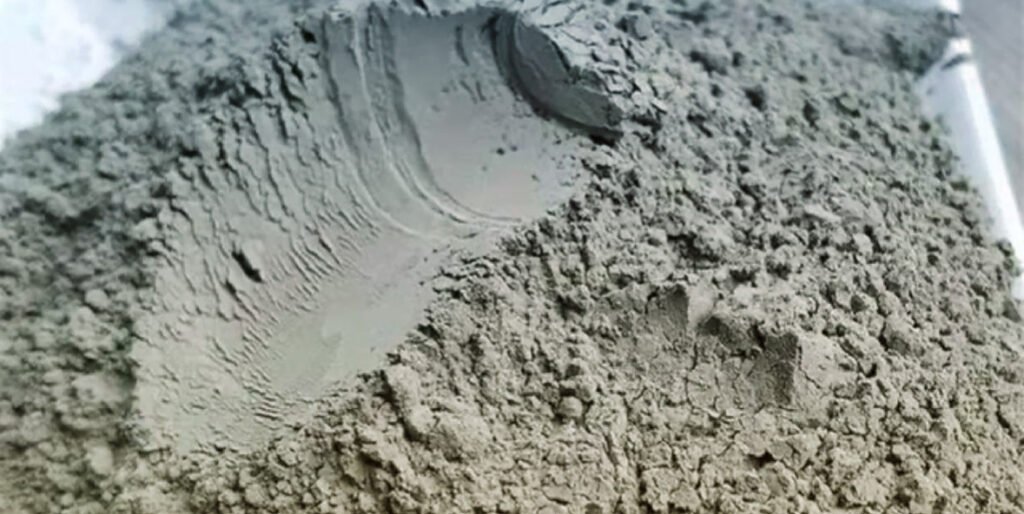
Sulfate resistant cement is a Portland cement with less than 5% tricalcium aluminate (C3A) and less than 25% (2C 3A +C4AF), which reduces the formation of sulfates. The reduction in sulfates reduces the susceptibility of concrete to sulfate attack. Sulfate resistant cement (SRC) is essential in construction. These factors weaken concrete over time. Therefore, it is crucial to use the right material, which is a hydraulic cementing material with resistance to sulfate ion attack. It is made by fine grinding of Portland cement clinker, appropriate amount of gypsum and blast furnace slag. Compared with other Portland cements, SRC cement has the characteristics of strong resistance to sulfate attack, strong frost resistance and low hydration heat. Sulfate resistant cement has lower content of tricalcium aluminate and tetracalcium aluminoferrate and higher content of tricalcium silicate. This structure can reduce the formation of sulfates, thereby improving the sulfate attack resistance of concrete stone and enhancing its durability in most corrosive environments. It is suitable for seaport projects, water conservancy projects and underground projects that are susceptible to sulfate attack, freeze-thaw and dry-wet cycles. Sulfate-resistant cement is used when construction is carried out in corrosive environments containing chemicals such as sulfates. The first criteria for cement to perform in harsh environments is that it must be well compacted, dense, and properly cured. This article will discuss the composition, properties, characteristics, uses, advantages and disadvantages of sulfate-resistant cement.
What is Sulphate Resistant Cement?
Sulphate resistant cement is a special type of Portland cement in which the tricalcium aluminate content is deliberately limited to less than 5% and the sulphate resistant cement (AF) content is controlled to less than 25%. This deliberate reduction in the amount of tricalcium aluminate minimises the formation of sulphates, which reduces the risk of sulphate attack on the concrete. Sulphate resistant cement (SRC) is more durable than ordinary cement. Ordinary cement breaks down rapidly in contact with corrosive sulphates, causing cracks and damage. SRC contains small amounts of tricalcium aluminate (C3A), a compound that reacts with sulphates, significantly increasing its strength and durability.
According to BS EN 197-1:2011, there are three main types of sulphate resistant cement:
1.Sulfate resistant Portland cement
Type | C₃A Content in Clinker |
CEM I-SR 0 | 0% |
CEM I-SR 3 | ≤ 3% |
CEM I-SR 5 | ≤ 5% |
2.Sulfate resistant blast furnace slag cement
Type | C₃A Content in Clinker |
CEM III/B-SR | Not specified |
CEM III/C-SR | Not specified |
3.Sulfate-resistant pozzolanic cement
Type | C₃A Content in Clinker |
CEM IV/A-SR | ≤ 9% |
CEM IV/B-SR | ≤ 9% |
What are sulfates?
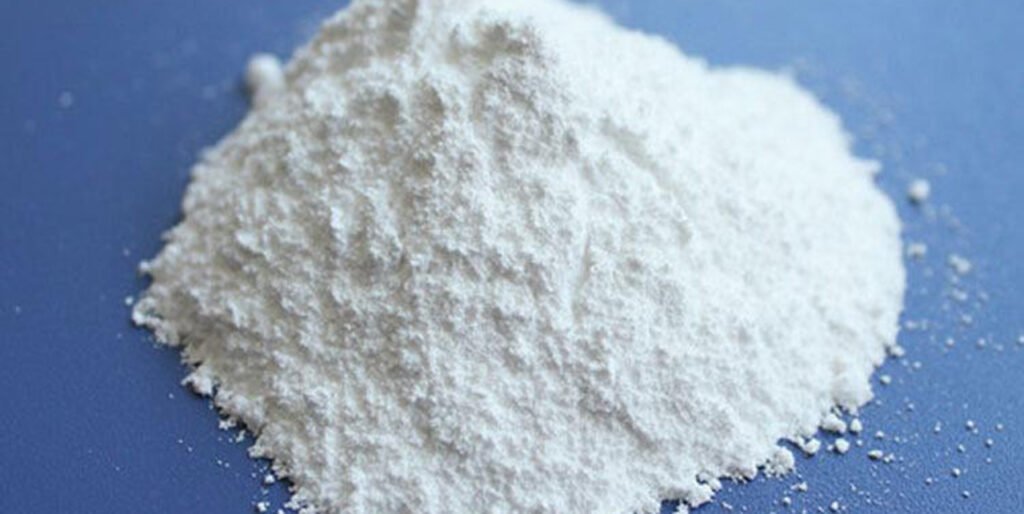
Sulfates are naturally occurring compounds found in soil and groundwater, especially in areas close to the sea, industrial areas or with sewage systems.
Why is sulfate attack resistance so important?
When concrete is exposed to sulfates, a chemical reaction occurs that causes expansion, cracking and ultimately structural damage to the concrete.How does SRC work? SRC has a lower content of tricalcium aluminate (C3A) than standard Portland cement. C3A is a component of cement that is particularly susceptible to sulfate attack. By reducing the C3A content, SRC minimizes the likelihood of this destructive reaction.
Composition of sulfate-resistant cement
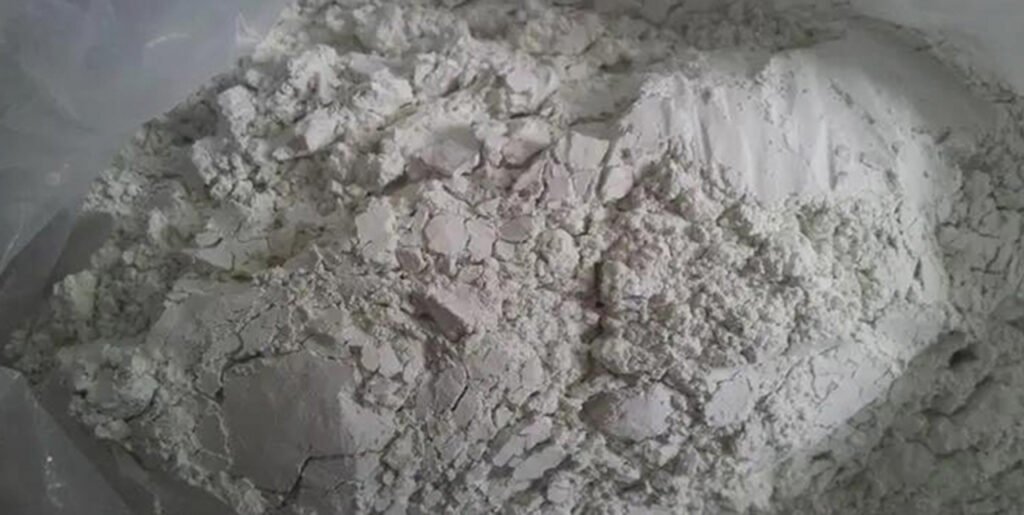
Sulfate resistant cement has a low tricalcium aluminate content. This limits the formation of calcium sulfoaluminates from the reaction of calcium sulfoaluminates with sulfates. Limiting the formation of expansive sulfoaluminates helps to increase resistance to sulfate damage during construction. The use of sulfate resistant cement effectively reduces the risk of expansive reactions and related concrete deterioration. The composition of sulfate resistant cement is key to its effectiveness. The main ingredients are as follows:
- Cement clinker: It is the main ingredient. It is made by heating limestone and clay in a kiln. For SRC, less C3A is added to the clinker. This makes it more resistant to sulfate attack.
- Gypsum: It is added during the grinding process. It controls how fast the cement sets and hardens.
- Supplementary cementitious materials (SCM): SCMs are extra materials added to cement. They enhance the properties of cement. Examples are fly ash and slag. They make cement stronger and more durable.
- Other additives: Sometimes other materials are added to improve the sulfate resistance of sulfate resistant cement. These materials are designed to improve the performance and properties of cement, such as workability and strength.
Sulfate-resistant cement properties
Sulfate-resistant silicate cement is divided into medium-resistant sulfate cement and high-resistant sulfate cement, with strength grades of 32.5, 42.5, and 52.5 respectively.
- Medium sulfate-resistant cement (codename P-MSR) can resist the erosion of medium-concentration sulfate ions, with a tricalcium silicate content not exceeding 55.0% and a tricalcium aluminate content not exceeding 5.0%.
- High sulfate-resistant cement (codename P-HSR) can resist the erosion of high-concentration sulfate ions, with a tricalcium silicate content of less than 50% and a tricalcium aluminate content of less than 3%.
Compressive Strength | Loss on Ignition | Free Lime Content | Magnesium Oxide Content | Insoluble Residue Content | Specific Surface Area | Initial Setting Time | Final Setting Time |
10 MPa at 3 days, 16 MPa at 7 days, 33 MPa at 28 days | ≤ 3% | ≤ 1.0% | ≤ 5% | ≤ 1.5% | ≥ 280 m²/kg | ≥ 45 minutes | ≤ 10 hours |
Properties of Sulfate Resistant Cement
Sulfate resistant cement has some unique properties that make it different from ordinary cement.
- Lower heat of hydration: SRC generates less heat when it cures. This is essential for large structures. Excessive heat can cause cracks.
- Increased durability: SRC is more durable due to its lower C3A content. It is resistant to sulfate attack, which increases the life of the concrete.
- Longer setting time: SRC cement takes slightly longer to set than ordinary cement. This is helpful for complex projects.
- Good workability: SRC is easy to mix and pour even with special formulations. This makes it convenient for construction workers to use.
- Strength: SRC can withstand heavy loads and is suitable for building strong structures. Its strength is usually comparable to or even higher than that of ordinary cement.
- Resistance to hydration: SRC resists hydration in the presence of sulfates. This allows the concrete to remain intact for a long time.
- Chemical resistance: This cement resists chemical attack, especially from sulfate ions. This property helps the concrete remain strong and durable.
- Low shrinkage: Sulfate-resistant cement shrinks less than ordinary cement after drying. This means a lower risk of concrete cracking.
- This cement has maximum resistance to chloride ions, minimizing the risk of steel corrosion.
- Has excellent workability and pumpability.
Application of sulfate-resistant cement
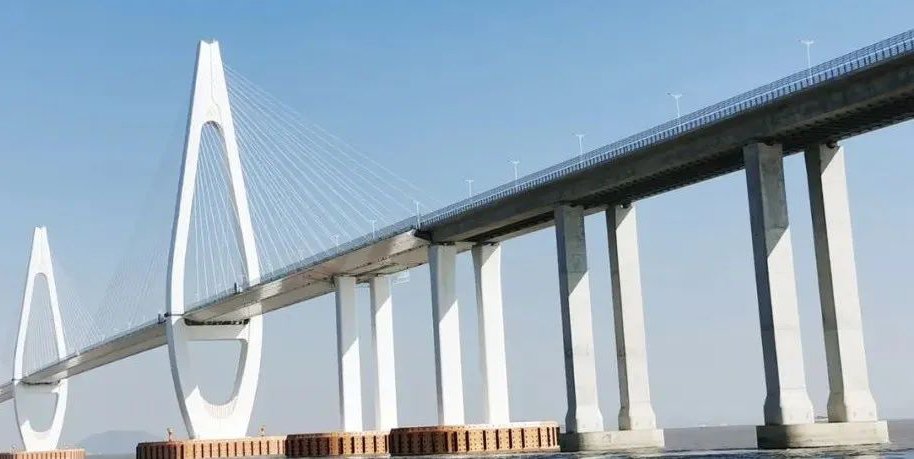
Some construction projects use sulfate-resistant cement. This type of cement is used in areas that are most affected by sulfates. Here are some common uses:
- Foundations: SRC is often used to build foundations in areas where there is high sulfate content in the soil or water. This helps prevent the foundation from getting damaged over time.
- Wastewater treatment plants: SRC is used in wastewater treatment plants. It handles the corrosive chemicals in the wastewater.
- Marine structures: Structures such as piers and docks are built using steel reinforced concrete (SRC). These structures are exposed to seawater, which contains sulfates. This helps keep them strong and safe.
- Concrete repair projects: Builders often use SRC when repairing concrete that has been damaged by sulfates. It ensures that the repaired concrete is long-lasting and durable.
- Infrastructure projects: SRC is used in highways, bridges, and other infrastructure that are at risk of sulfate exposure. This ensures the durability of these structures.
Advantages and Disadvantages of Sulfate-Resistant Cement
Sulfate-resistant cement, like any material, has its advantages and disadvantages. Here are its advantages and disadvantages:
advantage:
- Enhanced durability: SRC helps structures resist sulfate damage, thereby extending their service life.
- High strength: This cement has excellent compressive strength, which helps it withstand heavy loads.
- Reduced maintenance costs: SRC is not susceptible to sulfate attack. Therefore, structures built with it require little maintenance.
- Versatility: SRC is a flexible option that can be used in a variety of construction projects.
Disadvantages:
- Higher cost: Sulfate-resistant cement is more expensive than regular cement. This can increase the overall cost of a project.
- Longer setting time: The longer time it takes to set may not be suitable for every project, especially those that need to be completed quickly.
- Limited supply: SRC can be difficult to find in some places. This can make it difficult for some builders to use it.
Sulfate-resistant cement manufacturing process
The raw materials required to produce sulfate-resistant cement are basically the same as those of ordinary Portland cement, mainly including calcareous materials, clayey materials and iron-containing correction materials, but its mineral composition is very different from that of ordinary Portland cement.
- The hydration product of C3A is the most susceptible component in cement. Since C4AF has stronger corrosion resistance than C3A, C4AF is used to partially replace C3A in sulfate-resistant cement to improve the corrosion resistance of cement.
- CH produced during the hydration of C3S is another factor leading to corrosion. Therefore, appropriately reducing the C3S content and correspondingly increasing the C2S with better performance is also an effective measure to improve the corrosion resistance of sulfate-resistant cement.
The production process of sulfate-resistant cement is basically the same as that of ordinary Portland cement and can be divided into:
Raw material preparation
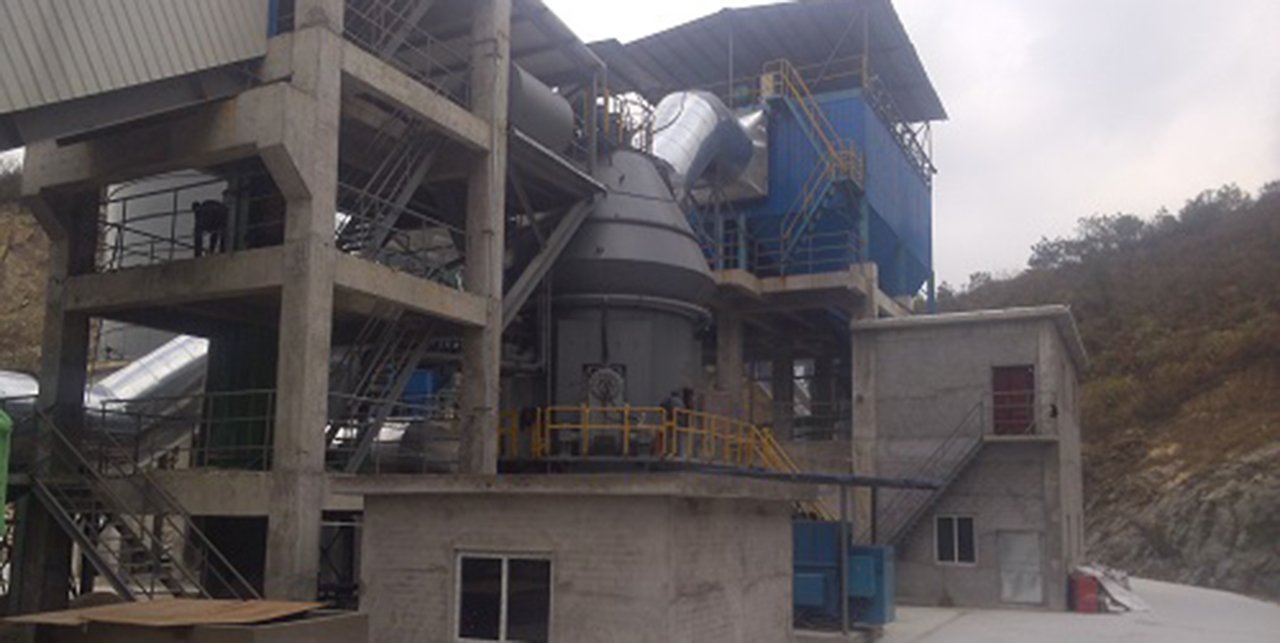
Raw materials such as limestone and clay are first crushed to the raw material mill feed size by cement crushers, and then stored in pre-homogenization yards, mixed in proportion and sent to cement raw material vertical roller mills for subsequent fine grinding. The finely ground raw materials are stored in silos waiting for calcination.
Clinker calcination
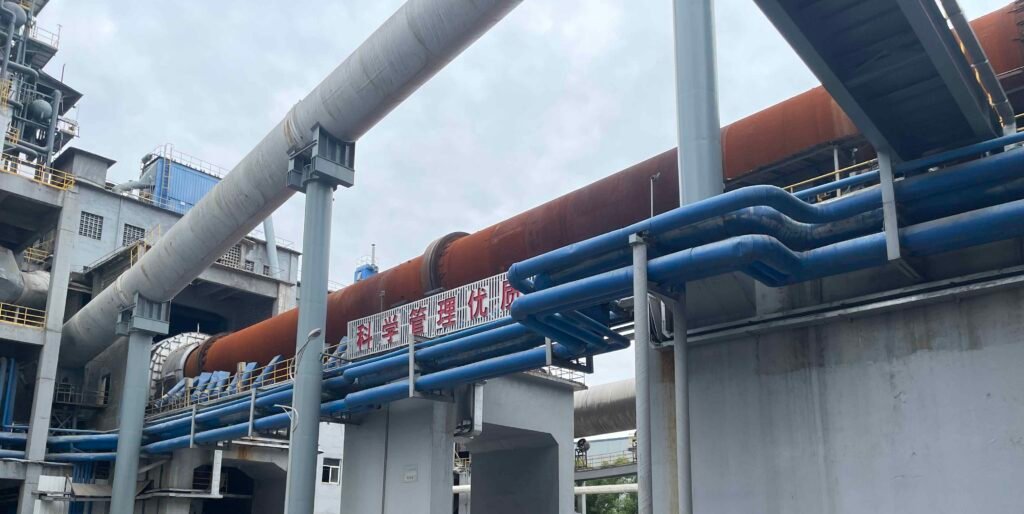
During the calcination process, the cement raw materials first enter the preheater and decomposition furnace to complete preheating and partial carbonate decomposition. Then they are sent to the cement kiln for formal calcination until clinker is formed. After that, the high-temperature clinker is cooled to room temperature in the cement cooler after the kiln.
Cement grinding
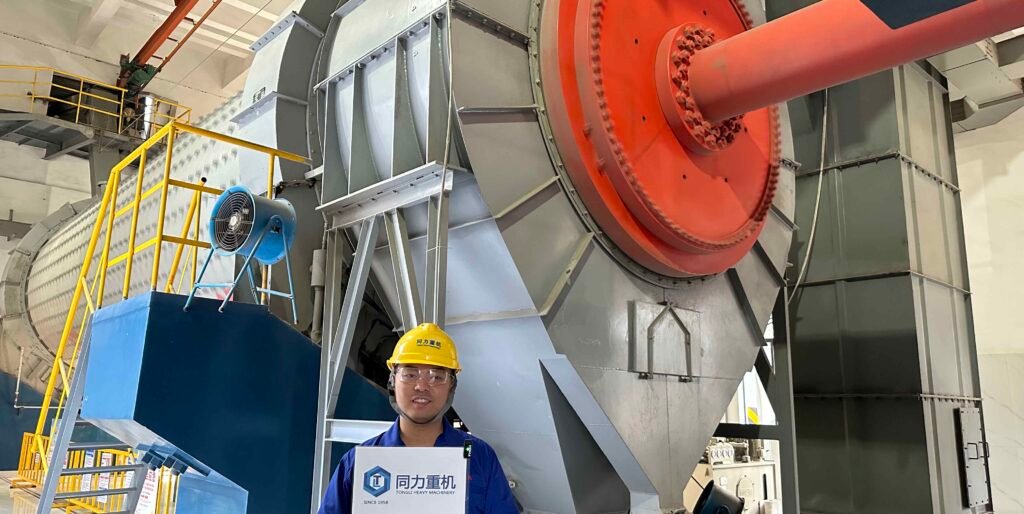
Cement clinker is usually mixed with gypsum and other admixtures with specific characteristics and then sent to the cement mill. In the cement ball mill, the clinker is finely ground until it reaches the fineness required for cement products. The ground cement powder is stored in cement silos and then packaged by cement packaging machines.
Related cement equipment
- Raw material crusher
- Pre-homogenization equipment
- Fine grinding machine
- Clinker calcining equipment
- Cement grinding machine
- Cement packaging machine
Precautions before using sulfate-resistant cement
Before using sulfate-resistant cement, consider the following:
- Soil testing: It is important to test the sulfate content of the soil. This helps determine if the project requires the use of SRC.
- Project requirements: Consider the specific needs of the construction project, such as environmental conditions and the expected loads on the structure.
- Cost analysis: Compare the cost of using SRC cement versus ordinary cement and consider the potential long-term benefits of choosing SRC cement.
- Construction schedule: Remember that SRC takes longer to set. This must be factored into the construction schedule. This ensures that the project stays on schedule.
Sulfate-resistant cement is key to building in areas with high sulfate content. Its unique properties can extend the life of concrete. While sulfate-resistant cement has its pros and cons, carefully evaluating your needs and conditions can help you make the right choice. When used correctly, sulfate-resistant cement (SRC) can create strong, durable structures.
Conclusion
In summary, sulfate-resistant cement (SRC) is an important engineering material that is formulated specifically to resist the damaging effects of sulfate ions found in groundwater, seawater, and certain soils. By significantly reducing the content of tricalcium aluminate (C3A), SRC minimizes the formation of expansive and weakening compounds such as ettringite and wollastonite that can cause cracking, spalling, and structural failure in traditional Portland cement. This makes SRC an essential choice for durable concrete foundations in sulfate-rich environments, marine structures, sewage systems, and other infrastructure exposed to aggressive chemical conditions. While proper concrete mix design, placement, curing, and permeability control remain critical, selecting a sulfate-resistant cement is a fundamental first step in ensuring the long-term integrity and service life of concrete structures exposed to sulfate attack.