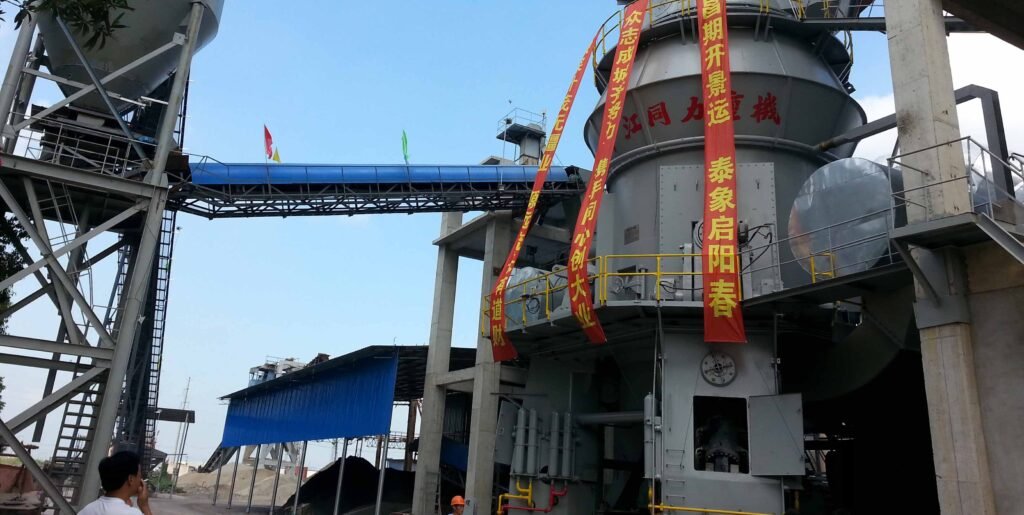
Introduction:
In the vertical cement mill grinding process, the fluctuation of raw material moisture easily causes the vertical mill to vibrate. Generally, water spraying is used to stabilize the material bed, but water spraying easily causes hydration of clinker and reduces the strength of cement. In order to achieve grinding without water spraying, the grinding roller, powder selector, air ring, etc. are modified. The results show that the technical transformation reduces the clinker ratio by 2.9%, increases the output by 19%, and reduces the unit power consumption by more than 3.3 kWh/t, achieving the goal of increasing production, reducing consumption, saving energy and reducing carbon footprint. So to start with this article today, let's first introduce why we use vertical roller mill in cement plant.
Preface: Why use vertical roller mill in cement plant
The use of vertical mill system to grind cement has many advantages, such as simple process, convenient operation, high grinding efficiency, low unit power consumption, and small maintenance workload. There are many factories in China that use vertical mill to grind cement. More than 70% of newly built cement production lines abroad use vertical mill final grinding system. PPC Company, a customer of TONGLI, has 2 sets of LM56.3+3c/s large cement vertical mills, grinding P·042.5 grade cement with an output of about 210 t/h and unit power consumption of 31 kWh/t. In order to stabilize the material bed, water needs to be sprayed into the mill…, but it is easy to cause hydration of clinker and affect the strength of cement. In order to further save energy and reduce consumption and reduce costs, a number of measures have been taken for transformation.
Vertical raw mill grinding system process flow:
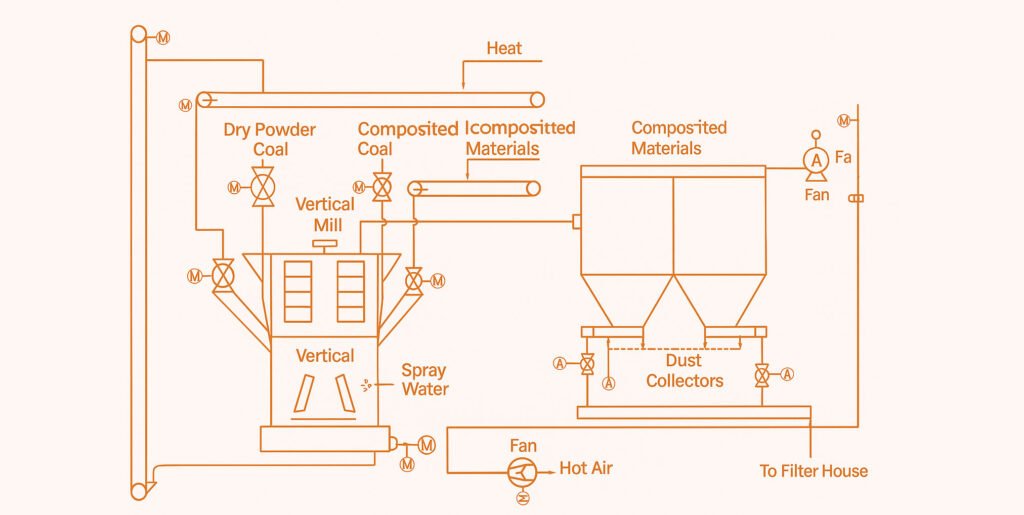
The flow chart of the vertical raw mill system of PPC Company is shown in Figure 1. The mill has 4 feeding points, 1 for feeding clinker, 1 for feeding gypsum and mixed materials, and 2 for feeding dry fly ash. In order to avoid the agglomeration of dry and wet materials and the agglomeration of the air lock valve, clinker and mixed materials are fed into the grinding disc from their respective feeding points. Due to its high specific surface area, dry fly ash enters the vertical raw mill through the air lock valve, is first selected by the powder selector, and the coarse material returns to the grinding disc for grinding, which is conducive to increasing production and reducing the pressure difference of the mill. The finished product obtained by the vertical mill grinding and powder selection is collected by the dust collector and then transported to the storage elevator. The heat source of the vertical mill drying comes from the exhaust gas (about 120℃) at the outlet of the cooling head exhaust fan to ensure that the moisture content of the cement is controlled to <0.5%. The equipment parameters of the system are shown in Table 1, and the equipment operation parameters before the transformation are shown in Table 2. The three material spreading rollers of the mill were dismantled in 2012.
Table1: Vertical roller mill cement plant grinding system equipment list:
Equipment item | Parameters/technical specification |
Grinding Mill | Qty: 1 |
Model: LM56.3+3e/s; | |
Grinding Table Diameter: 5600mm; | |
Grinding Table Speed: 22.09r/min; | |
Number of Grinding Rolls: 3; | |
Middle Diameter of Grinding Roll: 2360mm; | |
Width of Grinding Roll: 785mm; | |
Diameter of Hydraulic Cylinder: 480mm; | |
Diameter of Piston Rod: 145mm; | |
Power: 5300kW; | |
Output: 205t/h for P·042.5 Grade Cement | |
Powder Selector | Qty: 1 |
Diameter: 5150mm; | |
Height: 3445mm; | |
Maximum Speed: 125r/min; | |
Power: 400kW | |
Centrifugal blower | Air Volume: 300,000m³/h; |
Air Pressure: 6000Pa; | |
Power: 2200kW | |
Bag Type Dust Collector | Maximum Handling Air Volume: 650,000m³/h; |
Filtration Air Speed: 0.8m/min; | |
Resistance: 1200Pa | |
Return Material Elevator | Lifting Capacity: 150t/h; |
Power: 30kW |
4 Existing problems of vrm in PPC cement plant

Power consumption:
(1) PPC Company uses 2-3 t/h water spraying to stabilize the material bed. The P·042.5 grade cement ratio is 1%-2% more clinker than the roller press + ball mill semi-final grinding system. Not only is the cement production cost high, but the power consumption is also high, reaching 31 kWh/t.
Effective grinding zone small:
The structure of the vrm grinding zone plays a vital role in the grinding capacity and stability of the mill. According to the poor operating stability of the site due to the need for water spraying, it is inferred that the grinding zone may be narrow and the width of the grinding zone needs to be widened to give full play to the grinding capacity of the mill.
Vibration
The mill needs to spray water to stabilize the material layer, but the vibration may also be related to the speed of the vrm grinding roller and the structure of the air ring.
Internal circulation too much:
The internal circulation volume of the vrm powder selector is large and the rotor speed of the powder selector is fast, resulting in low classification efficiency and affecting the performance of the mill capacity.
Table2: Operation parameters of P·042.5-level cement vertical mill system before tongli upgrade
Item | data | Item | data |
Output | 210t/h | Grinding Mill Power | Approximately 3,900 kW |
Water Injection | 2–3t/h | Mill Pressure Difference | 4,800Pa |
Baffle Ring Height | 385mm | Grinding Roll Linear Speed | 41 r/min |
Material Layer Thickness | 50–70 mm | Powder Selector Power | 130–180 kW |
Effective Area of Air Ring | 3.98m² | Powder Selector Speed | 80 r/min |
Horizontal Vibration Value | 3–5 mm/S | Windmill Baffle Opening | 100% |
Rod Chamber Pressure | 6.5–7.5 MPa | Windmill Power | 1,450–1,650 kW |
Rodless Chamber Pressure | 2.0–2.4 MPa | Hot Gas Temperature | 90℃ |
So above are the problem of the existing system, aftert tongli engineer visited their site, our professional modification recommandations are as follows:
How to improve the efficiency of the vertical roller mill? 6 methods
Widen the grinding area
Update the three roller sleeves (see Figure 2), increase the roller sleeve diameter from 2360 mm to 2570 mm, increase the roller projection area, improve the mill output and grinding efficiency, and reduce power consumption.
Figure 2: Grinding roller zone enlargement design
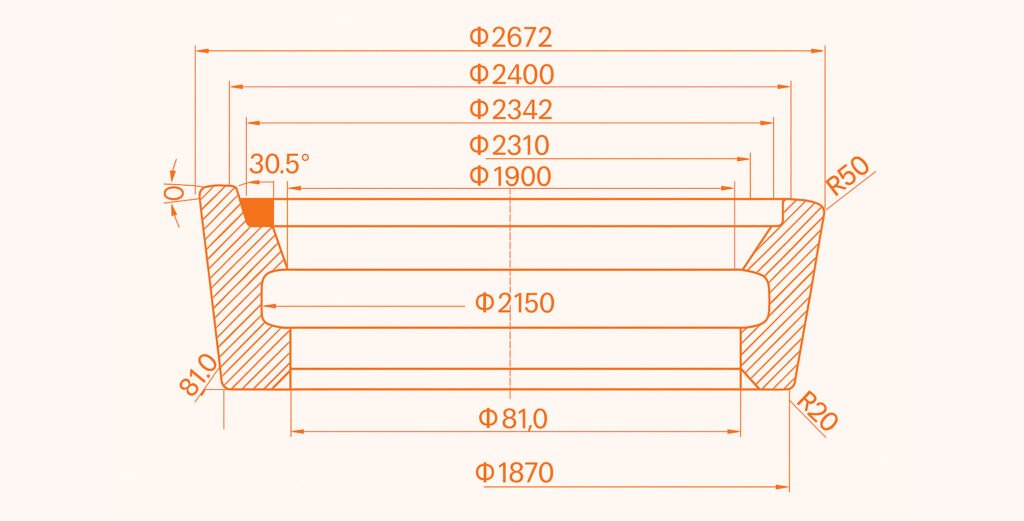
Reduction in linear speed
Keep the grinding disc speed unchanged. Since the grinding disc speed remains unchanged at 22.09 r/min, the linear speed is reduced from 41 r/min to 37 r/min after the roller middle diameter is increased. The reduction in linear speed can increase the grinding pressure and improve the grinding efficiency. At the same time, it can also reduce the vibration of the mill and achieve non-water spraying grinding.
Increase grinding roller taper angle
Optimize the grinding roller taper angle. After the roller middle diameter is increased, the grinding roller assembly can be reused, but the grinding roller taper angle needs to be optimized. The grinding disc size is adjusted by surfacing welding, and the grinding roller taper angle is adjusted from horizontal 0. to 1.6. (see Figure 4) to ensure that it matches the working surface of the new grinding roller.
Figure 4: Grinding roller taper angle increase design

Optimize the height of the retaining ring
The height of the retaining ring corresponds to the thickness of the material layer and has a great influence on the grinding efficiency of the mill. Under the condition of no vibration, the lower the height of the retaining ring, the higher the grinding efficiency of the mill. Increasing the diameter of the grinding roller and reducing the linear speed can reduce the vibration of the mill. Therefore, the height of the retaining ring of the mill is reduced from 385 mm to 265 mm, and the grinding efficiency is improved by reducing the thickness of the material layer.
Replace with a high efficiency
Replace with a low-resistance and high-efficiency powder classifier. The particles ground by the mill need to be sorted by the powder classifier, and the semi-finished products are returned to the mill for grinding. The existing powder classifier has large resistance and low powder selection efficiency. The powder classifier and the upper shell of the mill are replaced as a whole and replaced with a low-resistance and high-efficiency powder classifier to improve the powder selection efficiency and reduce the system resistance.
Adjust wind ring baldes and guide cone angle
Optimize the angle of the wind ring blades and the air guide cone. The mill wind ring structure has a certain influence on the mill resistance. By optimizing the angle of the wind ring blades and the wind guide cone, the wind ring resistance itself can be reduced, and at the same time, the flow field inside the mill can be optimized, the overall mill resistance can be reduced, and the powder selection effect of the wind ring can be improved.
Now let's take a look at how it goes after the improvement.
Vrm cement mill performance after modification:
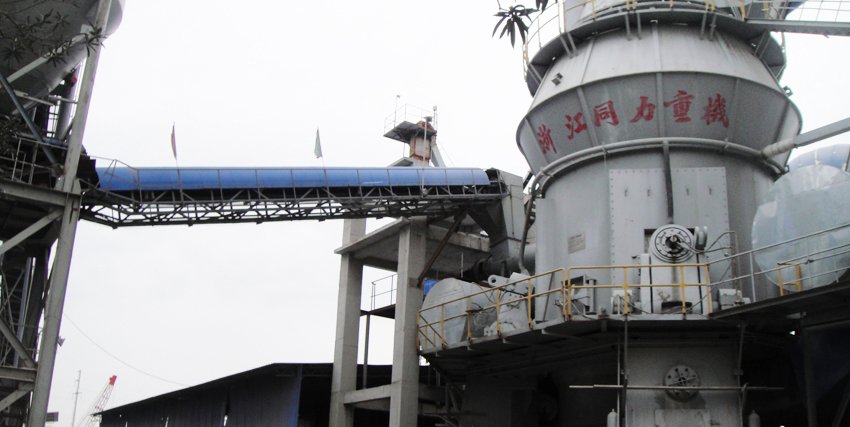
Increased output
Optimized operating parameters: After the transformation, the operating parameters such as the height of the retaining ring, grinding pressure, and system air volume were also optimized, and the cement was successfully ground without water spraying. The output of P·042.5 grade cement increased from 210 t/h to N250 t/h, greatly reducing power consumption. The operating parameters after the transformation are shown in Table 3. As shown in Table 3, the pressure difference of the mill decreased by 500 Pa, and the speed of the powder selector decreased by 12 r/min.
Less clinker is needed, cost is going down, profit is going up
The clinker ratio was reduced. As shown in Table 4, after the vertical mill stopped spraying water, the clinker ratio of P·042.5 grade cement decreased by 2.9%.
Table4: P·042.5 grade cement ratio before and after upgrade
Item | Clinker | Gypsum | Limestone | Coal-fired Slag | Volcanic rock | Fly Ash |
Before Retrofit | 78.5% | 5.0% | 6.0% | 4.0% | 2.0% | 4.5% |
After Retrofit | 75.6% | 5.0% | 6.0% | 5.1% | 5.5% | 2.8% |
Output increased
The output was increased and the power consumption was reduced. The output and power consumption of P·042.5 grade cement before and after the transformation are shown in Table 5.
Table 5: Raw material consumotion table after upgrade
Project | Output/(t·h⁻¹) | Specific Surface Area/(cm²·g⁻¹) | Power Consumption/(kWh·t⁻¹) | 3 d Compressive Strength/MPa | 28 d Compressive Strength/MPa |
Before | 210 | 3500~3600 | 31.1 | 27.2 | 51.5 |
After | 250 | 3500~3600 | 27.8 | 29.1 | 52.3 |
Outcome of the Cement vertical roller mill modification/upgrade
Transformation benefits: Based on an annual cement production of 1.2 million tons and a 2.9% reduction in the clinker ratio, the project saved 3.96 million kWh of electricity and reduced clinker consumption by 34,800 tons, with direct benefits of nearly RMB 8 million. The project investment payback period was just over one year. In addition, CO emissions were reduced by approximately 30,000 tons due to electricity and clinker conservation.
Table3: Outcome of the Cement vertical roller mill modification/upgrade
Item | data | Item | Data |
Output | 250t/h | Grinding Mill Power | 4,200~4,500 kW |
Water Injection | 0 | Mill Pressure Difference | 4,300Pa |
Baffle Ring Height | 265mm* | Grinding Roll Linear Speed | 37 r/min |
Material Layer Thickness | 50~70mm | Powder Selector Power | 110~130 kW |
Effective Area of Air Ring | 3.85m²* | Powder Selector Speed | 68 r/min |
Horizontal Vibration Value | 3~5 mm/s | Windmill Baffle Opening | 100% |
Rod Chamber Pressure | 7.0~7.3 MPa | Windmill Power | 1,550~1,620 kW |
Rodless Chamber Pressure | 2.0~2.2 MPa | Hot Gas Temperature | 90℃ |
Other Vertical roller mill upgrade program/method:
FL-smidth Cement OK mill Raw Mill Vertical roller mill upgrade program:
This is the official upgrade description and method listed on Fl-smidth website: "The capacity of a vertical raw mill is often the limiting factor in the production of clinker, especially when a factory upgrades its kiln system, which can easily form a bottleneck. Compared with investing in a new vertical mill, the feasibility of gradually upgrading the capacity of an existing mill is limited. Although a moderate capacity increase can be achieved by upgrading the integrated classifier, the mature new solution launched by FLSmidth can significantly increase efficiency - integrating a specially designed hydraulic roller press (HRP) into the mill, combined with the existing classifier design, fan capacity and drying capacity, can increase capacity by up to 15%. It removes some waste from the classifier waste cone through the installation of a modified extraction screw conveyor, transports it to the HRP for separate grinding, and then returns it to the mill to participate in the material cycle. This upgrade solution saves energy and space and has a fast return on investment. No major modifications to existing equipment are required during installation, and downtime is short. If installed during a planned maintenance period, the construction period can be shortened. It usually only takes a few days to connect the HRP to the roller mill, and it is highly flexible: when additional capacity is required, the HRP and the roller mill operate in conjunction, and when not required, the roller mill can be operated alone. The HRP The mill can also run at normal capacity without interruption during maintenance, and HRP’s patented flexible baffle ring system ensures uniform loading across the width of the rollers even when handling fine-grained slag materials. This reduces maintenance work and ensures operational stability, allowing the plant to maintain the same specific power consumption (kWh/ton) after the upgrade as before the installation"
Comment: The differnece between the FL-smidth vrm upgrade and Tongli vrm upgrade.
The Difference is simple, the fl-smidth upgrade is an add-on system which will incraese 15%, investment is low, while the Tongli upgrade is more like a renovation, it increase the capacity by 40% or more but more parts will need to be changed or modified in the existing system. So to explain it better we write it down in 6 aspect:
The fundamental difference:
- The logic of TONGLI vertical roller mill upgrade is: by replacing high-efficiency powder selectors, adjusting classification speed and air volume, replacing new grinding roller materials, increasing grinding discs, and adding grinding rollers, the capacity improvement method is not to simply optimize a certain link, but to significantly improve the material throughput capacity of the entire system by increasing the key threshhold components. This type of upgrade solution is more suitable for situations where the clinker line is expanding, the original grinding system is close to the limit, or the mismatch between the new and old lines leads to insufficient raw material grinding.
- In contrast, the HRP integrated upgrade introduces a screw conveyor into the waste material circuit of the vertical mill powder selector, introduces some coarse particles into the HRP for independent grinding, and then returns it to the vertical mill to participate in the material circulation. This is equivalent to adding a "parallel booster system" to the original closed-loop system. "Explore the potential" in the existing vertical mill structure. This type of transformation usually has a low investment, a short construction period, and little interference with production. It is suitable for factories with slight capacity shortages or want to extend the service life of existing equipment. Its advantages are quick results and low risks, but the improvement is also relatively limited. Under normal circumstances, this type of optimization can bring a maximum capacity increase of 5-10%, and it depends on the original system fan, motor and drying capacity to have margin.
Rate of Return Perspect:
- From the perspective of return on investment, the risks and benefits of the two are also different. HRP upgrades have a short cycle, low investment, and a quick return. Generally, the investment can be recovered within half a year, which is suitable for users with tight budgets and short-term results.
- While the TONGLI upgrade of grinding rollers and powder selectors is in the millions or even tens of millions, it can increase the system capacity by 30-70% or even more, and the unit power consumption is reduced, and the energy consumption structure is optimized. Therefore, in factories with high electricity prices and tight production capacity, its payback period is not long, and generally positive cash flow can be achieved within 1-2 years.
Capacity Limitation:
- As an independent module, HRP is in a synergistic relationship with the vertical mill, and the operation can be switched: when the production capacity is not tight, the HRP can be shut down and the main mill can run alone; once the production needs to be increased or the HRP needs to be overhauled, the main mill can still maintain basic production alone, which provides greater flexibility and redundancy for the operation layer. However, due to the need for repeated trial adjustments between air volume balance, powder selection efficiency and grinding plate pressure, the system volatility is higher.
- TONGLI's all-round transformation is an all-round improvement of the vertical roller mill, which is equivalent to achieving a significant increase in production capacity at a relatively low cost, and is more suitable for customers with high production requirements, not just customers who are satisfied with a 15% increase.
As a cement plant owner which upgrade I should choose? which one fit me better?
In summary, If you want a 15% increase capacity within a short amount of time, the fl-smidth upgrade program is better. However if you want to expand your current cement production line to have a over 30% increase in capacity then the TONGLI vertical roller mill upgrade is more suitable. The essential difference between FLSmidth's and TONGLI's vertical mill upgrade strategies lies in "whether to tap the potential in the existing structure or to break through the structural limitations and introduce new paths." The former is suitable for local optimization and quick results, while the latter is suitable for capacity breakthroughs and structural upgrades. If the optimization of the grinding roller + powder selector is a minimally invasive surgery, then the integration of HRP is more like installing a "second heart" for the system.
Gebr. Pfeiffer VRM cement mill modernization & retrofitting upgrade
Pfeiffer provides official upgrade services for all ages of their mills (e.g., MPS series), focusing on modular retrofit components to improve performance, energy efficiency, and capacity. Solutions include: High-efficiency classifier replacements, boosting throughput and grind fineness. Grit extraction screws, hydraulic roll systems, liners. Full process audits and feasibility testing in their pilot stations
- Field reference: In 2016, Pfeiffer upgraded a VRM at Siniat Hartershofen — reusing existing foundation but installing a larger MPS 160 B mill alongside the old one
Pfeiffer provides comprehensive mill upgrades — classifier swaps, roll systems, screw conveyors — plus digital support to restore, optimize, or increase capacity in existing VRMs. They also extend service through digital tools (GPlink/GPpro) for predictive maintenance and optimization.
Thyssenkrupp Polysius: Booster Mill & Technology Forum
Polysius offers the polysius® Booster Mill, a supplemental agitated bead mill that operates in a separate milling stage. It provides up to 10–20% capacity increase and improved grind quality, with minimal footprint and downtime .This system is modular, dry grinding designed for upgrading existing ball or VRM circuits to meet higher quality needs or reduced clinker targets..They also host Technology Forums on VRM maintenance and upgrades, though these are educational rather than product-focused. Polysius’s Booster Mill is analogous to FLSmidth’s HRP—an external grinding module added to improve throughput or fineness, without replacing the core mill.
Loesche LM Series vertical roller mill upgrade service and program
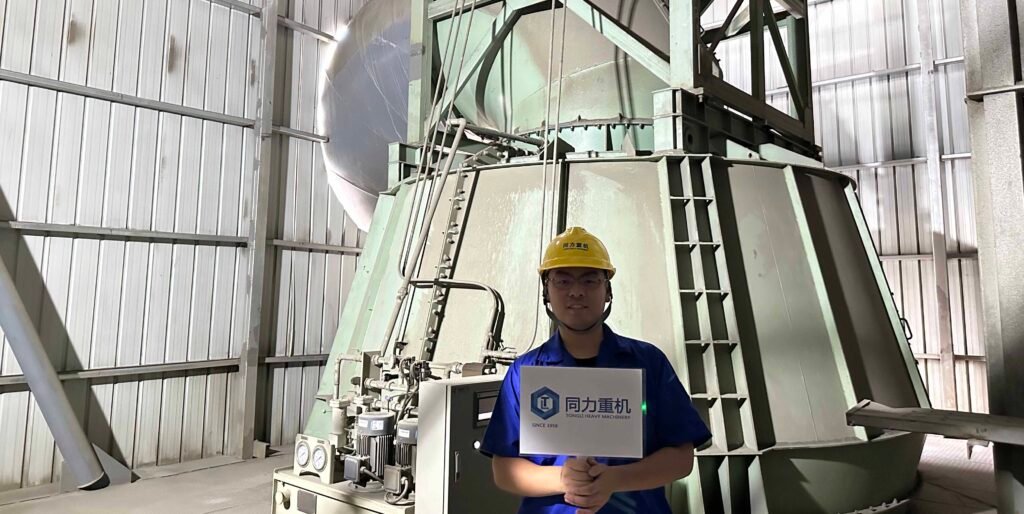
Loesche's vrm upgrade service also emphasis on 3 aspects: Powder selection, roller, transmission.
1. Classifier Retrofits – Dynamic High-Efficiency Classifiers
- Loesche provides retrofit services that replace static classifiers with their LSKS high-efficiency dynamic classifiers.
- In a notable coal-mill project (MPS 89), this retrofit improved throughput by 19.3%, reduced power consumption by over 10%, and sharpened fineness control.
- Upgrades are made precise using 3D laser scanning and factory-to-mill engineering to ensure perfect fit and minimal downtime .
2. Roller Configuration Upgrades – M+S Technology (Master + Support Rollers)
- Loesche's patented M+S roller setup introduces additional preparation rollers alongside main grinding rollers in configurations like 2+2, 3+3, or 4+4, depending on mill size.
- This modular design enhances grinding pressure, process flexibility, and product fineness control.
- For example, the 3+3 design in their LM 56.3+3 model achieved a 20% throughput increase with individual rollers ~40% lighter than previous models.
- Resulting systems benefit from better wear distribution, lower vibration, reduced maintenance, and up to 30–50% energy savings versus conventional mills .
3. Drive System Modernization – COPE Gearbox Retrofit
- Loesche introduced the Compact Planetary Electrical (COPE) gearbox, which replaces traditional gearboxes with multiple small electric drive units, eliminating the vulnerable first-stage gear.
- This upgrade is available for large mills (4,000–15,000 kW). Benefits include operational redundancy (single unit failure doesn’t affect production), rapid motor replacement (~2-hour downtime), and compatibility with existing foundations.
Vertical roller mill uprade reference project listed:
No. | Company | Location | VRM Type / Size | Retrofit Scope | Capacity After Upgrade |
1 | FLSmidth | USA – CalPortland, Mojave | OK 48‑4 (~250 stph) | Full mill replacement (retrofit) | ~60% capacity increase → 400 stph |
2 | FLSmidth | Bangladesh – Shah Cement | OK 62‑6 (largest cement VRM) | New installation | 640 tph (designed capacity) |
3 | FLSmidth | Bolivia – COBOCE | OK 43‑4 | New VRM installation | 130 tph |
4 | Loesche | Pakistan – DG Khan Cement | LM 56.3+3 | Dynamic classifier + M+S roller system upgrade | +20% capacity and energy gain |
5 | Loesche | India – Wonder Cement | LM 63.3+3 | Classifier + COPE gearbox retrofit | +18% capacity increase |
6 | Gebr. Pfeiffer | Germany – Siniat GmbH | MPS 160 B | New compact raw mill installation | +25% raw material throughput |
7 | Gebr. Pfeiffer | India – Shree Cement | MVR 6000 C‑6 | Separator & circuit optimization | +10–12% clinker throughput |
8 | Polysius | Vietnam – VICEM Hoang Mai | QUADROPOL QMR² 45/23 | Booster Mill add-on retrofit | +15% cement capacity |
9 | Polysius | Germany – CEMEX Rüdersdorf | QUADROPOL Raw Mill | Booster mill + fan upgrade | +10% capacity, –12% power use |
10 | Loesche | Nigeria – Dangote Obajana | LM 70.4+4 / LM 69.6 | New VRM additions | Significant capacity gain |
11 | FLSmidth | India – Orient Cement | Atox raw + 2 cement mills | Full grinding line retrofit | 6000 tpd line capacity |
12 | Loesche | India – Ramco Cement | LM 46.3+3 / LM 63.3+3 | 3 VRM installations with COPE drives | +20% cement output |
13 | Pfeiffer | Africa – undisclosed client | MPS series | Separator & recirculation upgrade | +15–20% (estimated) |
14 | FLSmidth | Europe – clinker line | OK series VRM | HRP press retrofitted into separator loop | +15% capacity |
15 | Polysius | Asia Pacific – unknown site | QUADROPOL | Booster system modular upgrade | ~+20% grinding output |
(FAQ)Frequently asked question/people also ask about vrm cement mill upgrade:
Q1: How to increase output of vertical roller mill?
Improving the output of vertical mills requires systematic optimization of process parameters and equipment configuration. Pre-crushing technology can be used to control the particle size of the material entering the mill to below 8mm, reducing the mill load; using a dynamic powder selector instead of a static powder selector, the classification efficiency is increased to more than 85%, reducing the powder return rate of the finished product; optimizing the grinding track of the grinding roller and the grinding disc, so that the material layer thickness is stable at 50-70mm, and the pressure of the hydraulic system is increased to 8-10MPa, which can significantly improve the grinding efficiency. In addition, increasing the wind speed of the wind ring to 90-100m/s and enhancing the material suspension capacity can increase the hourly output by 20%-30%. Through the above transformation, a cement plant increased the output of the LM56.3+3e/s vertical mill from 210t/h to 250t/h.
Q2: Best ways to reduce power consumption in VRM grinding
Reducing the power consumption of the vertical mill requires optimization of the entire energy conversion process. The main motor can be replaced with a permanent magnet synchronous motor, which increases the efficiency by 5%-8%; the planetary gearbox is used to replace the traditional reducer, and the transmission efficiency reaches more than 98%; the rotor structure of the powder selector is optimized to reduce the air resistance coefficient to below 0.3 and reduce reactive power loss. At the same time, the intelligent control system is used to achieve dynamic matching of the mill load and air volume, so that the system air leakage rate is less than 3%. Combined with the online monitoring technology of the material layer thickness, the unit power consumption can be reduced from 31.1kWh/t to 27.8kWh/t, reaching the international advanced level.
Q3: Vertical roller mill vs ball mill – which is more efficient after upgrade?
After upgrading, the energy efficiency advantage of the vertical mill significantly surpasses that of the ball mill. The vertical mill adopts the material bed extrusion principle, and the grinding efficiency is 40% higher than that of the ball mill. After upgrading the high-wear-resistant ceramic roller sleeve, the metal wear is reduced by 70%; the dynamic powder selector makes the finished product particle grading more concentrated, and the proportion of 3-32μm particles is increased to more than 75%. Even if the ball mill is upgraded to high-chromium steel balls and new liners, there are still problems such as high grinding medium consumption (0.8-1.2kg/t) and serious over-grinding. Actual measured data show that after upgrading the vertical mill of the same specification, the system power consumption is 35%-40% lower than that of the ball mill, the floor space is reduced by 50%, and the comprehensive operating cost is reduced by 25%.
Q4: What are the key components to upgrade in a vertical roller mill?
The key upgraded parts of the vertical mill cover mechanical and fluid systems. The grinding roller can be replaced with a modular structure, and the roller sleeve adopts a composite material (WC-Co coating), and the wear rate is reduced to below 0.05mm/kt; the dynamic powder selector is upgraded to a cage rotor, which can achieve a wide adjustment of 30-150r/min through variable frequency speed regulation, and the cutting particle size accuracy reaches ±1μm; the hydraulic system adopts proportional servo control, and the pressure fluctuation range is ≤±0.2MPa. In addition, the air ring adopts an adjustable blade design, the ventilation area adjustment range is ±20%, and the air flow distribution uniformity index is optimized to above 0.95.
Q5: How to improve product fineness in vertical roller mills?
Optimizing the fineness of the vertical mill product requires multi-dimensional coordinated control. By increasing the speed of the powder selector to 120-150r/min and increasing the number of rotor blades to 64, the cutting particle size d50 can be controlled at 10-12μm; adjusting the pressure difference between the inlet and outlet of the mill to 5-6kPa, the particle classification effect is enhanced; using a new anti-sticking inner guide plate to reduce the edge effect. At the same time, the moisture content of the material entering the mill is strictly controlled at 0.5%-1.0% to avoid paste grinding caused by excessive moisture. Combined with the PID intelligent control of grinding pressure and feed amount, ultrafine cement with a specific surface area of 420-450m²/kg can be stably produced, with the 3d compressive strength increased to more than 30MPa and the 28d strength reaching 55MPa.
Generally there are two ways to reduce the wear rate of grinding parts of vertical mills. High chromium alloy (Cr26 type) roller sleeves are preferred, with carbide content exceeding 40% in the metallographic structure, surface hardness reaching HRC62-65, and wear rate can be controlled below 0.1mm/kt; the grinding disc liner can be clad with tungsten carbide (WC particles account for 35%), and the wear resistance is improved by 2 times. At the same time, it is necessary to monitor the material layer thickness online (maintain 50-70mm) to avoid empty mill impact, set a superconducting iron remover (magnetic field strength ≥18000Gs) at the feed end to intercept metal impurities, and optimize the wind speed in the mill (85-95m/s) to reduce particle erosion and wear. After application in a 5000t/d production line, the roller sleeve life was extended from 8000 hours to 14000 hours.
The ROI of vertical mill upgrade is affected by the scale of production capacity and the depth of transformation, ranging from 25% to 45%, with a payback period of 1.5 to 3 years. Taking a 600,000-ton cement line as an example, upgrading the high-efficiency powder selector and frequency conversion drive system (investment of about $700,000) can reduce power consumption by 3.5kWh/t, increase output by 15t/h, save about $532,000 in electricity bills per year, and reduce maintenance costs by $112,000, with a comprehensive ROI of 42%. If the overall replacement of the grinding roller is involved, it is necessary to focus on evaluating the remaining service life of the equipment. When the main machine is used for more than 10 years, the ROI of the transformation is 15%-20% higher than that of the replacement of a new machine.
The cutting-edge technologies for vertical mill upgrades in 2025 are as follows: 1. Silicon carbide ceramic coating (SiC content ≥ 95%) roller sleeve, wear resistance is 3 times higher than that of traditional high chromium cast iron, and is suitable for high temperature conditions above 1000°C; 2. Direct-drive permanent magnet motor (efficiency 97.5%) with planetary gearbox, which saves 18% energy compared with traditional asynchronous motor system; 3. Digital simulation technology of flow field inside the mill (based on CFD modeling to optimize the wind ring angle, the airflow uniformity index is increased to 0.92); 4. Electrostatic grading powder separator (ultrafine powder separation efficiency reaches 90%, suitable for products with a specific surface area of 500m²/kg or more). But these 4 technology still need time to be proved.
The transformation of two-roller vertical mill to four-roller configuration requires mechanical upgrade, which can be divided into two situations. If you consider adding grinding rollers in the later stage and make the grinding disc larger and leave a margin, you can directly add grinding rollers. If there is no reserve, it is better to first expand the diameter of the grinding disc by 35%-40% from 4.6m to 6.2m, and simultaneously upgrade the power of the main reducer from 3150kW to 5600kW, and the basic bearing capacity needs to be increased to 2.3 times the original design. The hydraulic loading system needs to be expanded from dual-pump dual-circuit to four-pump independent control, and the pressure fluctuation accuracy is controlled at ±0.08MPa. According to Tongli's experience, after the LM46.2+2 two-roller mill is upgraded to LM56.4+4, the hourly output can be increased from 180t/h to 300t/h, but the transformation cost is about 65% of the new machine of the same specification, which is more suitable for production lines with prominent production bottlenecks and intact main frame structure.
The efficiency of the powder classifier directly affects the circulation load of the vertical mill and the quality of the finished product. When the classification efficiency of the dynamic powder classifier is increased from 75% to 88%, the content of particles >45μm in the finished product can be reduced from 12% to below 3%, the system powder return rate is reduced by 15%-20%, the corresponding mill output is increased by 8%-12%, and the power consumption is reduced by 4-6kWh/t. When the particle size fluctuation of the powder classifier is ±1.5μm, the deviation of the specific surface area of the finished product can reach ±30m²/kg. The new cage powder classifier can stabilize the proportion of 3-32μm particles at more than 70% through variable frequency speed regulation (20-180r/min) and adjustable vortex guide vanes, while reducing the power consumption of the powder classifier itself by 12%-15%.
Conclusion:
TONGLI has carried out structural transformation on cement vertical mill roller, powder selector, air ring, etc. according to the characteristics of PPC company's cement grinding mill. It has not only realized grinding without water spraying, but also reduced the clinker by 2.9%, increased the output by 19%, and reduced the unit power consumption by more than 3.3 kWh/t, achieving the purpose of increasing production, reducing consumption, saving energy and reducing carbon emissions. The most important thing is to reduce costs and increase the benefits of the entire production line. This is the most important thing, and it is real money in your pocket.