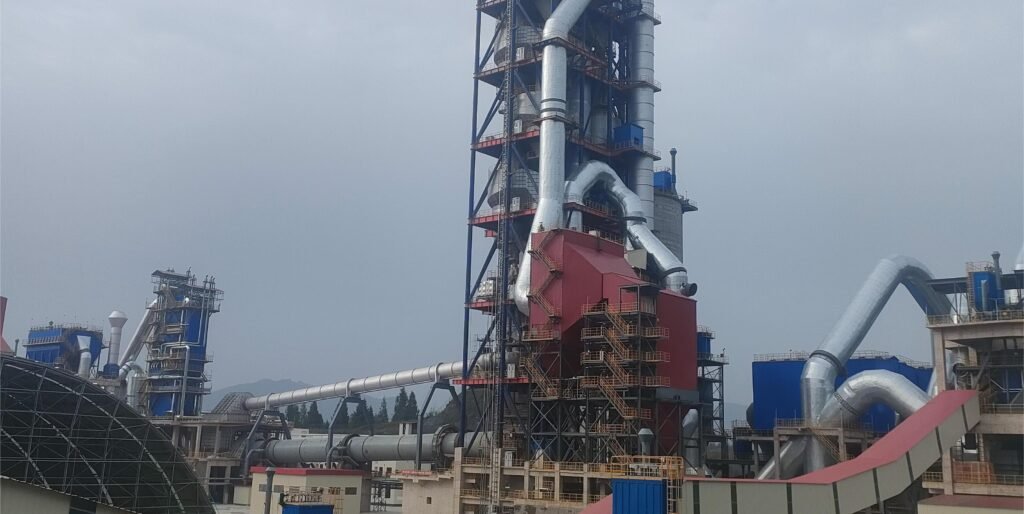
As an No.1 important process in construction, cement production has developed from wet process, semi-dry process to dry process. Dry process, especially the new Tongli dry kiln decomposition process, has replaced traditional methods, and has become the mainstream technical route for many morden cement production plant. This article we wrote analyzes the technical principles, core processes, key equipment, outstanding advantages, challenges and future development trends of dry process. We have detailed discussions on raw material grinding, preheating decomposition, clinker calcination and waste gas treatment, it shows our effort in maximizing the capacity in cement production. So far, the new dry process cement equipment rate in developed countries such as Japan and Germany has reached 95%.
Definition of dry cement process
The dry process cement production process is a process in which the raw materials are ground and mixed in a dry state. This is different from the wet process cement production process, in which the raw materials are mixed with water. In the dry process cement production process, the moisture content is reduced to a minimum from the beginning, which significantly saves energy and fuel consumption in the subsequent production stages.
Core principles and technical features of dry process
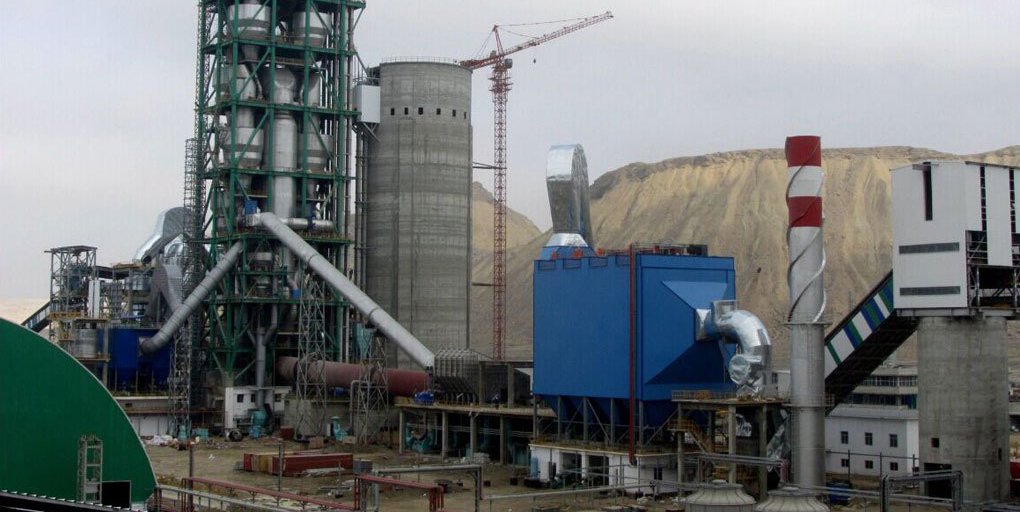
Different from the wet process, which makes the raw materials into slurry with 30%-40% water content, the core features of the dry process are:
- Raw material preparation: The raw materials (limestone, clay, correction materials, etc.) are crushed and dried, and then directly ground into dry raw material powder with a moisture content of usually less than 1%.
- New type of pre-decomposition outside the kiln: The core breakthrough is to add a preheater (Preheater) and a decomposition furnace (Calciner) before the rotary kiln to form a preheating and pre-decomposition system at the end of the kiln.
- Preheater (multi-stage cyclone): Use the high-temperature exhaust gas (~1000℃) at the end of the kiln to preheat the raw material powder in multiple stages (usually 4-6 stages). The gas-solid heat exchange efficiency is extremely high, and the material temperature rises to ~800℃.
- Decomposition furnace: The calcium carbonate decomposition reaction (CaCO₃ → CaO + CO₂), which accounts for 50%-60% of the total heat consumption and is the most energy-consuming, is moved from the rotary kiln to a special decomposition furnace (the decomposition rate can reach 90%-95%). An appropriate amount of fuel (accounting for ~60% of the total fuel) is sprayed into the decomposition furnace, and preheated tertiary air is introduced to assist combustion, providing the required heat for the strong endothermic reaction.
Characteristics of new dry process cement production technology
Small pollution
The new dry process cement production technology makes full use of the limestone resources discarded by traditional mining methods, and uses pre-decomposition technology, suspension preheating technology, multi-channel burner and other technologies to reuse the recycled low-quality fuel, effectively reducing the emission of waste gas such as NO2 in the system.
Low consumption
The cement production process adopts new conveying equipment and multi-functional grinding system to effectively save energy consumption. At the same time, the use of pre-decomposition and suspension preheating technology improves the calcination efficiency of traditional cement kilns and continuously reduces the energy consumption required for clinker calcination. At present, the heat consumption of clinker calcination can be reduced to 3000kJ/kg.
Long construction period
Since the new dry process cement production technology has high requirements for production equipment, transportation, geology, raw materials, etc., and consumes a lot of refractory materials, its construction period and initial investment are higher than traditional production technology.
High quality
Since the new dry process cement production process uses highly automated equipment, the operation of the entire cement production line is consistent and stable, and each link cooperates closely, ensuring the high quality and high yield of cement production.
Dry process cement production process section guide
Raw Materials Preparation
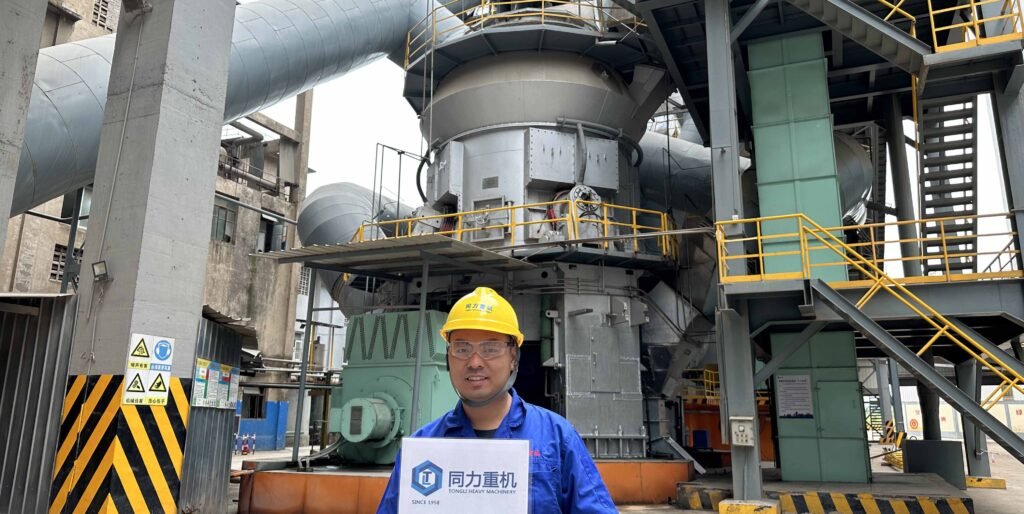
Cement production begins with the procurement of key raw materials, typically limestone, clay and sand. These materials go through two main stages:
- Crushing: The raw materials are first broken into smaller pieces for easier grinding and processing.
- Grinding: The crushed raw materials are finely ground by Vertical roller mill into a powder to ensure they can be accurately mixed and proportioned.
This stage is crucial as improper grinding or the wrong proportions can adversely affect the quality of the final product.
Mixing and Proportioning
After the raw materials are ground, they must be precisely mixed and proportioned to achieve the desired chemical composition. The mixture typically contains varying amounts of:
- Calcium oxide (from limestone)
- Silicon dioxide (from sand)
- Aluminum oxide (from clay)
Maintaining the proper proportions is critical to producing high-quality cement. This often requires the use of advanced automated systems to ensure the accuracy of the material mix.
Raw material preheating
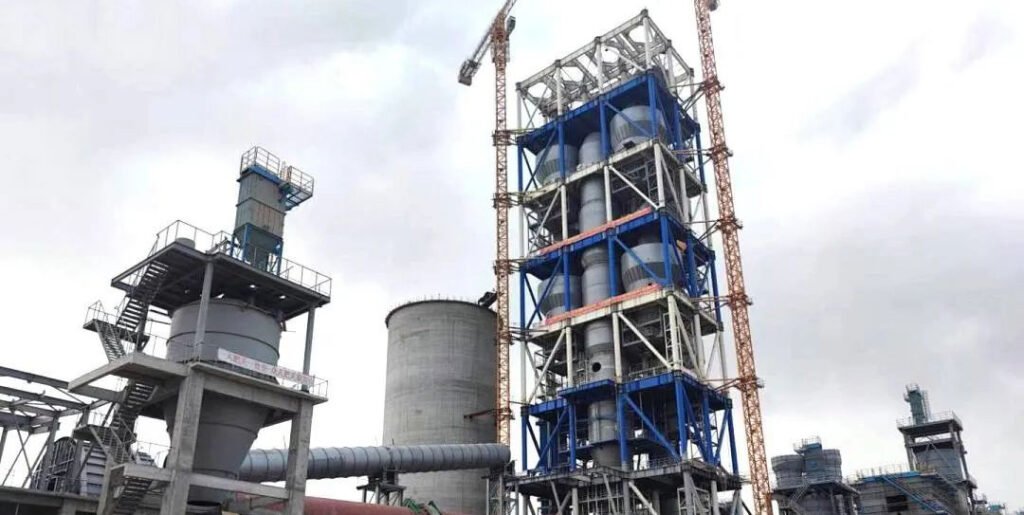
The next step is to preheat the mixed raw materials. Preheating is usually done in a preheating tower, where the temperature reaches about 800°C. There are several key advantages to this stage:
- Moisture reduction: Removal of residual moisture from the raw materials.
- Energy saving: Preheating triggers some chemical reactions, which reduces the energy required by the kiln.
- Process efficiency: The preheating process ensures that the material is already at a higher temperature before entering the kiln, thereby reducing energy consumption during the calcination stage.
Calcination
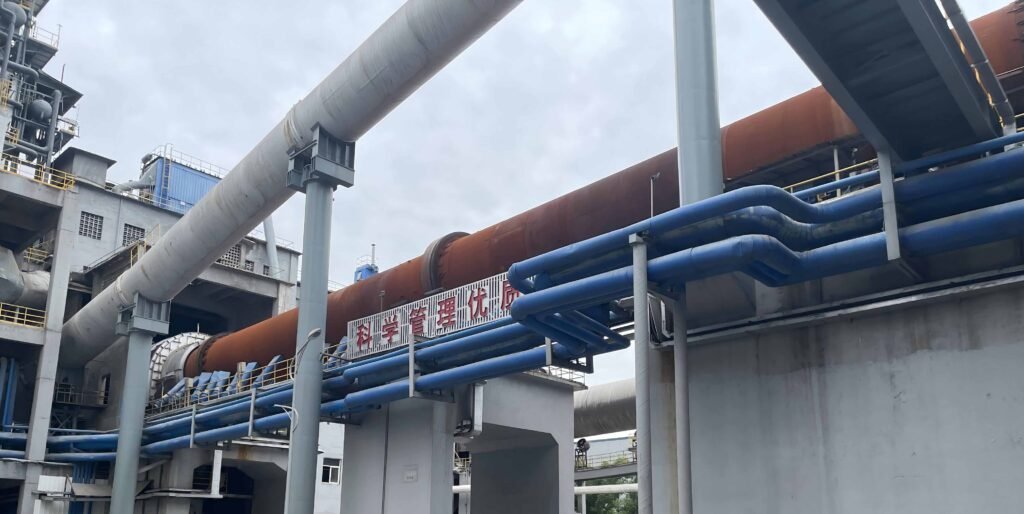
Calcination is the heart of cement production. After preheating, the raw material mixture enters the rotary kiln and is heated to about 1450°C. The high temperature triggers various chemical reactions that ultimately form clinker - an intermediate product in cement production.
The main chemical reactions that occur during calcination include:
- Limestone (calcium carbonate) decomposes into lime (oxide) and carbon dioxide.
- Lime combines with silica, alumina and ferrite to form calcium silicate and calcium aluminate.
These reactions form small, hard clinker nodules, which are essential for producing cement.
Clinker formation
At the end of the calcination process, clinker is formed, which consists of various compounds, mainly including:
- Calcium silicates (C2S and C3S)
- Aluminates (C3A)
- Iron gases (C4AF)
The quality and composition of clinker determine the strength and properties of the final cement product.
Clinker Cooling
After the clinker leaves the kiln, it must be cooled quickly to prevent further chemical reactions and make it easier to handle. Cooling is usually done using air or water and has the following effects:
- Prevent overreaction: Rapid cooling stops the chemical process, ensuring that the clinker retains its desired composition.
- Ease of handling: Cooled clinker is easier to transport and handle during the grinding process.
Clinker Grinding
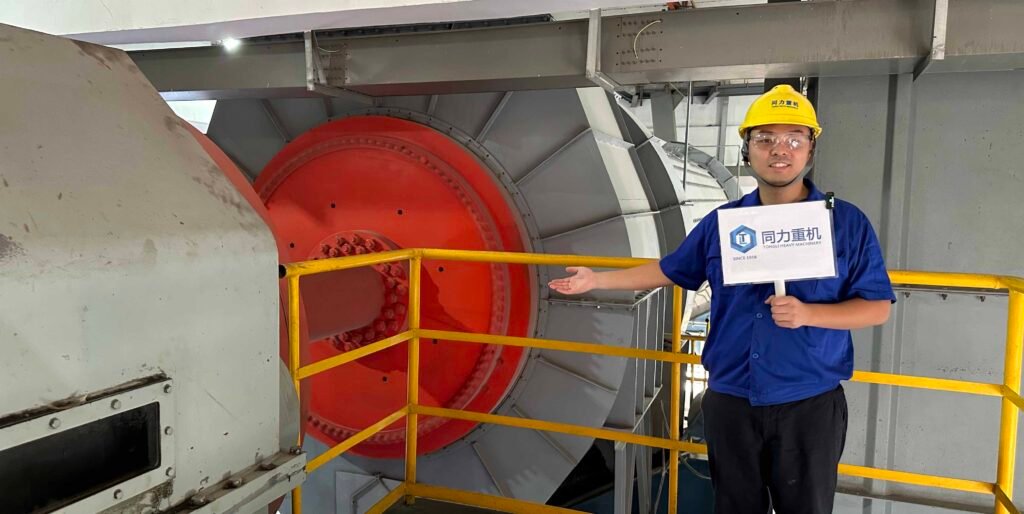
After cooling, the clinker is ground into a fine powder using cement ball mill or vertical mill. At this stage, gypsum is added to the clinker to control the setting time of the final product. Gypsum helps prevent the cement from setting too quickly, making it easier to work with during use. The final product of this grinding process is Portland cement, which is stored in silos until it is packaged for distribution.
The Final Product
After dry process cement is produced, it is stored in silos before being packaged and shipped. Portland cement is used in construction projects around the world for its durability, strength, and versatility. Dry process cement production is not only energy-efficient and environmentally friendly, but also ensures high quality cement.
Advantages of dry process cement production technology
- Energy efficiency
The dry process is more energy efficient than the wet process. By using preheated materials and reducing the moisture content from the beginning, energy consumption can be minimized, thereby reducing operating costs. - Reduced fuel consumption
Because the material is dried before entering the kiln, fuel consumption is significantly reduced. Eliminating the drying stage in the kiln can significantly save fuel, which is one of the largest costs in cement production. - Environmental benefits
The environmental benefits of the dry process are very significant:
Reduced CO2 emissions: Since less energy is required to heat and dry the materials, CO2 emissions are reduced.
Reduced water consumption: The process eliminates the need for water in the initial mixing stage, which helps to save water resources.
By optimizing energy consumption and reducing emissions, the dry process contributes to a more sustainable method of cement manufacturing.
Essential cement equipment for dry process cement production line
Raw material conveying system
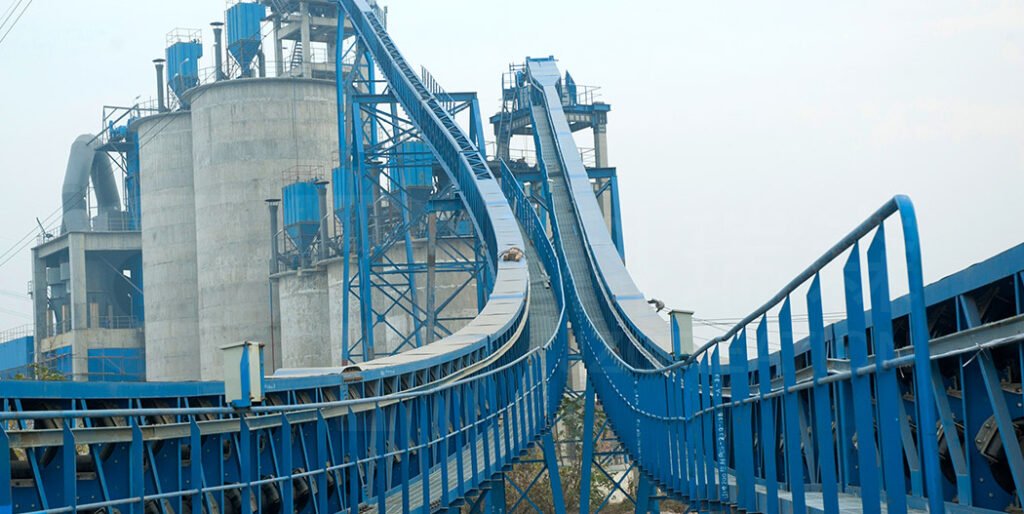
Limestone, dolomite and other raw materials are crushed and transported to the cement plant. They are transported to the storage warehouse by forklifts and lifted to the raw material warehouse. After measurement, qualified 10-50mm limestone is transported to the top warehouse of the preheater. The feed particle size is 10-50mm, and the finished product particle size is 5-40mm, reaching more than 90%.
Active lime calcining system
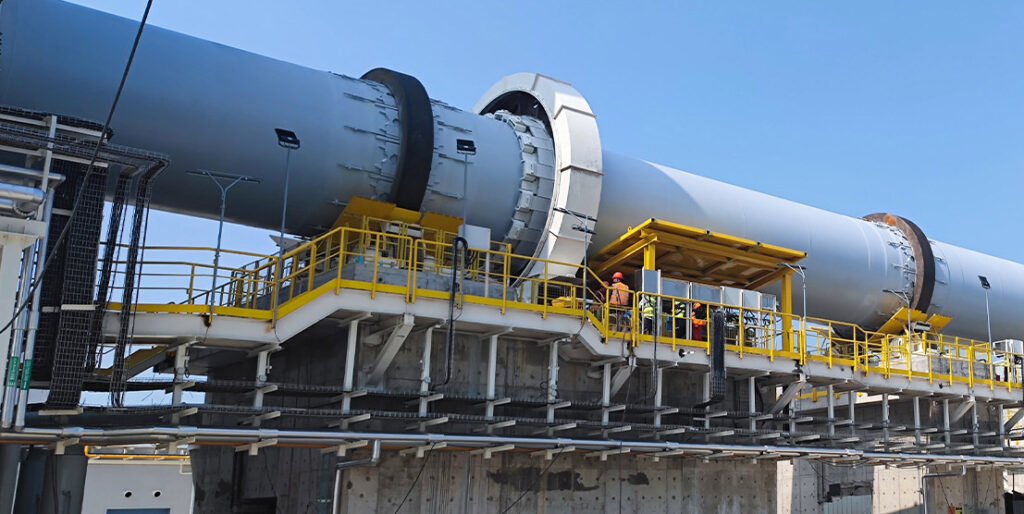
The active lime calcining system consists of a vertical preheater, a rotary kiln, a cooler and other auxiliary equipment.
- Vertical preheater: The vertical preheater consists of a preheater body, a storage bin, a feed pipe, a hydraulic push rod device, etc. The polygonal and circular preheaters use a compartment device to gradually heat up the limestone to avoid excessive temperature rise and explosion and the production of a large amount of powder. The decomposition rate of limestone entering the kiln reaches 30%∽40%, and the average temperature of the exhaust gas is 230℃∽260℃, which reduces the heat consumption of the system.
- Rotary kiln: The rotary kiln consists of a cylinder, a support device, a variable speed transmission device, a wheel stop device, a kiln tail kiln head seal, a kiln head cover, etc. The kiln body is placed at an inclination angle of 3.5% with the horizontal plane. There are two sets of support devices, and the support wheel bearing is a water-cooled oil spoon lubricated sliding bearing with an automatically aligning spherical bush. A hydraulic wheel stop device is also provided near the large gear ring. The kiln body is driven by a variable frequency speed regulating motor, and an auxiliary transmission device is set to drive the kiln body. The kiln head and kiln tail adopt a spring sheet sealing device. The kiln body is driven by a variable frequency motor, and the decomposition rate of the preheater is used to effectively control the calcination time and temperature to meet the requirements of raw materials and overburning indicators. The burner adopts a four-channel burner for mixed combustion of coal and gas. It is flexible and convenient to adjust and easy to operate. The injection speed of each air duct can be adjusted at will during operation, and any flame required under different kiln conditions can be adjusted. The calcination temperature in the kiln is easy to control.
Coal powder preparation system
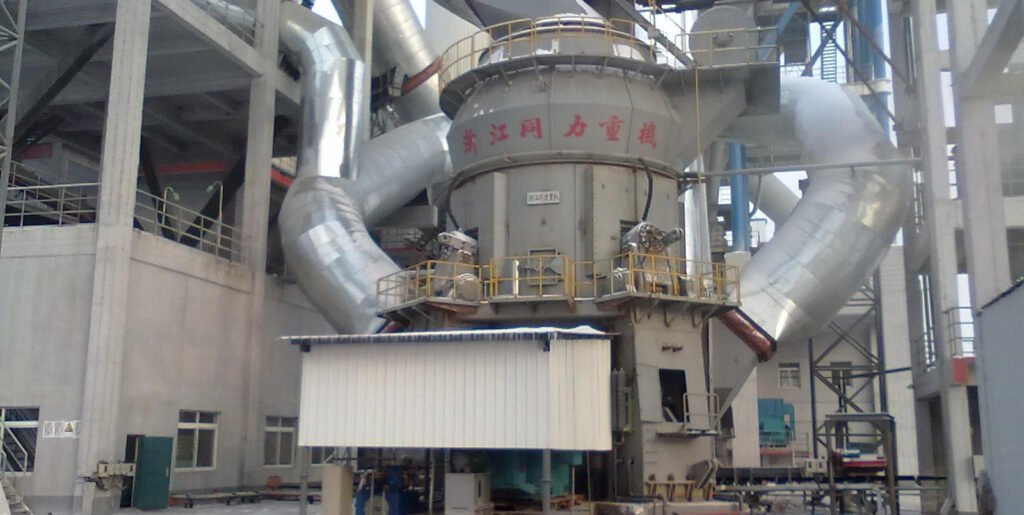
Coal powder preparation is an important part of the active lime rotary kiln system using coal. There are generally two systems. One is a coal powder preparation system composed of a wind-swept pipe coal mill and a bag dust collector. This system has the advantages of easy operation and clean environment. Its production process is as follows:
The lump coal with a size of ≤25mm is supplied to the belt by the process bucket elevator, and is input into the raw coal bin through the belt, and then sent to the coal mill through the disc feeder or electromagnetic vibrating feeder at the bottom of the raw coal bin. It is a device that integrates grinding and drying. During grinding, hot air from the rotary kiln system or hot flue gas from the auxiliary combustion chamber is introduced for drying. The coal powder gas from the coal mill enters the coal mill for separation under the action of the exhaust fan, and the coarse coal powder returns to the coal mill through the automatic ash discharge valve for re-grinding. The fine powder is carried into the bag dust collector with the air flow to collect dust, so as to achieve the purpose of powder gas separation. The gas from the powder selector is discharged by the exhaust fan after dust collection and purification. Part of the exhaust gas is blown into the coal mill for recycling, and the other part of the exhaust gas is discharged into the atmosphere through the chimney. The coal powder collected by the dust collector is discharged into the coal powder storage bin in front of the kiln. According to needs, the coal powder is sent to the burner in front of the kiln through a Roots blower, and the burner combustion fan provides combustion air for calcining limestone.
Finished product conveying system
The finished lime is transported from the cooler to the elevator via the chain bucket conveyor, and then to the top of the silo via the bucket elevator. After screening, qualified products with a particle size greater than 5mm are sent to the finished product silo by the belt conveyor, and powder materials less than 5mm are sent to the powder silo. Electric discharge valves are installed at the bottom of the silo, the finished product silo, and the powder silo. The main function of the finished product silo here is buffering and metering. The finished products should be sent to the steel plant and calcium carbide plant in time to reduce powdering.
Flue gas treatment system
The high-temperature flue gas generated by the combustion of the rotary kiln undergoes heat exchange with the limestone in the preheater, and the temperature drops to below 260°C. After being cooled by the multi-tube cooler, it enters the high-temperature bag dust collector. After dust removal, it is discharged into the atmosphere through the chimney by the high-temperature fan. The dust concentration of the flue gas discharged into the atmosphere is less than 30mg/Nm³. In order to meet the process requirements of the modern active lime pre-decomposition rotary kiln production line, ensure the reliable operation of the process equipment, stabilize the process parameters, ensure product quality, save energy, and improve the operation rate of the production line. The entire line adopts advanced technology and full-process control. On the basis of PLC control, DCS control is added to centrally monitor, operate and disperse the main production line, control the rotary kiln operating system, improve product quality, and reduce consumption. Improve the reliability and maintainability of electronic control equipment and realize the modernization of control, monitoring, and operation.
Cement Grinding Station
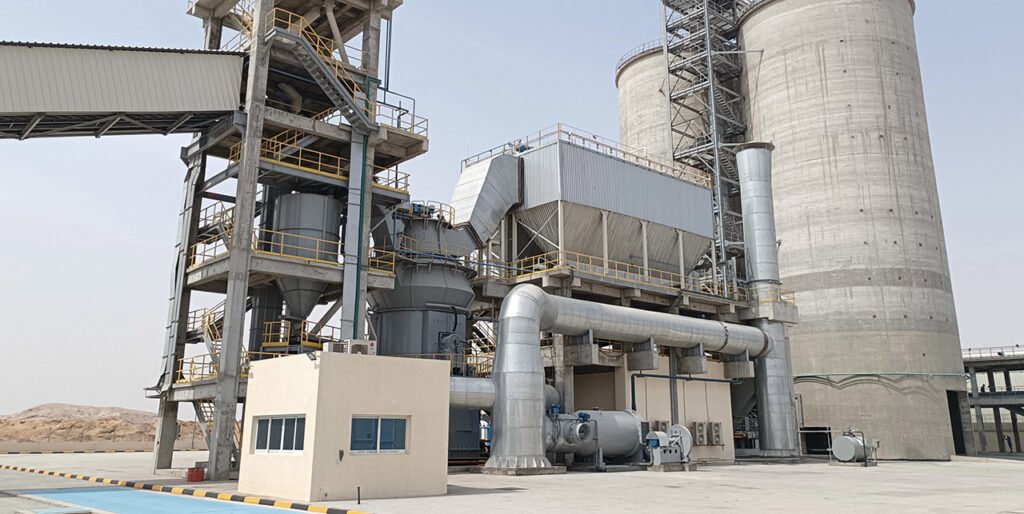
VRM Cement grinding station is a finished cement production unit in the final product separation stage of cement production. In this stage, cement clinker is added to the appropriate amount of mixed materials for pulverization to produce finished cement. Cement production can generally be divided into three processes: raw material preparation, clinker calcination and cement production. The production process of Portland cement is representative in cement production. It uses limestone and clay as the main raw materials, which are lifted to the silo by bucket elevator, connected to the hot air furnace through the dryer, and then lifted by bucket elevator. After reaching the homogenization silo, it enters the ball mill and then enters the powder selector through bucket elevator. The fine materials then enter the screw conveyor through the bucket elevator and are transported to the cement silo separately. Each cement silo is equipped with a screw conveyor for finished product transportation.
Comparison of wet and dry processes for cement production
There are two different processes for cement production. The wet process is to grind the mineral wet (by adding water) to form a slurry and then dry it; the dry process is to grind the mineral dry to form a powder. Both processes are in use and have their own advantages and disadvantages. Wet grinding is easier, while the dry process can save the fuel cost required to dry the slurry.
Wet Process
1- The raw materials are mixed with 35% to 50% water in a ore washer.
2- The material coming out of the mill is called "slurry" and has a fluid nature.
3- The kiln size required for producing cement is larger.
4- The raw materials are easy to mix, so a more homogeneous material can be obtained
5- The fuel consumption is high, 350 kg of coal is consumed for each ton of cement produced.
6- The production cost is high.
7- The capital cost (setup cost) is relatively less.
Dry Process
1- The raw materials are mixed in a dry state in a mixer.
2- The dry material coming out of the mill is called "kiln charge".
3- The kiln size required for producing cement is smaller.
4- The mixing of raw materials is difficult to control, so it is difficult to obtain a more homogeneous material.
5- The fuel consumption is low, only 100 kg of coal is consumed for each ton of cement produced.
6- The production cost is low.
7- The capital cost is high due to the mixer.
Energy consumption and efficiency
Dry process:
The decomposition technology outside the kiln moves 60% of the fuel to the decomposition furnace, greatly reducing the heat load of the rotary kiln.
The moisture content of the raw material is less than 1%, and there is no need to evaporate the moisture. The heat consumption is only 50-55% of the wet process.
Wet process:
30%-40% of the moisture in the slurry needs to be evaporated in the kiln, consuming a lot of heat energy (about 35% of the total energy consumption).
The long kiln has large heat loss and the thermal efficiency is less than 40%.
Production scale and economy
Dry method:
- Large-scale single-line production capacity (5000-12000 tons/day), high degree of automation, and low labor costs.
- Although the initial investment is high (about $200-300/ton of production capacity), the long-term operating cost advantage is significant.
Wet method:
- Limited by the heat transfer efficiency of the long kiln, the single-line production capacity is difficult to exceed 3000 tons/day.
- Low investment (about $100-150/ton) is offset by high energy consumption, and the economy is poor.
Comparison table of dry process vs wet process cement production process
Comparison Dimension | Dry Process Technology | Wet Process Technology |
Core Principle | Raw materials are dried and ground into dry raw meal (<1% moisture), then fed into kiln | Raw materials are mixed with water into slurry (30%–40% moisture), then fed wet into kiln |
Representative Technology | New Suspension Preheater (NSP) system | Long rotary kiln wet process |
Raw Material Processing | ▶ Crushing → Drying → Dry grinding → Homogenization | ▶ Crushing → Wet grinding (with water) → Homogenization |
Calcination System | ▶ Preheater + Calciner + Short rotary kiln (length 60–80 m) | ▶ Long rotary kiln (length 150–200 m) (no preheater/calciner) |
Heat Consumption (per ton of clinker) | 720–760 kcal/kg (3.0–3.2 GJ/t) | 1200–1400 kcal/kg (5.0–5.8 GJ/t) |
Power Consumption (per ton of cement) | 80–90 kWh | 100–120 kWh |
Thermal Efficiency | High (efficient waste heat recovery) | Low (large heat loss due to water evaporation) |
CO₂ Emissions | Lower (less fuel consumed) | Higher (more fuel + evaporation losses) |
Dust Emissions | Easy to control (negative pressure system + efficient dust collection) | Hard to control (wet material adhesion, low collection efficiency) |
Single-Line Capacity | High (up to 10,000 tons/day or more) | Low (typically ≤3000 tons/day) |
Investment Cost | Higher (complex equipment) | Lower (simple equipment) |
Operating Cost | Low (low energy use, less labor) | High (high energy use, frequent maintenance) |
Clinker Quality | Stable (high degree of raw meal homogenization) | Fluctuates (slurry composition difficult to homogenize) |
Raw Material Adaptability | ▶ Requires low-moisture raw materials (<10%)▶ Can utilize industrial waste | ▶ Suitable for high-moisture/sticky materials (e.g., kaolin, sludge) |
Water Consumption | Very low (only for cooling) | Very high (for slurry preparation and evaporation) |
Current Industry Share | >95% (mainstream globally) | <5% (largely phased out) |
FAQ
Energy efficiency demand: There is a growing demand for energy-efficient and environmentally friendly manufacturing processes.
Urbanization and infrastructure: Rapid urban development in the Asia Pacific, Middle East and Africa, and Latin America regions has driven the demand for cement production.
Industrial modernization: Increased automation and process control capabilities in developing economies.
Government initiatives: Green building policies and emission regulations compliance encourage the adoption of new dry process production lines.
Reducing clinker coefficient: There is a growing interest in sustainable cement ingredients that have less impact on the environment.
Lower carbon footprint: CO2 emissions are significantly reduced compared to traditional wet process.
Reduced water consumption: No water is required in the mixing and heating stages, solving the problem of water shortage.
High product quality: Uniform clinker production leads to excellent cement performance and durability.
Energy saving: Thermal energy efficiency is between 3300–3600 kJ/kg clinker, while the thermal energy efficiency of wet process is 5200–5600.
Global industry standard: More than 90% of new cement plants worldwide use dry process production lines for their long-term viability.
Emerging Economy Growth: India, Vietnam, Indonesia and Nigeria are witnessing strong growth in demand for dry process plants.
Brownfield Expansion: Retrofitting old kilns and grinding units with dry process capabilities is gaining momentum.
Greenfield Projects: Large-scale dry process facilities in resource-rich regions offer high ROI prospects.
Public-Private Partnerships: Strengthening collaboration on infrastructure projects using advanced cement technology.
Equipment and Automation Suppliers: Suppliers of rotary kilns, preheaters and control systems are benefiting from the influx of capital investment.
High initial capital investment: The cost of installing a full trunk line infrastructure remains a barrier for small and medium-sized enterprises.
Shortage of technical expertise: Emerging markets lack a skilled workforce to manage advanced automation systems.
Complexity of environmental regulation: Complying with evolving global standards and carbon tax frameworks adds complexity.
Raw material fluctuations: The cost and availability of limestone, bauxite and other additives fluctuate.
Supply chain disruptions: Logistical challenges and equipment lead time constraints affect project timelines.
Smart cement plants: AI and IoT driven cement production facilities are expected to dominate by 2030.
Carbon neutral manufacturing: Net zero emission targets drive innovation in clinker substitutes and low energy consumption processes.
Decarbonization investments: Global cement companies are committed to large-scale decarbonization R&D programs.
Government subsidies: Financial incentives for green manufacturing and infrastructure resilience to promote the adoption of dry process production lines.
Export opportunities: Plants in the Asia Pacific region export clinker to Africa and Latin America, creating cross-border investments.
Conclusion
Dry process cement production technology, especially the Tongli new dry process outside the kiln, represents the highest level of cement manufacturing technology today. Through a series of our patented technologies such as dry grinding of raw materials, multi-stage suspension preheating, efficient combustion of fuel outside the kiln to decompose calcium carbonate, efficient rapid cooling of clinker and deep utilization of waste heat from exhaust gas, it has achieved a significant reduction in energy consumption and effective control of environmental emissions.