation capabilities: Consider automation possibilities such as programmed recipes, data logging, and remote monitoring. Automation can improve process control, reduce human error, and streamline processes.
Equipment design and cleanliness
- Materials of Construction: Make sure the materials used in the dryer’s construction are fit for purpose, such as stainless steel for the pharmaceutical or food processing industries.
- Accessibility and Maintenance: Look at the ease of cleaning and maintenance. Look for features that make cleaning easier and faster, such as removable parts and easy-to-clean surfaces.
- Air Handling System: To ensure product quality and limit contamination issues, consider the design of the air handling system, including filtration and exhaust systems.
- Manufacturer experience: Choosing a reliable supplier for a fluid bed dryer because it directly affects the performance, efficiency, and longevity of the equipment. A good supplier provides not only high-quality, durable machinery but also ensures proper customization to meet specific processing needs. They offer technical support, spare parts availability, and after-sales service, which are essential for minimizing downtime and ensuring smooth operation. Additionally, a reputable supplier like tongli have a proven track record, comply with industry standards, and provide clear documentation and training, helping buyers make a safe and cost-effective investment in a critical piece of production equipment.
Security and Compliance
- Make sure the selected fluid bed dryer meets the relevant safety standards and regulatory requirements. Aspects such as explosion-proof design, proper grounding, and compliance with industry-specific regulations need to be considered.
Advantages and Disadvantages of Fluid Bed Dryers
Fluid bed dryers are a flexible and popular method of drying bulk solids and are often the first choice in industrial drying system selection. Like any industrial dryer, fluid bed dryers have inherent advantages and disadvantages that make them more suitable for certain applications than other dryers. Here are the main advantages and disadvantages of these industrial dryers.
Advantages of Fluidized Bed Dryer
Fluid bed dryers are the preferred drying method for many applications due to their many advantages. These include:
Small Footprint
Fluidized bed dryers are significantly smaller than some other drying technologies, yet still offer commercial production capacity. This makes them well suited for facilities with lower throughput requirements and limited space.
Efficient Drying
Fluidized bed dryers have high heat transfer rates due to their fluidization technology, making them an efficient choice; fluidization allows air to surround each particle.
Gentle Handling
Fluidized bed dryers offer gentler material handling than some other drying technologies.
Low Cost
Perhaps one of the most common reasons for choosing a fluidized bed dryer is its relatively low cost. In addition to its low capital cost, its small size also makes it more cost-effective to ship. Installation costs are also low.
Flexible Applications
Fluidized bed dryers are able to effectively dry a wide range of bulk solids for a wide range of processes, industries, and materials.
Solids Mixing (CSTR)
Fluidized bed dryers are considered continuous stirred tank reactors (CSTRs) because fluidization promotes thorough mixing of solids.
Simple Manufacturing
While some industrial drying systems require extensive machining and extremely precise fabrication and welding, fluidized bed dryers are much simpler. With no rotating parts and varying loads, fluid bed dryers are not subject to as many forces during operation, so there is less need for heavy and delicate construction.
This is not to say that fluid bed dryers are poorly constructed; like any industrial dryer, they require attention to detail in both design and construction to provide an efficient, reliable solution.
Easily automated
Fluid bed dryers are particularly easy to automate. Additionally, with no moving parts, pressure sensors and temperature probes can be easily integrated to collect process data.
Disadvantages of Fluid Bed Dryer
While fluid bed dryers offer many advantages, they also have some disadvantages. The most obvious are:
No Energy Savings
Because a certain air velocity is required to achieve minimal fluidization, fluid bed dryers cannot be run at lower speeds as other types of dryers can when capacity is reduced. Therefore, even if a fluid bed dryer is run at a lower capacity, no electrical energy is saved.
Requirement for Homogeneous Feedstock
Fluid bed dryers also require very uniform feedstock. Any fluctuations in particle size, moisture content, or bulk density can present problems, so tight control of feedstock quality is critical. This often means implementing one or more pretreatment methods to ensure uniformity.
Product Abrasion and Dust Emissions
While fluid bed dryers are generally gentler on materials, in some cases materials may be abraded and dust generated during fluidization, which may require additional dust and air quality control measures. This may also make fluid beds inappropriate in certain environments. It is recommended to work with an expert to determine if these issues apply to a specific drying project.
Fluid Bed Dryer Frequently asked question FAQs
Fluid bed dryers work by pneumatically suspending solid particles in an air stream. This design maximizes gas-solid contact.
The dryer consists of a stationary container with a perforated plate at the bottom through which air is passed at the velocity required to achieve minimum fluidization of the solids (not to exceed terminal velocity).
It is important to note that variations of traditional fluid bed dryers, such as vibrating fluid beds, while based on fluid bed technology, are not true fluid beds because they use mechanical assistance to move the particles through the unit.
Fluid bed dryers are capable of processing a wide range of materials and are widely used in drying minerals, chemicals, metals, and biomass-derived feeds.
Large particle materials (usually larger than ½ – 1 inch) are generally better suited to rotary dryers. This is also true for materials with varying feed characteristics.
While fluid bed dryers can be used to process a wide variety of materials, they are generally best suited for materials with consistent particle size and density.
Fluid bed dryer testing is also offered at our Innovation Center to help producers evaluate whether fluid bed technology fits their specific process and product goals and establish data critical for scale-up and equipment design.
Fluid bed dryers range in size from a moderately sized pilot unit to large systems with processing capacities exceeding 100 TPH.
Because fluid bed dryers have no moving parts, maintenance requirements are minimal. The main maintenance for fluid beds is related to auxiliary equipment, such as fans and combustion systems.
Fluid bed dryers that process abrasive materials, such as sand, may also require additional maintenance on the unit itself to account for abrasive wear.
As with the design of any industrial drying system, manufacturers need multiple data points around raw materials and process goals. These include:
Starting feed moisture content
Desired outlet moisture content
Maximum material temperature
Chemical composition
Particle size distribution
Rheological properties (i.e. particle shape, is the material viscous, etc.)
Required throughput
Bulk density
Specific heat
During the design process, several process variables can be modified to meet process and product objectives. These include:
Air flow rate (and subsequently fluidization regime)
Bed distributor plate configuration
Filling percentage
Feed and product flow rates
System pressure
Residence time
Temperature profile
Additional modifications to the dryer configuration
Future Trends: Intelligent and Green Development
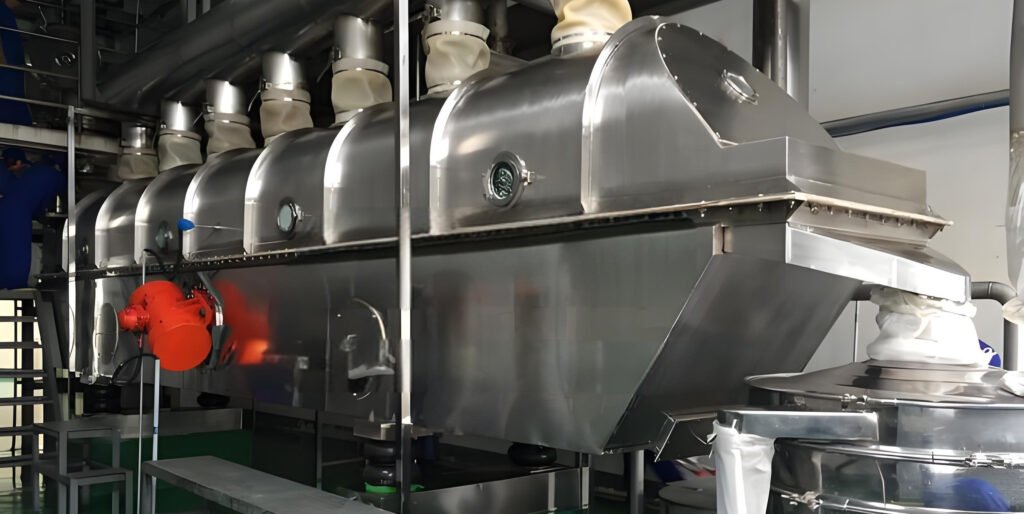
With technological advancement, fluidized bed dryers are upgrading in the following directions:
- Intelligent control: Real-time monitoring of temperature and humidity through sensors, optimization of operating parameters, and improvement of automation level.
- Energy-saving design: The application of technologies such as waste heat recovery and multi-stage drying further reduces energy consumption.
- Multifunctional integration: Integrated equipment for drying, cooling, and granulation to meet complex process requirements.
Conclusion
In this article we have discussed the working principle and application of fluidized bed dryers TONGLI Fluidized bed dryers are reliable, and can achieve efficient and high-quality drying in fertilizer industry, ensuring optimal product quality and high thermal efficiency. If you have any inqury please send us and we are glad to offer professional proposal.